Cement is one of the widely used materials, one of the most energy intensive industries, and one of the main contributors to carbon dioxide (CO2) emissions on a global level and in China. Cement industry is responsible for about 7% of the global CO2 emissions and the third largest industrial energy consumers [1]. It is also responsible for about 10% of the total CO2 emissions in China [2]. China produces more than 60% of global cement, which is mainly driven by the economic, population, and urbanization growth.
Several studies have analysed cement demand and production in different countries including China. Zhang et al. [3] have analysed the change of cement production or demand based on the economic and social factors. Based on econometric techniques, Uwasu et al. [4] found an inverted U-shape relationship between per capita Gross Domestic Product (GDP) and cement production, and per capita cement production in East Asia and North America peaked at about 500 kg, in the EU at 531 kg, while in China it was more than twice that in the EU. García-Gusano et al. [5] put forward that Spain's cement demand had fallen to its lowest level in 2014 as a result of the economic crisis, and was expected to increase gradually thereafter, reaching 25 Mt and 29 Mt in 2030 and 2050, respectively. Using the extended Stochastic Impacts by Regression on Population, Affluence and Technolog (STIRPAT) model, Cao et al. [6] found that fixed investment and per capita GDP were decisive factors of cement consumption in China, and there was an inverted U-shape relationship between cement consumption and urbanization level, as well as per capita GDP. Some scholars pointed out that the peak of cement consumption in China will come before 2020. Li et al. [7] and Li et al. [8] predicted that China's cement production would peak at 2.5 billion tons in 2017, and then gradually decline, to 2.3 billion tons in 2030 and 1.5 billion tons in 2050, respectively. Ze [9] estimated that China's cement consumption would peak at 2.7 billion tons before 2020. Based on Building and Infrastructure Construction (BIC), Peak consumption Per capita (PCPC), and Fixed Assets Investment (FAI), respectively, Ke et al. [10] predicted that the cumulative cement production in China would be 26.0 Gt, 35.9 Gt and 35.0 Gt from 2011 to 2030. Based on fixed assets investment, urbanization rate and per capita GDP, respectively, Wei et al. [2] projected China's cement production would reach 2,000 Mt, 1,650 Mt and 937 Mt by 2030. Recently Hache et al. [11] studied the impacts of future power generation on cement demand based on climate scenario on a global level, while Elshkaki [12] has estimated cement demand, among oter materials, required for the future electricity generation in China based on several national and international scenarios.
As an energy-intensive industry, energy consumption in the cement industry has attracted much attention. Based on cointegration and error correction model, Mandal and Madheswaran [13] found a long-run and bi-directional causal relationship between output and energy consumption in Indian cement industry. Lin et al. [14] found that the output value of China's cement industry has a positive impact on energy consumption. Oda et al. [15] compared energy efficiency of the cement industry in different countries, and found that in 2005, energy consumption per unit clinker in Japan, India and some EU countries was relatively low, while that in Russia, US and China was relatively high. Using data envelopment analysis, Mandal and Madheswaran [16] concluded that energy efficiency of Indian cement enterprises was related to production volume and labor quality. Recently energy consumption and energy saving potential of the cement industry are predicted in several studies based on scenario analysis. Lin et al. [14] predicted that energy demand in China's cement industry could decrease by 19.06% and 33.69% in 2030, with medium and high energy efficiency respectively. Hasanbeigi et al. [17] analysed energy saving potential of 16 cement plants in Shandong Province, China, and the result showed it could be 12% and 23% if energy efficiency of these plants reaches domestic best level and international best level respectively. Huang et al. [18] estimated that energy efficiency improvement could lead to 25% savings for electricity and 9% savings for fuels in Taiwan's cement industry by 2035. Madlool et al. [19] found that waste heat recovery in cement grinding has great energy saving potential. Several studies have also estimated CO2 emissions from process, fuel combustion and electricity consumption in China's cement industry [20]-[22]. Cement industry is one of the highest CO2 emissions industries in China, however, CO2 emissions in China's cement industry could be overestimated due to ignoring the reality such as technological transition and differences in clinker to cement ratio [23]. Shen et al. [24] surveyed 359 production lines in 22 provinces of China and found that the process emissions and clinker to cement ratio were overestimated by 1.4-3.4% and 12-32%, respectively, and fuel emissions had a deviation of −227.63-6.25%. Liu et al. [25] revised China's coal emission factor, which is about 40% lower than the default emission factor of Intergovernmental Panel on Climate Change (IPCC). Based on the information of 1,574 cement enterprises in China, Cai et al. [26] evaluated the average CO2 emissions in China's cement industry was 806 kg/t clinker, which is 35 kg/t clinker lower than the global level. Ofosu-Adarkwa et al. [27] predicted CO2 emissions of China's cement industry from 2020 to 2030 using a hybrid Verhulst-GM(1,N) model and emissions' technical conversion.
