Lignocellulosic biomass has been used for the production of renewable fuels and chemicals. This has caused increasing attention due to shortage of oil reserves, enhanced fuel demand worldwide, increased climate concerns, and the inherent conflict between food prices and converting edible carbohydrates to ethanol or plant oils to bio-diesel [1]. Biomass is the most common form of renewable energy and generates very low net greenhouse emissions. The energy from biomass can be obtained by various techniques, such as combustion or by upgrading it into a more valuable fuel, gas or oil. Biomass can also be transformed into a source of value-added products for the chemical industry by using a thermochemical method such as pyrolysis of bio-oil. Nonetheless, several drawbacks of bio-oil severely limit its potential to replace or supplement high-grade transportation fuels. These include low heating values, high corrosiveness, high water content, thermal instability and immiscibility with hydrocarbon fuels, etc. [2]. Thus, bio-oil has to be upgraded before using it as a fuel. Moens et al. [3] pointed out that lignin compound will be formed in bio-oil after it is left for a few weeks or months. During storage the reactive components can interact to form larger molecules and altered its properties due to oxidation and thermal degradation.
Oxidation leads to polymerization resulting in an increase of viscosity. On the other hand, thermal degradation leads to partial decomposition of components and can result in loss of volatiles which further caused the bio-oil’s viscosity to increase. The High-Molecular-Mass (HMM) fraction of water-insolubles which are lignin-derived material will be increased due to polymerization and condensation reactions of carbohydrate constituents, aldehydes and ketones. Increment of HMM lignin fraction will increase the density of bio-oil as well. This phenomenon is due to the reason that of molecular weight increases during storage results from etherification and esterification occurring between hydroxyl, carbonyl and carboxyl group components. Condensation reactions in bio-oil will result in the formation of water as byproduct and further reduces its heating value [3].
Palm oil production is vital for the economy of Malaysia, which is the world’s second largest producer of the commodity. It covers about 59% of the world’s needs and 23% of Empty Fruit Bunch (EFB) can be obtained from the substantial fresh fruit bunch produced. Malaysia has generated a lot of oil palm biomass residues in the form of empty fruit bunch, mesocarp fibre, palm kernel shell and palm oil mill effluent [4]. Empty fruit bunch can be utilized as the feedstock for biomass pyrolysis. The reaction condition for the bio-oil used are 5 weight percent of H-Y zeolite catalyst at temperature of 500 °C and nitrogen flow rate of 100 ml/min [5], [6]. Catalytic pyrolysis offers some advantages over slow pyrolysis. The reaction can be improved and enhanced by the introduction of catalyst. Since pyrolysis requires the breaking of carbon-carbon bonds, the introduction of catalyst is able to catalyze the reaction and to facilitate the cracking reactions and de-oxygenation reaction, improve the quality of bio-oil produced compared to that of slow pyrolysis and thus the downstream upgrading processes is less expensive [7]. This process is able to remove oxygenated groups in bio-oil and improves the stability of bio-oil.
Introduction of catalyst in catalytic pyrolysis decreased the amount of organic yield (bio-oil) and increased the amount of gas yield, water content and Polyaromatic Hydrocarbons (PAHs) [8]. The oxygenated compounds in the bio-oil undergo dehydration, decarboxylation, cracking, aromatization, alkylation, condensation and polymerization with deoxygenation simultaneously [9]. Higher water content reduced the heating value of the bio-oil [10]. Besides, the most important factor driving the aging rate is temperature. Heating bio-oil to 60 °C or higher will promote internal reactions and polymerization that can be significant over a prolonged period [11]. Elevated temperatures increase the rate of the aging reactions, forming higher molecular weight compounds [12]. Solvents play an important role in maintaining the bio-oil’s stability. Organic solvents can also inhibit the chain of polymerization by converting the active units in the oligomer chain to inactive units which are acetone, biodiesel, ethanol, ethyl acetate and methanol [13].
