Global warming due to the increased concentration of Carbon dioxide (CO2) in the atmosphere, mainly from burning of fossil fuels, is a problem widely discussed worldwide. Several researchers are promoting efforts to reduce CO2 emissions through Carbon Capture and Storage (CCS) initiatives. CCS involves the adaptation of industrial facilities with a set of technologies to capture, transport, and store carbon in geological
formations. However, the main obstacle for its implementation is the absence of economic revenues for the additional capital and operational costs of such adaptation and to surpass technological gaps identified in carbon capture [1]. An alternative to mitigating CO2 emissions is Carbon Capture and Utilization (CCU), which uses photosynthesis to capture CO2 and convert it into biofuels, adding value to CO2 and substituting fossil fuels (oil, natural gas, and coal) [2].
The production of biofuels using microalgae as a feedstock (termed third generation biofuels) has been widely studied as an alternative to fossil fuels. Microalgae are highly productive and use less area for cultivation than terrestrial crops, and they can occupy soils unsuitable for food production, potentially managing the food-energy nexus [3]. Use of microalgae feedstock to produce renewable energy, through photosynthesis, recycling atmospheric CO2, can lead to a carbon neutral production-consumption cycle [4]. Biodiesel from microalgae is one of the most promising options of bio-CCU [5], due to its higher growth rate and lipid content, as well as real productivity compared with marine or terrestrial plants. However, the production of biofuels from microalgae faces a series of problems such as a high input of nutrients for growth, high energy consumption for harvesting, and dewatering of biomass and extraction of lipids, which must be overcome for the microalgae biodiesel industry to produce the required quantity of biofuel at competitive prices [4].
Current methods of liquid microalgae biofuel production generate approximately 60-70% residual biomass as by-product. Although residual biomass can have several destinations (e.g., food industry, aquaculture, bioethanol, and biohydrogen production, and bio-oil production via pyrolysis) [5], anaerobic digestion is a key process [6] that is amenable to large-scale applications. Anaerobic digestion of microalgae is an environmentally viable option to create a renewable energy source for industrial and domestic use. This process can be integrated into the production of biofuels derived from microalgae and wastewater treatment with microalgae, increasing its economic feasibility [7]. Production of biofuels by anaerobic digestion incorporated into biorefineries can reduce overall production costs, contributing to its economic feasibility and environmental sustainability [6].
Although the potential of biogas production from anaerobic digestion of microalgal biomass is recognized [6], it has received much less attention than liquid biofuels derived from microalgae. Nevertheless, increased interest has occurred in recent years [6] due to the advantages of anaerobic digestion over alternative technologies. From a process engineering view, the increased interest is because anaerobic digestion eliminates the need to dry the biomass. The energy intensive step of drying is the major bottleneck of microalga-based renewable energy. On the other hand, several studies report that increasing initial moisture content of mesophilic anaerobic digesters increased the methanogenic activity in high-solids sludge digestion [8].
Furthermore, anaerobic digestion does not require pure cultures and a specific fraction of the biomass is not an essential production goal [6]. Unlike biodiesel, which requires high lipid content (favored by nutritional stress and consequently reduced growth rate), selecting a particular microalga species for biogas production should target mainly high specific growth rates. In industrial terms, anaerobic digestion of solid wastes can be seen as a mature technology [8]. Biogas by anaerobic digestion of residual microalgal biomass (after extraction of lipids or other bio-components of interest) has the side benefit of the recovery of essential nutrients, as well as the possibility of using wastewaters in the microalgae growth step. Integrated biogas and biodiesel has potential for increasing sustainability of microalgal biofuels [9]. When these processes are integrated and operated simultaneously, the benefits of microalgae biofuel production and energy production through wastewater treatment are significantly increased [4].
However, anaerobic digestion of microalgae biomass has several technical constraints, including low concentrations of biodegradable digestible substrate, recalcitrant constituents, difficult degradability of cell wall, low carbon/nitrogen ratio, ammonia toxicity and salinity effects, and associated metal ions [7]. Another point to be highlighted in the anaerobic digestion of microalgae is the number of species studied and the difficulty of comparing the results according to the different applied pretreatments, co-digestion with other wastes and extraction of microalgae lipid before the anaerobic degradation [10], [11]. Thus, it is important to expand studies of anaerobic degradation of microalgae biomass, particularly due to the different results obtained with different species and operating conditions, both in the cultivation of microalgae and in the anaerobic digestion stage.