The potential of energy saving and emission reduction in cement industry has attracted worldwide attention. Energy efficiency improvement, waste heat recovery, fossil fuel substitution, raw material substitution, Carbon Capture and Storage (CCS) have been introduced as the main measures to reduce emissions in cement industry [3], [28]-[33]. For example, using a system dynamics approach, Jokar and Mokhtar [28] estimated clinker substitution could reduce CO2 emissions by 15 Mt in Iranian cement industry, and waste heat recovery has less emission reduction potential. Xu et al. [29] predicted that clinker substitution, CCS, efficiency improvement and fuel substitution would reduce CO2 emissions by 37%, 33%, 15% and 15% in China's cement industry by 2050, respectively. Moumin et al. [33] have estimated the reduction in CO2 emissions in the Spanish cement industry could reach 28% using a solar calciner. In a recent study, CO2 emissions from global cement industry has been expected to increase from 3,050 Mt in 2010 to 3,450 Mt in 2020, then gradually decrease to 2,900 Mt in 2050 under a scenario of improving technology and increasing consumption of biomass and natural gas [34]. Energy efficiency and CO2 emissions in the EU cement industry has been analyzed in Pardo et al. [35]. The authors found that thermal energy efficiency and CO2 emission per unit clinker may decrease by 11% and 3.7%, respectively, by 2030 compared to 2002 level. Improvement measures of blended cement, alternative fuel, and waste heat recovery are expected to save 29% and 21% of natural gas and electricity, respectively, and reduce CO2 emissions by 22% in Iran's cement industry in the next 20 years [36]. Benhelal et al. [37] found that fuel substitution in pyro-processing could save 2.3% of energy consumption, and reduce 66% of CO2 emissions in one of the cement plants in the south of Iran. It has been shown that energy efficiency improvement would be the main way to promote energy saving and emission reduction in China's cement industry in the near future [8], [9]. It is argued that CO2 emissions from cement production in China has been decoupling from cement output value, and projected clinker and cement emission factor would gradually decrease with technology improvement by 2030 [2]. It has been found that energy efficiency improvement would be the main driver of CO2 emission reduction in China's cement industry by 2020 [38]. However, technology lock-in effect might limit the diffusion of energy efficiency improvement technology [39].
Although there are several studies addressing cement industry and associated CO2 emissions, China's long-term cement demand and related energy and CO2 emission were not fully studied [2]. In this paper, we analyse the historical demand for cement based on socio-economic, technology, and policy related factors and develop several long term scenarios for cement-energy-CO2 emissions nexus up to 2050. The analysis provides perspectives on future direction to underscore the growing interconnection among energy, cement and carbon emission for promoting integrated planning, management and governance.
The historical consumption of cement from 1980 through 2018 (Figure 1a) [40], [41] has been analysed using linear regression analysis, with GDP, population, urbanization rate, time (as proxy for substitution, technical development, and policy), and the previous cement production as the main determinant factors. Linear regression analysis has been used in many scientific fields to analyse the relationship between a dependent variable and a number of independent and normally it identifies the significant independent variables and examines the separate and combined effects of significant variables. The optimal regression model and the significance of the variables are described by several statistical parameters including the coefficient of determination (R2), the adjusted coefficient of determination (R2adj), and the t- and F-statistics. Historical data on the explanatory variables including GDP, population, the level of urbanization have been obtained from [42].