Table 1 shows that the bio-oils have the following undesired properties for fuel applications when compared to petroleum fuel oil which has high water content, high viscosity and high oxygen content which leads to low heating value. These undesired properties have limited range of bio-oil application. The differences in processing conditions and feedstock result in significant differences in the product yield and product composition of bio-oils. Bio-oil is highly oxygenated, acidic and corrosive to common materials, thermally and chemically instable, as well as non-miscible with petroleum fuels due to its unique composition [14]. These fuel properties limited the bio-oil to be used directly only in boilers and furnaces. Bio-oil is hard to be directly used in diesel engines and gas turbines [15]. Various physical or chemical methods have been proposed to upgrade bio-oil.
Physical properties of bio-oil and petroleum fuel [16]
Physical properties | Value | ||
---|---|---|---|
Bio-oil (Jatropha) | Bio-oil (EFB) | Petroleum fuel | |
Moisture content [wt%] | 15.0-30.0 | 50.0 | 0.1 |
Heating value [MJ/kg] | 16.0-19.0 | 10.4 | 40.0 |
Viscosity at 40°C [cP] | 40.0-100.0 | 45.5 | 18.0 |
Carbon | 54.0-58.0 | 25.3 | 85.0 |
Hydrogen | 5.5-7.0 | 9.3 | 11.0 |
Oxygen | 35.0-40.0 | 64.6 | 10.0 |
Nitrogen | 0-0.2 | 0.3 | 0.3 |
Hence this research was aimed to stabilize the empty fruit bunch derived bio-oil by enhancing the properties of bio-oil such as water content and viscosity using solvents. The solvents used were ethyl acetate, acetone and ethanol of 95 vol% [13]. The chosen optimum conditions for aging of bio-oil were temperature of 80 °C and duration of 7 days [2], [13], [17]-[20]. The viscosity, water content and chemical compositions of the stabilized bio-oil were analyzed.
The source of empty fruit bunches was obtained from palm tree plantation area “Kilang Sawit FELCRA Berhad Nasaruddin, KM 37, Jalan Tronoh, 32600 Bota, Perak, Malaysia”. These empty fruit bunches were washed and dried in an oven at 100 °C for 3 days. The dried EFB was chopped and cut into smaller pieces. The sand and dust particles were cleaned by using water and then dried in the oven at 100 °C for 24 h. The dried EFB was then grinded with FRITSCH Cutting Mill to particle size below 500 µm. The grinded EFB was sieved to get the desired particle size of <500 µm. Table 2 shows the measured properties of EFB.
Properties of EFB (mf wt%)
Properties | Measured value |
---|---|
Ultimate analysis | |
Carbon | 46.830 |
Hydrogen | 6.277 |
Nitrogen | 0.664 |
Sulfur | 0.237 |
Oxygen (by difference) | 45.992 |
HHV [MJ/kg] | 19.643 |
Ultimate analysis of the EFB was carried out using LECO 932 CHNS Analyzer and the Higher Heating Value (HHV) was measured using IKA C5000 Bomb Calorimeter. The zeolite catalyst used in the catalytic pyrolysis was purchased from Sigma-Aldrich with surface area of 780 m2/g, 30 wt% of SiO2/Al2O3 and pore size of 7.4 × 7.4 Å [21]. The solvents (EMSURE® ACS) acetone and ethyl acetate were obtained from Merck KgaA whereas ethanol of 95 vol% was purchased from HmbG chemicals.
Semi-batch reactor
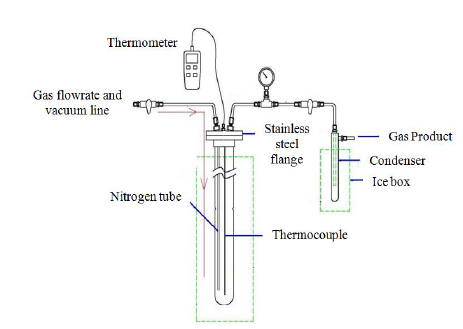
The reaction required about 35 min. The weight of the bio-oil produced was determined by measuring the difference between the weight of the condenser before and after the experiment. The liquid yield was calculated using eq. (1) below [22]:
The bio-oil obtained from all the experimental runs was stored in a container and placed in a refrigerator in order to slow down the rate of aging.