Several technologies have been developed to overcome the disadvantages of anaerobic digestion of microalgae, with emphasis on pretreatment of algal biomass [6], [10]. Pretreatment promotes the rupture of the cell wall of the microalga, which facilitates the access of the methanogenic archaea to the intracellular material of the microalgae. In addition, pretreatment promotes cleavage of the intramolecular bonds of the intracellular material, decreasing the size of biomolecules, which increases solubility and leaves them more susceptible to digestion [12]. In anaerobic digestion of the integral and residual biomass, pretreatment can significantly and efficiently increase the methane conversion yield. However, the energy required for biomass pretreatment may exceed the energy obtained from the produced methane [13], [14]. Thus, pretreatment methods should avoid use of chemical or biochemical (e.g, enzymes) inputs as they considerably diminish economic performance. Another reason for replacing sulfuric acid with CO2 is the reduction of sodium and sulfate concentrations in the anaerobic digestion stage, reducing inhibition over methanogenic microorganisms. An original contribution of the present work is to explore the potential of using CO2 as agent (or co-agent) of acid hydrolysis. It is worth noting that supercritical CO2 in biomass pretreatment has been suggested [15], but is economically unfeasible when applied to bulk production of low value products such as biofuels.
The work employs Scenedesmus obliquus, a species that readily adapts to heterotrophic growth, which allows wastewater to be used as source of carbon and nutrients [7], sustainably approaching the water-energy nexus and eliminating the burden of expensive fertilizers. The use of municipal wastewater as algal growth medium is attractive due to the presence of organic carbon and inorganic nutrients, including nitrogen and phosphorus.
Given the relevance of an integrated scenario for biofuel production, the possible use of wastewater for biomass production and the need of biomass pretreatment to release intracellular content, this work aims to assess pretreatment methods for the anaerobic digestion of microalgal biomass, applied to Scenedesmus obliquus. Different hydrolysis methods (mechanical, thermal, thermochemical) are evaluated for the solubilization of biomass aiming to select the most efficient hydrolysis method in terms of Specific Methane Production (SMP). Furthermore, the work presents an analysis of energy efficiency of pretreatment methods. Lastly, the work proposes an original hydrolysis method, which replaces the consumption of sulfuric acid and eliminates the energy demand of conventional thermochemical pretreatment through the injection of flue gases, directly increasing the temperature with waste heat and providing CO2 for combined chemical and thermal effects.
Scenedesmus obliquus biomass was provided by the Laboratory of Applied Studies in Photosynthesis of Federal University of Rio de Janeiro - LEAF/UFRJ. This species was selected because it is one of the most studied in the literature, for biodiesel and biogas production and because it has a rigid cell wall and difficult degradation [14], [16].
Microalgae were cultivated, concentrated by centrifugation and sent to the Environmental Technology Laboratory for pretreatment studies. After removal of aliquot for characterization, the suspensions were stored at 4 °C.
Concentrated microalgal biomass was characterized in terms of pH, total Chemical Oxygen Demand (CODT), soluble Chemical Oxygen Demand (CODS), total solids and Volatile Solids (VS) [17], as shown in Table 1. Suspensions of the concentrated biomass were diluted in distilled water to an initial CODT of 4–7 kg/m3 in the anaerobic digestion and pretreatment experiments.
Characteristics of concentrated fresh biomass
Parameter |
Value |
---|---|
pH |
6.9 ±0.5 |
Total COD [kg/m3] |
15.0 ±3.4 |
Soluble COD [kg/m3] |
0.9 ±0.3 |
Total solids [kg/m3] |
22.6 |
Volatile solids [kg/m3] |
21.3 |
Three pretreatment methods of the microalgae biomass were evaluated: thermal, thermochemical and mechanical, as described below. After each pretreatment, the microalgae suspensions were filtered through membranes with pore size of 0.45 μm and soluble COD was determined in the filtrate. The results were analyzed based on the increase of soluble COD in the biomass suspension. Each condition was assessed in two replicates and the averages shown in the results.