Historical cement production and consumption, total production of clinker and its production by different technologies (a); clinker to cement ratio overtime (b) and clinker to cement ratio vs clinker production (c)
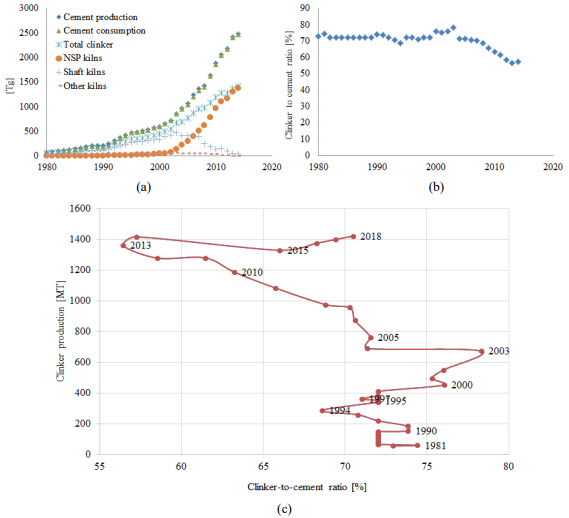
Based on the analysis, it has been found that each one of the explanatory variables is significant when used individually. However, the most significant variable is the previous cement production (R2 is 0.99), followed by the level of urbanization (R2 is 0.94) and then GDP and population (R2 is 0.93 and 0.75, respectively). When these variables have been combined, some of the variables either turned out to be insignificant or have unexpected signs. The best correlations between cement consumption and the combined explanatory variables are those when GDP and population, GDP and urbanization, time and urbanization, and previous cement consumption and urbanization are combined. Although the correlation when GDP and both population and urbanization are combined could be used, we have used the other two correlations [previous cement consumption and urbanization (R2 is 0.99), and time and urbanization (R2 is 0.96)] [eq. (1) and eq. (2)]:
(1)
(2)
where CC is cement consumption, T is time, U is urbanization, and P is previous cement consumption.
The future cement consumption is estimated based on the models obtained by regression analysis and several scenarios for the future development in the explanatory variables. Eq. (1) has been used for SC1 Var and eq. (2) has been used for SC2 Var. The only exogenous variable in the two equations is the urbanization rate. Four scenarios for the average annual urbanization growth rate: 1.44%, 0.6%, 1% and 0.8%, have been used in the analysis representing SC1 U, SC2 U, SC3 U and SC4 U, respectively.
Clinker production has been estimated based on cement production, which is assumed equal to the consumption, and cement to clinker ratio. Although, historically clinker to cement ratio in China has been decreasing overtime, it starts to increase in recent years (Figure 1b and Figure 1c). The scenario used in the analysis assumes an annual increase of the ratio by 0.75%, reaching 75% by 2050. Several technologies are historically used for clinker production including New Suspension Pre-heater and pre-calciner (NSP) kiln, Shaft kiln, and other kilns (including dry and wet rotary kiln), although recently almost 100% of clinker is produced using NSP kilns. In the future only NSP kilns are used for the production of clinker. The rest of the analysis is based on the maximum and minimum annual urbanization growth rates.
As an energy-intensive industry, energy consumption in the cement industry has attracted much attention. Energy demand in China's cement industry is expected to decrease by 19.06% and 33.69% in 2030, with medium and high energy efficiency, respectively [15]. Energy saving potential of 16 cement plants in Shandong Province, China, has been analyzed and the result showed it could be 12% and 23% if energy efficiency of these plants reaches domestic best level and international best level, respectively [17]. It is estimated that energy efficiency improvement could lead to 25% savings for electricity and 9% savings for fuels in Taiwan's cement industry by 2035 [19]. It has been found that waste heat recovery in cement grinding has great energy saving potential [18].
Electricity required for cement production in this analysis is estimated based on cement production and the electricity intensity. Historical electricity intensity of cement production is shown in Figure 2a. Fuel intensity of clinker is estimated based on clinker production and the fuel intensity of the clinker. Historical fuel intensity (total and for each technology) is shown in Figure 2b. Data on historical energy intensity of cement production obtained from [43].
Historical electricity intensity of cement production (a) and historical fuel intensity of the clinker and the different technologies (b)
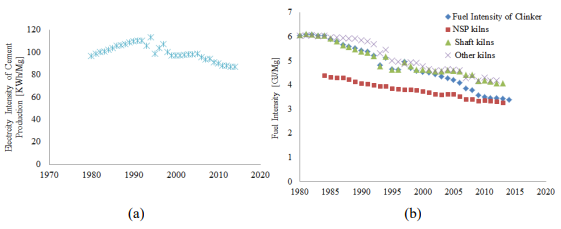
Three scenarios for Electricity Intensity of Cement Production (EICP) and Fuel Intensity of Clinker (FICP) of the NSP kilns in the future have been used. The first scenario assumes no change in the electricity intensity and fuel intensity. The second scenario assumes a reduction of 20% in electricity intensity and 15% of fuel intensity compared to 2015 intensities level. The third scenario is based on the historical trend between 1990 and 2014 as given in eq. (3) and eq. (4):
(3)
(4)
Cement industry is the second largest sector contributing to global anthropogenic CO2 emissions. Several studies have estimated CO2 emissions from process, fuel combustion and electricity consumption in China's cement industry [20]-[22]. However, CO2 emissions in China's cement industry might be overestimated due to ignoring the reality such as technological transition and differences in clinker to cement ratio [24].