The chosen chemical solvents, ethanol of 95 vol%, acetone and ethyl acetate were mixed homogeneously with the bio-oil. The percentage changed in viscosity and water content of bio-oil, with and without solvents, after subjected to accelerate aging are presented in Figure 2 and Figure 3 respectively. Figure 2 shows that after the accelerated aging at 80 °C for 7 days, the percentage change in viscosity of bio-oil with solvents decreased compared to pure bio-oil. This indicated that the solvents were able to increase the stability of bio-oil. The percentages change of viscosity of bio-oil with ethyl acetate, acetone and ethanol were 64.60%, 79.09% and 38.31% respectively.
Percentage change in viscosity of bio-oil with and without solvents
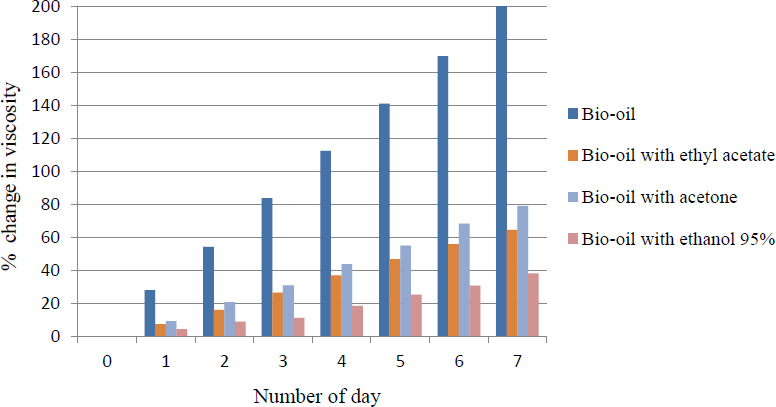
Based on Figure 3, the water content of bio-oil was reduced with the addition of solvents where the percentage changed of water content of bio-oil with ethyl acetate, acetone and ethanol of 95 vol% were 4.10%, 6.63% and 0.75% respectively. The results were comparable to the work of Osama et al. [23] as he investigated that by adding 2 wt%, 5%, 10%, and 20% of ethanol to a hardwood bio-oil and observed that the initial viscosity of the bio-oil at 50 °C decreased from 50 cost with absence of ethanol to 10 cost with presence of 20% ethanol. After aging at 50 °C for 7 days, the increased in viscosity of the neat bio-oil was 3.5 cost/day compared to 0.4 cost/day for a mixture of 5 wt% ethanol in bio-oil.
Percentage change in water content of bio-oil with and without solvents
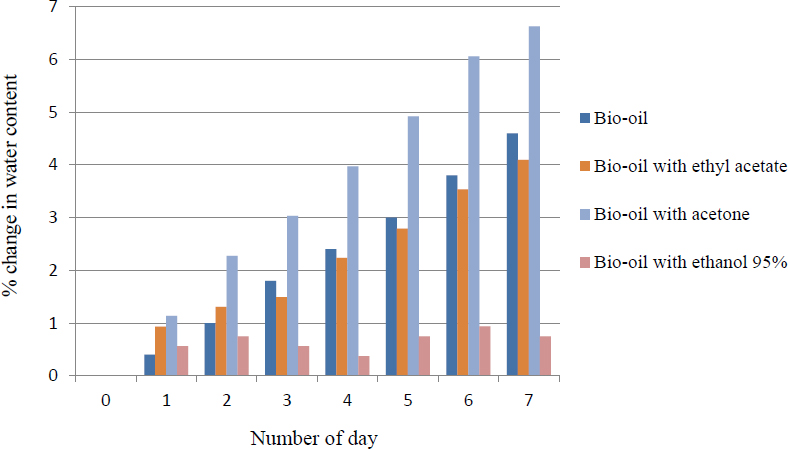
The effectiveness of solvent increased in the following order: acetone, ethyl acetate, and ethanol of 95 vol%. For bio-oil blended with solvents, no phase separation was observed after 7 days of accelerated aging. It showed that addition of ethanol to pure bio-oil inhibited phase separation. This was particularly important for bio-oil storage at high temperatures. Gas Chromatography-Mass Spectrometry (GC-MS) analysis was conducted on bio-oil with ethanol to identify the compounds that presence in the bio-oil.