5 ml of microalgae suspension were transferred to 10 ml test tubes with screw cap and submitted to temperatures of 60, 80, 100 and 150 °C for 20 to 120 min. Hydrolysis in an autoclave (relative pressure of 101.3 kPa, 121 °C, 20 min) was also evaluated using 30 ml of microalgae suspension in 250 ml glass bottle with screw cap.
5 ml of microalgae suspension were transferred to 10 ml test tubes with addition of Sulfuric acid (H2SO4) to a concentration of 0.2 or 0.1% (v/v), Sodium hydroxide (NaOH) to a concentration of 0.2% (w/v), or CO2 to reach pH 2 (by bubbling the gas released from the neutralization reaction of Sodium bicarbonate [NaHCO3] solution with H2SO4). After acidification, the tubes were submitted to digestion at 150 °C for 60 min.
About 5 ml of algal biomass suspension were placed in glass tubes with screw cap (8.4 × 1.5 cm) with 1 g glass beads (mean diameter of 3 mm) and submitted to vortexing for 5 min.
Biomass suspensions (raw or pretreated) had their pH adjusted to 7.0 with NaHCO3 and were supplemented with nitrogen and phosphorus sources (Ammonium chloride [NH4Cl] and Potassium dihydrogen phosphate [KH2PO4], respectively) to a COD:N:P ratio of 350:5:1. Experiments were conducted on 100 ml penicillin flasks containing 50 ml of mixture composed of diluted biomass suspension and anaerobic sludge (10% v/v) sealed with rubber plugs and aluminum seals coupled to plastic syringes for measuring biogas volume. The sludge used as inoculum was collected in an anaerobic reactor operating in a poultry processing industry (VS 22 kg/m3). Flasks were incubated at 30 °C without agitation to stabilize biogas production. Each condition was assessed in five replicates and the average values shown in the results.
The energy input (Ein) required by the thermochemical pretreatment was calculated through the association of eq. (1) and (2) [13], [18]. Eq. 1 gives the energy demand for heating the biomass from the room temperature to the pretreatment temperature, including the energy necessary to maintain the system at the operation temperature during all the pretreatment time. The density (ρ) and the specific heat (γ) of microalgae suspension were assumed to be the same as those of water. The wall surface area of the reactor was calculated considering a reactor with a useful volume of 1.5 L and height/diameter ratio of 2. The calculation was performed based on the useful volume, excluding the surfaces of the reactor tops, totaling 0.061 m2 [14]:
where Ein is the energy input (kJ/g VS), ρ is the density of microalgae suspension (1 kg/L), V is the volume of microalgae suspension submitted to the pretreatment (L), γ is the specific heat of microalgae suspension (4.18 kJ/kg°C), Tp is the temperature of pretreatment (°C), To is the room temperature (25 °C), mVS is the weight of biomass submitted to the pretreatment (g VS or g COD), κ is the heat transfer coefficient (1 W/m2°C), A is the reactor wall surface area (m2) and t is the pretreatment duration time (min).
Eq. (2) provides the energy equivalent to the cost of reagents used in the pretreatment [14]. The price of sulfuric acid (USD 0.012/ml) was obtained from marketing sites of chemical reagents for academic purposes. The reciprocal commercial electricity rates (Pe) were calculated based on the average trading price of energy in Brazil, from January to December 2015, provided in the Report of the National Electric Energy Agency. The average rate for commercial consumption was USD 122.87/MWh in that period. Hence the rate was USD 3.4 × 10–5/kJ (Pe is 29,299 kJ/USD):
where VR is the volume of sulfuric acid (ml), YR is the sulfuric acid price (USD/ml), Pe is the reciprocal commercial electricity rates (kJ/USD), CS is the concentration of microalgae suspension (g VS/L) and V is the volume of microalgae suspension submitted to the pretreatment (L).
The energy output (Eout) obtained with the increase in methane production was calculated using eq. (3) [14]:
where Eout is the energy output (kJ/g VS), η is the recovery of methane efficiency = 0.9 [19], ΔΡ is the increase in methane production after pretreatment (ml CH4g VS applied) and ξ is the lower heating value of methane = 35.8 kJ/L CH4 [20].