Shen et al. [23] surveyed 359 production lines in 22 provinces of China and found that the process emissions and clinker to cement ratio were overestimated by 1.4-3.4% and 12-32%, respectively, and fuel emissions had a deviation of −27.63-6.25%. Liu et al. [25] have revised China's coal emission factor, which is about 40% lower than the default emission factor of IPCC. Based on the information of 1,574 cement enterprises in China, Cai et al. [26] evaluated the average CO2 emissions in China's cement industry was 806 kg/t clinker, which is 35 kg/t clinker lower than the global level. Energy efficiency improvement, waste heat recovery, fossil fuel substitution, raw material substitution, CCS are the main measures to reduce emissions in cement industry [3], [29], [30], [32]. Wu et al. [31] have predicted that clinker substitution, CCS, efficiency improvement and fuel substitution would reduce CO2 emissions by 37%, 33%, 15% and 15% in China's cement industry by 2050, respectively. It is argued that CO2 emissions from cement production in China has been decoupling from cement output value, and projected clinker and cement emission factor would gradually decrease with technology improvement by 2030 [2]. Gao et al. [39] found energy efficiency improvement would be the main driver of CO2 emission reduction in China's cement industry by 2020. However, technology lock-in effect might limit the diffusion of energy efficiency improvement technology [38]. Electricity emissions of cement production are estimated based on cement production and electricity emissions intensity. Historical electricity emissions intensity of cement production is shown in Figure 3a. Fuel emissions intensity of clinker production is estimated based on clinker production and fuel emissions intensity. Historical fuel emissions intensity is shown in Figure 3b.
Historical cement production electricity emissions intensity (a) and historical clinker production fuel emissions intensity (b)
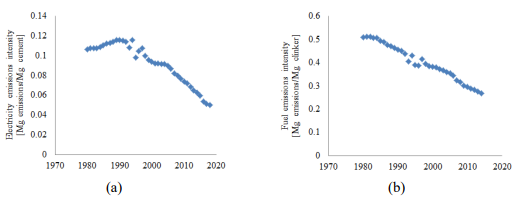
Three scenarios for Electricity Emissions Intensity (EEI), Fuel Emissions Intensity (FEI) of the NSP kilns, and process emissions intensity in the future have been used. The first scenario assumes no change in the electricity emissions intensity, fuel emissions intensity, and process emissions intensity. The second scenario assumes a reduction of 20% in electricity emissions intensity, 15% of fuel emissions intensity, and 12% of process emissions intensity compared to 2015 intensities level. The third scenario is based on the historical trend between 1990 and 2014 as given in eq. (5) and eq. (6). The reduction in emissions in the third scenario is expected to reach 44% by 2050 compared to 2015 level. Historically process emissions intensity was constant at 0.52. Historical information on electricity, fuel, and process emissions have been obtained from [23], [44].
(5)
(6)
Cement production in the eight scenarios, using the four scenarios of urbanization and the two models is shown in Figure 4a. Cement production is expected to reach between 1,919 Tg and 4,568 Tg, which represents between 0.82 and 1.96 times the production level in 2015. Cement production is expected to increase in all scenarios at different rates except one scenario that is based on the lowest urbanization rate (SC2 U) and the model includes the time as explanatory variable (SC2 Var), which shows the significance of the variables captured by the time including policy, substitution and technological development. On cumulative basis, cement production between 1980 and 2015 was 29,018 Tg, and expected to be between 114,641 Tg and 74,153 Tg between 2016 and 2050, an increase by between 155% and 295%.