Diebold [2] investigated that bio-oil with high molecular weight of hemiacetals, acetals, and esters would shift the equilibrium composition to a mixture with a lower molecular weight and viscosity by adding a low molecular weight alcohol. This could be important in stabilizing the bio-oil by four mechanisms which are reducing the concentration of reactive aldehydes, by converting more of them to less reactive, relatively low to moderate molecular-weight hemiacetals and acetals, transacetalizing large hemiacetals and acetals to form lower molecular weight hemiacetals and acetals, converting organic acids to low molecular weight esters and transesterifying large esters to form lower molecular weight esters. The second and fourth mechanisms could be considered to depolymerize the original high molecular weight hemiacetals, acetals, and esters. The chemical compositions of pure bio-oil and bio-oil with ethanol of 95 vol% were plotted in pie charts as shown in Figure 4 below.
Chemical composition of pure bio-oil (a); and bio-oil with ethanol of 95 vol% (b)
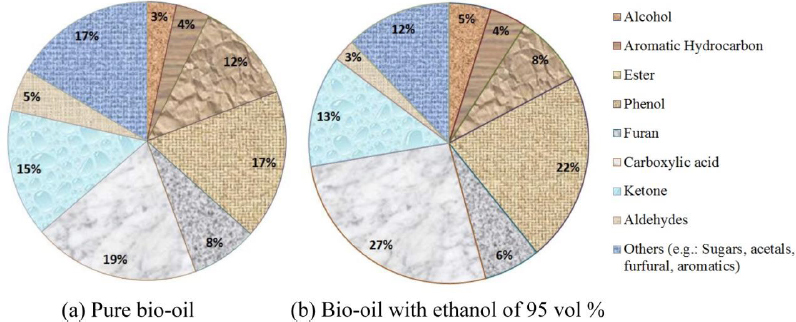
Figure 4 shows that adding ethanol of 95 vol% to bio-oil shifts the equilibrium composition of bio-oil towards more esters, acetals and water. The formation of esters and water from the reactions between carboxylic acids and ethanol was shown in the eq. (4) as follows:
Water was the most abundant compound present in pure bio-oil. Water was miscible with many of the oligomeric lignin derived components due to the solubilising effect of hydrophilic compounds. In addition, the water could not be removed by distillation as there was an azeotrope system formed between the carboxylic acid and water. Thus, conversion of low molecular weight acids into their corresponding esters allowed a large quantity of the water to be removed by distillation.
On the other hand, increased water content encouraged the hydrolysis of ester linked polymers to form lower-molecular-weight products such as furfural and furan. It also converted the reactants to inactive forms. The ethanol could react with the reactive sites in the oligomers that terminated polymerization. Likewise, polymeric esters were transesterified with alcohol to form a lower-molecular-weight methyl ester. The increased in molecular weights of these methyl esters and acetals were relatively low compared to the possible molecular weights that occurs in a real bio-oil with oligomeric hydroxy compounds reacting with oligomeric acids and aldehydes. This proved that addition of low molecular weight reactants reacts with oligomeric bio-oil components to form medium low molecular weight oligomers instead of high molecular weight polymers. Besides, aldehyde groups could also be converted to acetals which reduce the availability for polymerization. The results were analogous with the work of Etzkorn et al. [24]. He explored that unsaturated aldehydes such as acrolein could react with alcohol to form the alkoxy aldehyde, unsaturated acetal or alkoxy acetal according to the reaction shown in eq. (5) as follows:
where R is an alkyl group.
Addition of ethanol to bio-oil also inhibited phase separation as there was an absence of low-viscosity water-rich component on the top and a high-viscosity tar-rich layer at the bottom of the bio-oil which confirmed similar findings with the work of Oasmaa et al. [23]. He stated that the stability of bio-oil during storage increased by adding proper solvents.