Thermal pretreatment results are presented in Figure 1a, which shows a greater solubilization of COD at 150 °C and 60 min, with a percentage of soluble COD 10 times higher in the digested (23.2% average) compared to the fresh biomass (2.3% average). The combination of temperature and pressure (121 °C/101.3 kPa for 20 min in autoclave - Figure 1a) did not change the results obtained at 150 °C at the same digestion time. Thus, autoclaving was abandoned, the temperature maintained at 150 °C and longer digestion times were investigated. Figure 1b indicates that, within 60 min, maximum COD solubilization was achieved.
Effect of thermal pretreatment on biomass COD solubilization: effect of temperature for 20 and 60 min of hydrolysis (a); effect of hydrolysis time at 150 °C (b)
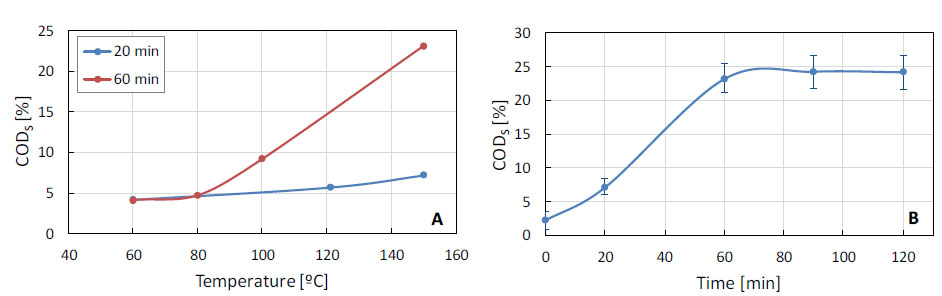
In the best condition for thermal pretreatment – 150 °C/60 min, the soluble COD values in the digestate were very low (1,356 mg/L, on average, for total COD of 5,732 mg/L). Thus, the combined effect of temperature (150 °C) and acid or base on the biomass digestion was evaluated for 60 min, obtaining the results presented in Figure 2. The combination of temperature and acid (0.2% v/v) showed better solubilization than with base (0.2% w/v) yielding 36.9% and 16.9% of soluble COD, respectively. The reduction in acid concentration from 0.2 to 0.1% (v/v) did not change the acid solubilization potential, with digested biomass containing 37.5% of soluble COD.
Effect of thermochemical pretreatment (150 °C/60 min with chemicals added) on biomass COD solubilization
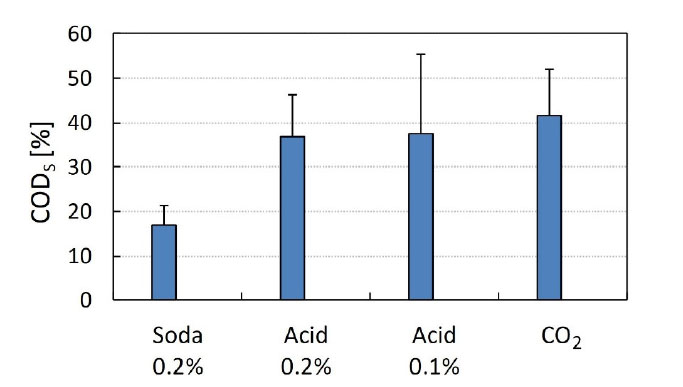
The effect of initial biomass concentration in the hydrolysis condition with acid 0.2% v/v and 150 °C for 60 min was evaluated on COD solubilization (Figure 3b). The soluble COD increased linearly with the initial biomass concentration (measured as total COD), generating up to 386 kg of soluble COD for every 1 ton of initial total COD (or 253 kg of volatile solids). The same increase in initial concentration of biomass in the control condition (no hydrolysis) led to negligible increases in soluble COD, generating only 58 kg COD soluble per ton of total COD (Figure 3a). However, the percentage of soluble COD of each experiment remained virtually constant (between 33 and 42%), which indicates that the hydrolysis rate is maintained regardless of the concentration of biomass employed. This result is consistent with the concentration of biomass for reuse of the culture medium and the reduction of volume and area occupied by the hydrolysis tank.