Historical and future cement production based on the two models and the four urbanization scenarios (a) and historical and future clinker production based on the two models and two urbanization scenarios (b)
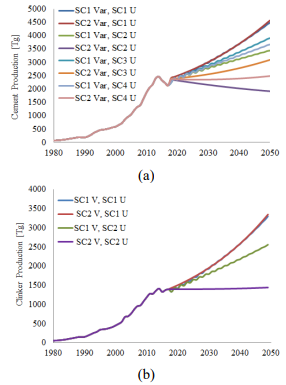
Clinker production using four scenarios of cement production, representing the highest and the lowest urbanization rate and the two models is shown in Figure 4b. Clinker production is expected to increase in all scenarios reaching between 1,448 Tg and 3,447 Tg, which represents between 1.1 and 2.6 times the production level in 2015. On a cumulative basis, clinker production between 1980 and 2015 was 19,369 Tg, and expected to be between 49,413 Tg and 77,800 Tg between 2016 and 2050, an increase by between 155% and 301%.
Electricity and fuel required for cement production and associated emissions in the four scenarios of cement production and the three energy scenarios are shown in Figure 5.
Electricity and fuel required for cement production and associated emissions in the four scenarios of cement production and the three energy and emissions intensities scenarios
In the first energy and emissions scenario, the electricity required is expected to be between 167 TWh and 397 TWh in SC4 (based on the second model and second urbanization scenario) and SC2 (based on the second model and first urbanization scenario). Electricity required is expected to increase by 93%, 96% and 48% in SC1, SC2 and SC3, respectively, and decrease by 18% in SC4 compared to 2015 level as a result of cement production. Fuel required is expected to be between 4,730 PJ and 11,256 PJ in SC4 and SC2. Fuel required is expected to increase by 154%, 159%, 96%, and 9% in four scenarios, respectively, compared to 2015 level as a result of the increase in clinker production. Electricity emissions are expected to increase by 61%, 64% and 24% in SC1, SC2 and SC3, respectively, and decrease by 31% in SC4 compared to 2015 level. Fuel emissions are expected to increase by 92%, 96% and 48% in SC1, SC2 and SC3, respectively, and decrease by 18% in SC4 compared to 2015 level. Process emissions are expected to increase by 154%, 159%, 95% and 9% in SC1, SC2, SC3 and SC4 compared to 2015 level. The total emissions are expected to increase by 125%, 129%, 73% in SC1, SC2 and SC3, respectively, and decrease by 4% in SC4 compared to 2015 level. The results indicate that when the emissions intensities are constant, the total emissions are expected to increase as a result of the increase cement and clinker production in three scenarios and expected to slightly decrease as a result of the decrease in cement production, although clinker production is increasing.
In the second energy and emissions scenario, the electricity required is expected to be between 138 TWh and 328 TWh in SC4 and SC2. Electricity required is expected to increase by 61%, 64% and 23% in SC1, SC2 and SC3, respectively, and decrease by 31% in SC4 compared to 2015 level. Fuel required is expected to be between 4,108 PJ and 9,779 PJ in SC4 and SC2. Fuel required is expected to increase by 125%, 130% and 73% in SC1, SC2 and SC3, respectively, and decrease by 3.5% in SC4 compared to 2015 level. Electricity emissions are expected to increase by 53%, 56% and 18% in SC1, SC2 and SC3, respectively, and decrease by 34% in SC4 compared to 2015 level. Fuel emissions are expected to increase by 92%, 96% and 48% in SC1, SC2 and SC3, respectively, and decrease by 18% in SC4 compared to 2015 level. Process emissions are expected to increase by 123%, 127% and 71% in SC1, SC2 and SC3 and decrease by 5% in SC4 compared to 2015 level. The total emissions are expected to increase by 106%, 110%, 58% in SC1, SC2 and SC3, respectively, and decrease by 12% in SC4 compared to 2015 level. The results indicates that when the emissions intensities are decreasing at the assumed rates, the total emissions are expected to increase as a result of the increased cement and clinker production in three scenarios and expected to decrease as a result of the decreased in cement production, and emissions intensities, although clinker production is increasing. Therefore, the decrease in the emissions intensities at these rates is not enough for the total emissions from the cement industry to decrease as long as the cement and clinker production is increasing.