The estimated bio-oil required for the study of stabilization was produced in 29 runs of experiment. The weight percentage of liquid yield for each run was calculated and tabulated in Table 3. The average liquid yield for catalytic pyrolysis of EFB in this research was 25.73 wt%.
Liquid yield (wt%) for catalytic pyrolysis of EFB
No. of run | Weight of biomass [g] | Weight of bio-oil produced [g] | Liquid yield [wt%] |
---|---|---|---|
1 | 15.01 | 3.86 | 25.72 |
2 | 15.00 | 3.91 | 26.07 |
3 | 15.02 | 3.87 | 25.77 |
4 | 15.02 | 3.88 | 25.83 |
5 | 15.03 | 3.88 | 25.82 |
6 | 15.04 | 3.86 | 25.66 |
7 | 15.03 | 3.85 | 25.61 |
8 | 15.01 | 3.82 | 25.44 |
9 | 15.01 | 3.84 | 25.58 |
10 | 15.00 | 3.85 | 25.67 |
11 | 15.03 | 3.86 | 25.68 |
12 | 15.04 | 3.81 | 25.33 |
13 | 15.01 | 3.88 | 25.84 |
14 | 15.02 | 3.90 | 25.97 |
15 | 15.02 | 3.91 | 26.03 |
16 | 15.04 | 3.87 | 25.73 |
17 | 15.03 | 3.85 | 25.62 |
18 | 15.03 | 3.82 | 25.42 |
19 | 15.03 | 3.81 | 25.36 |
20 | 15.05 | 3.80 | 25.25 |
21 | 15.02 | 3.91 | 26.03 |
22 | 15.01 | 3.92 | 26.12 |
23 | 15.01 | 3.86 | 25.71 |
24 | 15.00 | 3.87 | 25.80 |
25 | 15.00 | 3.87 | 25.80 |
26 | 15.00 | 3.85 | 25.67 |
27 | 15.00 | 3.84 | 25.60 |
28 | 15.02 | 3.89 | 25.90 |
29 | 15.00 | 3.90 | 26.00 |
Average liquid yield [wt%] | 25.73 |
In conclusion, the optimum condition for accelerated aging of bio-oil at 80 °C for 7 days had been applied. At this condition, solvents had been used to stabilize the bio-oil. The solvents used were able to improve the stability of bio-oil in terms of viscosity and water content during aging. The effectiveness of solvents increased in the following order: acetone, ethyl acetate and ethanol of 95 vol%. Organic solvent had great effect on both viscosity and water content of bio-oil. It could inhibit the chain of polymerization by converting the active units in the oligomer chain to inactive units. The solvent reacted to form higher low molecular weight products such as furfural and furan which resulted in lower viscosity and reduced the water content. Besides, addition of ethanol of 95 vol% also inhibited phase separation.
Biorefinery: Conversion of Woody Biomass to Chemicals, Energy and Materials ,J. Biobased Mater. Bioenergy , Vol. Vol. 2 , :100-1202008, https://doi.org/10.1166/jbmb.2008.302
, A Review of the Chemical and Physical Mechanisms of the Storage Stability of Fast Pyrolysis Bio-oils ,
, Study of the Neutralization and Stabilization of a Mixed Hardwood Bio-oil ,Energy and Fuels , Vol. Vol. 23 , :2695-26992009, https://doi.org/10.1021/ef8009266
, Waste-to-wealth: Green Potential from Palm Biomass in Malaysia ,Journal of Cleaner Production , Vol. Vol. 34 , :57-652012, https://doi.org/10.1016/j.jclepro.2012.04.004
, Bio-oils from Pyrolysis of Oil Palm Empty Fruit Bunches ,Am. J. Applied Sci , Vol. Vol. 6 , :869-8752009, https://doi.org/10.3844/ajassp.2009.869.875
, Studies on Catalytic Pyrolysis of Empty Fruit Bunch (EFB) using Taguchi’s L9 Orthogonal Array ,Journal of the Energy Institute , Vol. Vol. 87 , :227-2342014, https://doi.org/10.1016/j.joei.2014.03.008