Effect of initial biomass concentration on COD solubilization without (a) and with (b) hydrolysis
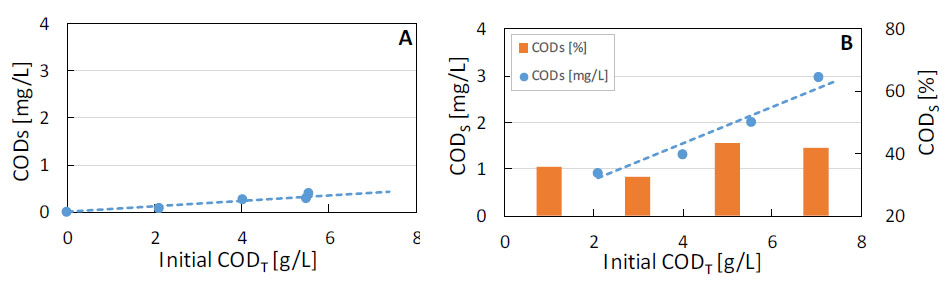
The mechanical treatment (shaking with glass beads) was evaluated as an adjuvant to the thermochemical treatment at 150 °C, 0.1% acid for 60 min. The COD solubilization results presented in Figure 4 show that the mechanical treatment did not improve biomass hydrolysis, suggesting that the solubilization of biomass occurs exclusively due to the effect of acid and temperature.
Effect of mechanical treatment on COD solubilization
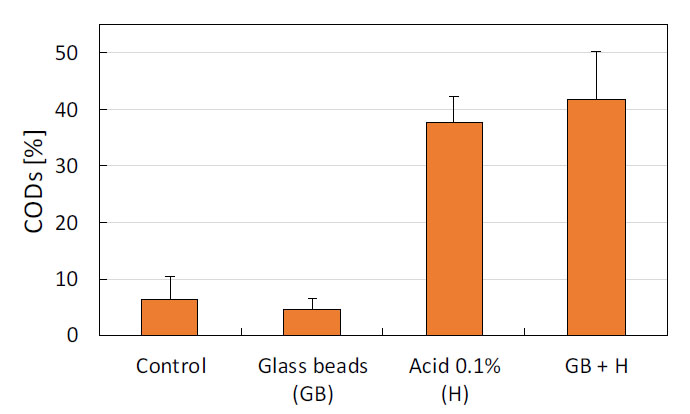
Two pretreatment conditions were selected to evaluate the anaerobic biodegradability: hydrolysis with acid 0.1% (v/v) at 150 °C for 60 min and 120 min. The results obtained with various biomass samples submitted to the selected pretreatments are displayed in Figure 5 and Table 2 together with digestion of fresh biomass without hydrolysis (Control). Hydrolysis with acid addition and heating for 60 min obtained higher biogas production, with total biogas volume 1.5 times higher than fresh biomass. There was lack of lag phase and similar initial biogas production rates in the three conditions. Biogas production stabilized within 6-8 days of incubation, resulting in biogas yields of 97.5, 146.4, and 61.3 mL/Lday for fresh biomass and biomass hydrolyzed for 60 min and 120 min, respectively.