In the third energy and emissions scenario, the electricity required is expected to be between 97 TWh and 231 TWh in SC4 and SC2. Electricity required is expected to increase by 14% and 16% in SC1 and SC2 and decrease by 13% and 51% in SC3 and SC4 compared to 2015 level. Fuel required is expected to be between 2,641 PJ and 6,287 PJ in SC4 and SC2. Fuel required is expected to increase by 47%, 49% and 12.5% in SC1, SC2 and SC3, respectively, and decrease by 37% in SC4 compared to 2015 level. Electricity emissions are expected to decrease by 75%, 74%, 81% and 89% in SC1, SC2, SC3 and SC4, respectively, compared to 2015 level. Fuel emissions are expected to decrease by 94%, 94%, 96% and 98% in SC1, SC2, SC3 and SC4, respectively. Process emissions are expected to increase by 79%, 82% and 37% in SC1, SC2 and SC3 and decrease by 23% in SC4 compared to 2015 level. The total emissions are expected to increase by 8% and 10% in SC1, SC2 and decrease by 17% and 54% in SC3 and SC4, respectively, compared to 2015 level. The results indicates that when the emissions intensities are decreasing based on historical trend, the total emissions are expected to slightly increase as a result of the increased cement and clinker production in two scenarios, expected to decrease as a result of the decrease in emissions intensities, although cement and clinker production is increasing in one scenario, and expected to significantly decrease as a result of the decrease in emissions intensities and cement production, although clinker production is increasing in one scenario. Therefore, the decrease in the emissions intensities at the historical trend combined with a reduction in cement production (based on lower urbanization rate and the factors captured in the time variable) could reduce the emissions in the cement industry by more than 50%.
Cumulative CO2 emissions in the three energy scenarios are shown in Figure 6. On a cumulative basis, emissions associated with cement production between 1980 and 2015 were 19,000 Tg, and expected to be between 39,440 Tg and 61,940 Tg between 2016 and 2050, an increase by between 110% and 230% in the first emission scenario. Cumulative emissions are expected to be between 36,425 Tg and 56,926 Tg between 2016 and 2050, an increase between 92% and 200% in the second emissions scenarios. These emissions are expected to be between 30,630 Tg and 45,214 Tg between 2016 and 2050, an increase between 61% and 136% in the third emissions scenarios.
Cumulative CO2 emissions in the four scenarios of cement production and the three energy scenarios
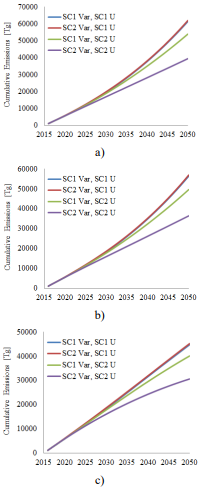
The paper analyses the historical demand for cement in China and provides several long term scenarios for its future demand and associated energy and emissions. Several conclusions can be drawn from the analysis.
Although several individual factors have been found significant in determining the historical demand for cement in China, the most significant variables are the previous cement production and the level of urbanization.
Cement production is expected to increase unless the level of urbanization grows at lower level combined with policy and technical aspects that aim at increasing resource efficiency and substitution.
The emissions associated with cement production are expected to increase as long as the current technologies and policies remain unchanged combined with an increase in the cement production.
The decrease in the emissions intensities at the historical trend combined with a reduction in cement production (based on lower urbanization rate and the factors captured in the time variable) could reduce the emissions in the cement industry by more than 50%.
- , , Technology Roadmap Low-Carbon Transition in the Cement Industry, Technology Report, 2018
Chinas Cement Demand and CO2 Emissions Toward 2030: From the Perspective of Socioeconomic, Technology and Population ,Environmental Science and Pollution Research , Vol. 26 ,pp 6409-6423 , 2019, https://doi.org/https://doi.org/10.1007/s11356-018-04081-2