, Production of Hydrocarbon Fuels from Biomass using Catalytic Pyrolysis under Helium and Hydrogen Environments ,Bioresource Technology , Vol. Vol. 102 , :6742-67492010, https://doi.org/10.1016/j.biortech.2011.03.104
, Comparison of Catalytic Pyrolysis of Biomass with MCM-41 and CaO Catalysts by using TGA-FTIR Analysis ,Journal of Analytical and Applied Pyrolysis , Vol. Vol. 89 , :171-1772010, https://doi.org/10.1016/j.jaap.2010.07.008
, Catalytic Pyrolysis of Biomass for Biofuels Production ,Fuel Processing Technology , Vol. Vol. 91 , :25-322010, https://doi.org/10.1016/j.fuproc.2009.08.011
, , Thermochemical Conversion of Biomass to Liquid Fuels and Chemicals , 2010, https://doi.org/10.1039/9781849732260
, Dynamotive; the Bio-oil Information Book , 2006
, Accelerated Aging of Bio-oil from Fast Pyrolysis of Hardwood ,Energy Fuels , Vol. Vol. 28 , :3224-32352014, https://doi.org/10.1021/ef500399n
, Towards Stabilization of Bio-oil by Addition of Antioxidants and Solvents, and Emulsification with Conventional Hydrocarbon Fuels ,The International Conference & Utility Exhibition , 2011, https://doi.org/10.1109/icuepes.2011.6497720
, Overview of Fuel Properties of Biomass Fast Pyrolysis Oils ,Energy Convers. Manag , Vol. Vol. 50 , :1376-13832009, https://doi.org/10.1016/j.enconman.2009.01.001
, Power Generation using Fast Pyrolysis Liquids from Biomass ,Renew. Sustain. Energy Rev , Vol. Vol. 11 , :1056-10862007, https://doi.org/10.1016/j.rser.2005.07.008
, Bio-oil Production via Fast Pyrolysis of Biomass Residues from Cassava Plants in a Fluidized-bed Reactor ,Bioresource Technology , Vol. Vol. 102 , :1959-19672010, https://doi.org/10.1016/j.biortech.2010.08.117
, Effect of Antioxidants and Additives on the Oxidation Stability of Jatropha Biodiesel ,Kasetsart Journal (Natural Science) , Vol. Vol. 44 , :243-2502010
, Storage Stability and Ageing Effect of Biodiesel Blends Treated with Different Antioxidants ,Energy , Vol. Vol. 36 , :369-3742011, https://doi.org/10.1016/j.energy.2010.10.029
, Bio-oils Obtained by Vacuum Pyrolysis of Softwood Bark as a Liquid Fuel for Gas Turbine, Part I: Properties of Bio-oil and its blends with Methanol and a Pyrolytic Aqueous Phase ,Biomass and Bioenergy , Vol. Vol. 19 , :337-3502000, https://doi.org/10.1016/S0961-9534(00)00043-X
, A Rapid Method for Evaluation of the Oxidation Stability of Castor Oil FAME: Influence of Antioxidant Type and Concentration ,Fuel Processing Technology , Vol. Vol. 90 , :1272-12772009, https://doi.org/10.1016/j.fuproc.2009.06.009
, One Step Thermal Conversion of Lignin to Gasoline Range Liquid Products by using Zeolites as Additives ,RSC Adv , Vol. Vol. 2 , :12892-128982012, https://doi.org/10.1039/c2ra22616b
, Investigation of the Effect of Metal Sites in the Me-Al-MCM-41 (Me = Fe, Cu or Zn) on the Catalytic Behavior during the Pyrolysis of Wooden Based Biomass ,Microporous and Mesoporous Materials , Vol. Vol. 105 , :189-2032007, https://doi.org/10.1016/j.micromeso.2007.05.059
, , Physical Characterisation of Biomass-Based Pyrolysis Liquids , Vol. 306 , :461997
, Acrolein and Derivatives in Kirk and Othmer’s Encyclopedia of Chemical Technology , Vol. Vol. 1 , :232-2511991
,