Biogas production at 30 °C under different biomass treatment conditions
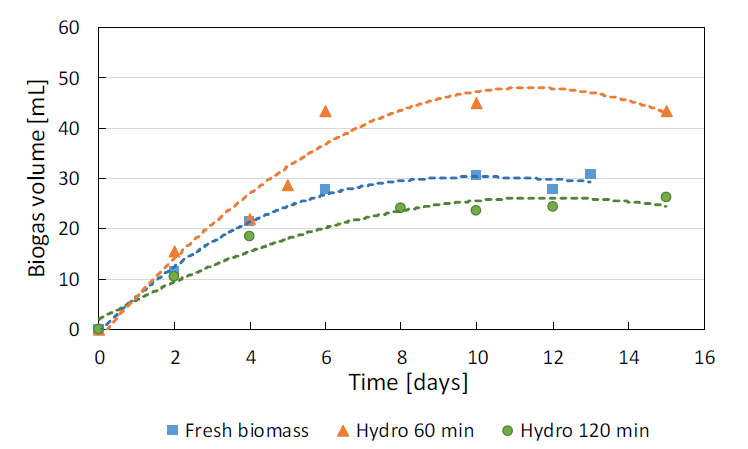
Biodegradability tests results (30 °C/15 d) with fresh biomass (control) and biomass hydrolyzed with acid 0.1% (v/v) at 150 °C, for 60 min and 120 min
Condition |
CODtinitial[g/L] |
CODsinitial[g/L] |
CODsfinal[mg/L] |
CODsremoval [%] |
Biogas [mL, 30 °C] |
CH4 [%] |
SMP |
---|---|---|---|---|---|---|---|
Controla |
7.20 ±0.33 |
0.61 ±0.25 |
173 ±32 |
72.8 ±5.4 |
29.3 ±6.0 |
41.4 ±1.4 |
130.9 ±26.0 |
Hydrob |
7.12 ±0.37 |
1.44 ±0.32 |
323 ±121 |
79.5 ±5.4 |
48.8 ±11.9 |
46.5 ±0.7 |
253.1 ±50.8 |
Hydroc |
6.00 ±0.13 |
1.55 ±0.92 |
379 ±209 |
75.1 ±3.8 |
39.7 ±7.2 |
45.0 |
224.8 ±27.6 |
Higher SMP was also obtained with biomass hydrolyzed with acid 0.1% (v/v) at 150 °C for 60 min, almost doubling the SMP for fresh biomass digestion, which confirms that this condition is the best biomass pretreatment. A comparison of results in the literature that used the same microalga (Scenedesmus obliquus) reveals similar values for fresh and previously hydrolyzed biomass. Ometto et al. [14], for example, obtained 162–259 mL CH4 STP/g VS [Standard Temperature and Pressure (273 K, 101.3 kPa) (STP)] after heating at 105–165 °C for 30 min. While Mussgnug et al. [21] and Zamalloa et al. [16] obtained 178 and 210 mL CH4 STP/g VS, respectively, with fresh biomass.
Even after pretreatment, cumulative methane yields in the anaerobic digestion step are still below expectations. Part of this poor performance can be attributed to high concentrations of sulfate and sodium (added as NaHCO3 to neutralize pH after acid hydrolysis), which can act as inhibitors in the metabolism of methanogenic archaea, reducing methane production [22].
Average ± standard deviation of 6a, 5b and 4c experiments. Hydrob is the biomass hydrolyzed for 60 min. Hydroc is the biomass hydrolyzed for 120 min. CODT is the total chemical oxygen demand. CODS is the soluble chemical oxygen demand. SMP is the specific methane production, mL CH4 (STP)/g VS applied.
Applying eq. (1) and (2) and adding their results, a total energy input (Ein) of 501.34 kJ/g VS was obtained. The energy output (Eout) calculated through eq. (3) was equal to 3.94 kJ/g VS. Thus, it can be concluded that the pretreatment is not economically viable, because it demands more energy than the resulting increase obtained in methane production.
One reason for this result is the low concentration of volatile solids (1.78 g VS/L) used in the experiment, which involves a large energy demand to heat a large volume of diluted biomass. However, the minimum concentration for the method to be viable (Ein < Eout) is 226.25 g VS/L, calculated through eq. (1) and (2). This value is well above those reported in the literature, therefore, other operation parameters must be optimized.
Although biogas produced in the anaerobic digestion can be used to generate electrical or thermal energy on-site to supply its energy demand (from biomass processing and extraction processes), other alternatives should be sought to increase energy performance. For instance, the effluent from the anaerobic digester could be concentrated in solar assisted drying equipment, to reduce use of thermal energy supplied by biogas combustion. Concomitantly, sulfuric acid could be replaced with carbonic acid (by bubbling CO2 up to pH 2) to reduce the energy input of pretreatment. In fact, flue gas (containing CO2 and other acid gases at high temperature) may be used for hydrolysis of the residual biomass of microalgae from photobioreactors for CO2 capture, thus helping to minimize operational costs (e.g., energy consumption and chemical input). Another reason for replacing sulfuric acid with CO2 would be the reduction of sodium and sulfate concentrations in the anaerobic digestion stage. The acidification with CO2 provided results similar to those obtained with sulfuric acid, with 41.6% of soluble COD (Figure 2).