, Mapping and Modeling Multiple Benefits of Energy Efficiency and Emission Mitigation in Chinas Cement Industry at the Provincial Level ,Applied Energy , Vol. 155 ,pp 35-58 , 2015, https://doi.org/https://doi.org/10.1016/j.apenergy.2015.05.104
, World Cement Production and Environmental Implications ,Environmental Development , Vol. 10 ,pp 36-47 , 2014, https://doi.org/https://doi.org/10.1016/j.envdev.2014.02.005
, Long-Term Behaviour of CO2 Emissions from Cement Production in Spain: Scenario Analysis Using an Energy Optimisation Model ,Journal of Cleaner Production , Vol. 99 ,pp 101-111 , 2015, https://doi.org/https://doi.org/10.1016/j.jclepro.2015.03.027
, Analysis on Major Drivers of Cement Consumption During the Urbanization Process in China ,Journal of Cleaner Production , Vol. 133 ,pp 304-313 , 2016, https://doi.org/https://doi.org/10.1016/j.jclepro.2016.05.130
, Projection of Cement Demand and Analysis of the Impacts of Carbon Tax on Cement Industry in China ,Energy Procedia , Vol. 75 ,pp 1766-1771 , 2015, https://doi.org/https://doi.org/10.1016/j.egypro.2015.07.457
, Quantifying the Impacts of Decarbonisation in Chinas Cement Sector: A Perspective From an Integrated Assessment Approach ,Applied Energy , Vol. 185 (Part 2),pp 1840-1848 , 2017, https://doi.org/https://doi.org/10.1016/j.apenergy.2015.12.112
, Re-Exploration of Cement Consumption Peak in China ,China Cement , Vol. 8 ,pp 17-21 , 2013
, Potential Energy Savings and CO2 Emissions Reduction of Chinas Cement Industry ,Energy Policy , Vol. 45 ,pp 739-751 , 2012, https://doi.org/https://doi.org/10.1016/j.enpol.2012.03.036
, The Impact of Future Power Generation on Cement Demand: An International and Regional Assessment Based on Climate Scenarios ,International Economics , Vol. 163 ,pp 114-133 , 2020, https://doi.org/https://doi.org/10.1016/j.inteco.2020.05.002
, Material-Energy-Water-Carbon Nexus in Chinas Electricity Generation System up to 2050 ,Energy , Vol. 189 ,pp 116355 , 2020, https://doi.org/https://doi.org/10.1016/j.energy.2019.116355
, Causality Between Energy Consumption and Output Growth in the Indian Cement Industry: An Application of the Panel Vector Error Correction Model (VECM) ,Energy Policy , Vol. 38 (11),pp 6560-6565 , 2010, https://doi.org/https://doi.org/10.1016/j.enpol.2010.07.042
, Energy Conservation in Chinas Cement Industry ,Sustainability , Vol. 9 (4),pp 668 , 2017, https://doi.org/https://doi.org/10.3390/su9040668
, International Comparisons of Energy Efficiency in Power, Steel, and Cement Industries ,Energy Policy , Vol. 44 ,pp 118-129 , 2012, https://doi.org/https://doi.org/10.1016/j.enpol.2012.01.024
, Energy Use Efficiency of Indian Cement Companies: A Data Envelopment Analysis ,Energy Efficiency , Vol. 4 ,pp 57-73 , 2011, https://doi.org/https://doi.org/10.1007/s12053-010-9081-7
, Analysis of Energy-Efficiency Opportunities for the Cement Industry in Shandong Province, China: A Case Study of 16 Cement Plants ,Energy , Vol. 35 (8),pp 3461-3473 , 2010, https://doi.org/https://doi.org/10.1016/j.energy.2010.04.046
, A Critical Analysis of Energy Efficiency Improvement Potentials in Taiwans Cement Industry ,Energy Policy , Vol. 96 ,pp 14-26 , 2016, https://doi.org/https://doi.org/10.1016/j.enpol.2016.05.025
, A Critical Review on Energy Use and Savings in the Cement Industries ,Renewable and Sustainable Energy Reviews , Vol. 15 (4),pp 2042-2060 , 2011, https://doi.org/https://doi.org/10.1016/j.rser.2011.01.005
, Estimation of CO2 Emissions from Chinas Cement Production: Methodologies and Uncertainties ,Energy Policy , Vol. 57 ,pp 172-181 , 2013, https://doi.org/https://doi.org/10.1016/j.enpol.2013.01.028
, An Inventory of Primary Air Pollutants and CO2 Emissions from Cement Production in China, 1990-2020 ,Atmospheric Environment , Vol. 45 (1),pp 147-154 , 2011, https://doi.org/https://doi.org/10.1016/j.atmosenv.2010.09.034
, Trajectory and Driving Factors for GHG Emissions in the Chinese Cement Industry ,Journal of Cleaner Production , Vol. 53 ,pp 252-260 , 2013, https://doi.org/https://doi.org/10.1016/j.jclepro.2013.04.001