Although the experiments are preliminary (conducted on bench scale) and still require further studies to consolidate the technical feasibility of the hydrolysis method proposed by flue gas injection at industrial scale, results suggest the potential of biomass pretreatment employing exhaust gases. In addition, it is known that different biomasses behave differently when submitted to the same treatment conditions, which is due to the distinct chemical composition of the microalgae. Nevertheless, hydrolysis with CO2 injection and temperature with Spirulina maxima biomass significantly increased the soluble COD fraction of the biomass suspension after hydrolysis (from <1% to 19%). This hydrolyzed biomass had a higher biogas production rate than the non-hydrolyzed biomass. Further experiments are being conducted to increase biomass concentration and reduce salt interference from microalgae culture medium in CO2 solubilization, with different operational parameters investigated to improve hydrolysis efficiency.
Considering that lipid extraction would result in additional energy penalty (as a dry biomass is required), digestion of integral biomass is recommended in the production arrangement displayed in Figure 6, which results in null blue water footprint. It is worth noting that the CO2 driven acidification of biomass fed into the biodigester provides further potential of reducing Global Warming Potential (GWP). Additional environmental benefits include the reduction of COD and macronutrients (N and P) from wastewater (producing the WATER stream in Figure 6).
Conceptual block diagram of integrated Biomass Growth – Digestion, with waste heat recovery from flue gas
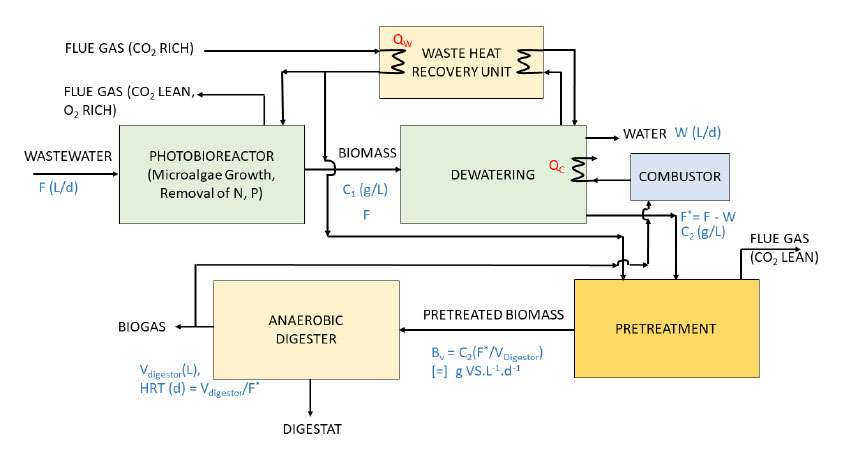
Thermochemical hydrolysis with biomass acidification using CO2 showed the best COD solubilization results among the investigated alternative methods. The anaerobic digestion of hydrolyzed biomass exhibited higher biogas yields compared to fresh biomass without hydrolysis. Biogas production stabilized within 6–8 days of incubation, resulting in biogas yields of 97.5, 146.4, and 61.3 mL/Lday for fresh biomass and biomass hydrolyzed for 60 min and 120 min, respectively. However, the energy penalty from pretreatment overrides the benefit of increased biogas productivity, a total energy input of 495.11 kJ/g VS was obtained, demanding additional process innovations to achieve economic feasibility. Among possible alternatives, this work suggests using waste energy from flue gas and substitution of sulfuric acid with CO2 as acidification agent, which would result in additional potential of CO2 utilization.
Carbon Capture and Storage Technologies: Present Scenario and Drivers of Innovation ,Curr. Opin. Chem. Eng. , Vol. Vol. 17 , :22-342017, https://doi.org/10.1016/j.coche.2017.05.004
, Atmospheric CO2 Capture by Algae: Negative Carbon Dioxide Emission Path ,Bioresour. Technol , Vol. Vol. 215 , :371-3792016, https://doi.org/10.1016/j.biortech.2016.03.060
, Managing the Food, Water, and Energy Nexus for Achieving the Sustainable Development Goals in South Asia ,Environ. Dev. , Vol. Vol. 18 , :14-252016, https://doi.org/10.1016/j.envdev.2015.12.001
, New Insights into Algae Factories of the Future ,Renew. Sust. Energ. Rev , Vol. Vol. 81 (Part 1), :643-6542018, https://doi.org/10.1016/j.rser.2017.08.024
, Bio-mitigation of Carbon Dioxide Using Microalgal Systems: Advances and Perspectives ,Renew. Sust. Energ. Rev , Vol. Vol. 76 , :1163-11752017, https://doi.org/10.1016/j.rser.2017.03.065
, Biogas from Microalgae: Review on Microalgae’s Cultivation, Harvesting and Pretreatment for Anaerobic Digestion ,Renew. Sust. Energ. Rev. , Vol. Vol. 75 , :692-7092017, https://doi.org/10.1016/j.rser.2016.11.045
, Recent Progress in Microalgal Biomass Production Coupled with Wastewater Treatment for Biofuel Generation ,Renew. Sust. Energ. Rev. , Vol. Vol. 79 , :1189-12112017, https://doi.org/10.1016/j.rser.2017.05.091
, Enhanced Anaerobic Digestion of Organic Waste ,
, Integrated Biodiesel and Biogas production from Microalgae: Towards a Sustainable Closed Loop through Nutrient recycling ,Renew. Sust. Energ. Rev. , Vol. Vol. 82 (Part 1), :1137-11482018, https://doi.org/10.1016/j.rser.2017.09.091
, Anaerobic Digestion of Algae Biomass: A Review ,Algal Res , Vol. Vol. 5 , :204-2142014, https://doi.org/10.1016/j.algal.2014.02.001
, Anaerobic Digestion of Microalgae: The benefits of Digesting Microalgae Waste ,Curr. Biochem. Eng. , Vol. Vol. 3 (No. 3), :210-2222016, https://doi.org/10.2174/1570180813666160527114809
, Pretreatment of Microalgae to improve Biogas production: A Review ,Bioresour. Technol. , Vol. Vol. 172 , :403-4122014, https://doi.org/10.1016/j.biortech.2014.08.114
, Microalgae Conversion to Biogas: Thermal pretreatment contribution on Net Energy Production ,Environ. Sci. Technol , Vol. Vol. 48 (No. 12), :7171-71782014, https://doi.org/10.1021/es500982v
, Impacts of Microalgae pre-treatments for improved Anaerobic Digestion: Thermal treatment, Thermal Hydrolysis, Ultrasound and Enzymatic Hydrolysis ,Water Res , Vol. Vol. 65 , :350-3612014, https://doi.org/10.1016/j.watres.2014.07.040
, Carbon Dioxide in Biomass Processing: Contributions to the Green Biorefinery Concept ,Chemical Rev. , Vol. Vol. 115 (No. 1), :3-272015, https://doi.org/10.1021/cr500330z
, Anaerobic Digestibility of Scenedesmus obliquus and Phaeodactylum tricornutum under Mesophilic and Thermophilic Conditions ,Appl. Energy , Vol. Vol. 92 , :733-7382012, https://doi.org/10.1016/j.apenergy.2011.08.017
, , Standard Methods for the Examination of Water and Wastewater, APHA – American Public Health Association, American Water Works Association, Water Pollution Control Federation , 2005
, Evaluation of Thermal, Ultrasonic and Alkali pretreatments on Mixed-Microalgal Biomass to enhance Anaerobic Methane Production ,Bioresour. Technol , Vol. Vol. 143 , :330-3362013, https://doi.org/10.1016/j.biortech.2013.06.017
, Improving Anaerobic Sewage Sludge digestion by implementation of a Hyper-Thermophilic Prehydrolysis Step ,J. Environ. Manage , Vol. Vol. 88 (No. 4), :881-8892008, https://doi.org/10.1016/j.jenvman.2007.04.020
, , Design of Thermal Oxidation Systems for Volatile Organic Compounds , 1999
, Microalgae as Substrates for Fermentative Biogas Production in a Combined Biorefinery System ,J. Biotechnol , Vol. Vol. 150 (No. 1), :51-562010, https://doi.org/10.1016/j.jbiotec.2010.07.030
, , Anaerobic Technology for Industrial Wastewaters, Archae Press, Nashville, USA , 1996
,