, Calculation and Evaluation on Carbon Emission Factor of Cement Production in China ,Chinese Science Bulletin , Vol. 61 (26),pp 2926-2938 , 2016
, Factory-Level Measurements on CO2 Emission Factors of Cement Production in China ,Renewable and Sustainable Energy Reviews , Vol. 34 ,pp 337-349 , 2014, https://doi.org/https://doi.org/10.1016/j.rser.2014.03.025
, Reduced Carbon Emission Estimates from Fossil Fuel Combustion and Cement Production in China ,Nature , Vol. 524 ,pp 335-338 , 2015, https://doi.org/https://doi.org/10.1038/nature14677
, Evaluating CO2 Emission Performance in Chinas Cement Industry: An Enterprise Perspective ,Applied Energy , Vol. 166 ,pp 191-200 , 2016, https://doi.org/https://doi.org/10.1016/j.apenergy.2015.11.006
, Forecasting CO2 Emissions of Chinas Cement Industry Using a Hybrid Verhulst-GM(1,N) Model and Emissions Technical Conversion ,Renewable and Sustainable Energy Review , Vol. 130 ,pp 109945 , , https://doi.org/https://doi.org/10.1016/j.rser.2020.109945
, Policy Making in the Cement Industry for CO2 Mitigation on the Pathway of Sustainable Development- A System Dynamics Approach ,Journal of Cleaner Production , Vol. 201 ,pp 142-155 , 2018, https://doi.org/https://doi.org/10.1016/j.jclepro.2018.07.286
, CO2 Emissions Reduction Potential in Chinas Cement Industry Compared to IEAs Cement Technology Roadmap up to 2050 ,Applied Energy , Vol. 130 ,pp 592-602 , 2014, https://doi.org/https://doi.org/10.1016/j.apenergy.2014.03.004
, Low Carbon Measures for Cement Plant -A Review ,Journal of Cleaner Production , Vol. 103 ,pp 260-274 , 2015, https://doi.org/https://doi.org/10.1016/j.jclepro.2014.11.003
, Reducing Environmental Impacts and Carbon Emissions: Study of Effects of Superfine Cement Particles on Blended Cement Containing High Volume Mineral Admixtures ,Journal of Cleaner Production , Vol. 196 ,pp 358-369 , 2018, https://doi.org/https://doi.org/10.1016/j.jclepro.2018.06.079
, Integrated Assessment of CO2 Reduction Technologies in Chinas Cement Industry ,International Journal of Greenhouse Gas Control , Vol. 20 ,pp 27-36 , 2014, https://doi.org/https://doi.org/10.1016/j.ijggc.2013.10.004
, CO2 Emission Reduction in the Cement Industry by Using a Solar Calciner ,Renewable Energy , Vol. 145 ,pp 1578-1596 , 2020, https://doi.org/https://doi.org/10.1016/j.renene.2019.07.045
, - , Long-Term Model-Based Projections of Energy Use and CO2 Emissions from the Global Steel and Cement Industries, Resources, Conservation and Recycling, 2016
Prospective on the Energy Efficiency and CO2 Emissions in the EU Cement Industry ,Energy , Vol. 36 (5),pp 3244-3254 , 2011, https://doi.org/https://doi.org/10.1016/j.energy.2011.03.016
, A System Dynamics Model for Analyzing Energy Consumption and CO2 Emission in Iranian Cement Industry Under Various Production and Export Scenarios ,Energy Policy , Vol. 58 ,pp 75-89 , 2013, https://doi.org/https://doi.org/10.1016/j.enpol.2013.02.042
, A Novel Design for Green and Economical Cement Manufacturing ,Journal of Cleaner Production , Vol. 22 (1),pp 60-66 , 2012, https://doi.org/https://doi.org/10.1016/j.jclepro.2011.09.019
, A Bottom-Up Optimization Model for Long-Term CO2 Emissions Reduction Pathway in the Cement Industry: A Case Study of China ,International Journal of Greenhouse Gas Control , Vol. 44 ,pp 199-216 , 2016, https://doi.org/https://doi.org/10.1016/j.ijggc.2015.11.028
, Evolution and Projection of CO2 Emissions for Chinas Cement Industry from 1980 to 2020 ,Renewable and Sustainable Energy Reviews , Vol. 74 ,pp 522-537 , 2017, https://doi.org/https://doi.org/10.1016/j.rser.2017.02.006
, Estimating the In-Use Cement Stock in China: 1920-2013 ,Resources, Conservation and Recycling , Vol. 122 ,pp 21-31 , 2017, https://doi.org/https://doi.org/10.1016/j.resconrec.2017.01.021
, A Probabilistic Dynamic Material Flow Analysis Model for Chinese Urban Housing Stock ,Journal of Industrial Ecology , Vol. 22 (2),pp 377-391 , 2017, https://doi.org/https://doi.org/10.1111/jiec.12579
, - , , China Statistical Yearbook 2010-2018, 2018
- , , China Cement Almanac, 2011
- , , CO2 Emissions from Cement Production, Intergovernmental Panel on Climate Change (IPCC)