The waste problem is increasingly becoming a severe problem in the 21st century due to the accumulated municipal wastes generated from everyday human activities. An increase in living standards automatically leads to an increase in municipal waste. In Indonesia, Surabaya bears 2,483 tons of waste per day, of which 37.1% of the untreated waste is left. It ends up in rivers, along railway lines, landfills, is burnt directly or disposed of in some other way [1]. Several studies on managing organic waste have begun to be undertaken through several methods, such as methods on handling manure wastes [2] and agriculture crops [3]. In addition, the ways to convert agriculture waste into bio-oil were also revealed [4].
However, the type of waste that causes the most worrying health risk and environmental concerns is plastic waste. It will contribute to global plastic waste, which is projected to escalate into a staggering 1.3 billion tons in 2040 [5] if the growth trend of generated plastic waste is maintained. Plastic wastes are not biodegradable, resulting in higher environmental disturbances, especially when disposed of inappropriately. Generally, the fastest ways to reduce plastic wastes are open-air incineration and waste mining from the landfill [6]. Open-air incineration releases greenhouse gases and toxic matter, which are other environmental problems, especially dioxins [7].
Meanwhile, waste mining is carried out by excavating the plastic waste into the landfill. The aim is to get the combustible material from the disposal site, which can be used as an input for the refuse-derived fuel (RDF) production process and energy recovery from the incinerator. Although these methods reduce the volume of plastic waste, they are not environmentally friendly. Therefore, it is necessary to apply environmentally-friendly technology in plastic waste processing to reduce its continuous accumulation and not increase greenhouse and toxic gas emissions.
Recently, many researchers have taken some alternative actions to reduce the need for fossil fuels by producing alternative fuels through the conversion of plastic waste using the pyrolysis method, that is, by pyrolyzing a mixture of rubber and plastic wastes [8]. In addition, alternative fuels can be obtained in various ways, either in terms of their feedstock origin or production process. However, a common thread among those methods is applying clean and sustainable procedures, such as the thermo-chemical conversion process [9]. Manges et al. reported a comparison of properties of pyrolysis oils derived from HDPE (high-density polyethylene), LDPE (low-density polyethylene), and PP (polypropylene) that have the potential as a diesel engine fuel [10]. Then, in addition to being useful for obtaining alternative fuels from plastic waste, this method is also very promising because it has a number of advantages, including a significant reduction of the volume of waste [11]. The pyrolysis has some disadvantages, including: (1) the stream of product yields are quite complex than other alternative treatments, and (2) the gas yields cannot be exhausted directly without treatment because of the highly flammable gases like CO, CH4, and H2 concentrations, which is quite dangerous for the environment. However, these disadvantages can be overcome by innovating pyrolysis processing features and utilizing flammable gas for other purposes. Examples of these are energy feedstocks for fuel cells or gasification co-generation. Previous research has evaluated their economic aspects [12] by which the produced yields of pyrolysis have the potential to produce solid, liquid, and gaseous fuels simultaneously. It will generate a significant energy content with the smallest environmental effect, compared to other plastic-waste-processing methods.
This investigation will use the low-density polyethylene (LDPE) plastic to be converted into oil yields. LDPE is used widely in many industrial areas, such as packaging, automotive, electrical-electronics, food, and agriculture [13]. An important reason why LDPE is considered a feedstock is that it is made from petroleum and is a type of plastic that is difficult to destroy but can be recycled. Because this plastic waste promises enormous potential as an alternative fuel, the present study aims to investigate whether the oil yields produced by pyrolysis can replace fossil fuels and their similar properties. This is to understand the physicochemical properties of the yields. Since pyrolysis is a thermochemical degradation process [14], the thermal effect of decomposing LDPE plastic waste is an essential parameter in the chemical recycling process. Then, this study will analyse the change in physicochemical properties of yields affected by pyrolysis temperature, which impacts the properties of oil yields.
To date, the previous LDPE research only discussed the changes in its chemical properties or its physical properties [15], [16]. There is a lack of information/data about the changes in the chemical properties affecting the changes in their physical properties [17]. The causes of the changes in the properties are crucial to be understood [18] because the material has two properties that should be related to each other [19], [20]. This work also explains the reaction mechanism of the LDPE molecular structures during the changes in the chemical properties that affect the physical properties.
Moreover, this study aims to confirm that the oil yields of pyrolysis products can be used directly according to the physical properties of the appropriate substitute fuels. As a result, it can be directly applicable to engines. By examining the effects of pyrolysis temperature variations, the appropriate temperature for processing plastic wastes into oil fuel will be identified. The quantitative aspects, such as the mass and the volume of oil yields, are also investigated. This study also offers a convenient and informative approach to investigate the mechanisms of molecular degradation by comparing each of the different pyrolysis temperatures, thus making it possible to influence physical properties.
In this study, the pyrolysis process was conducted in a real pilot plant in a laboratory-scale plastic pyrolizer, as shown in Figure 1a. Meanwhile, Figure 1b illustrates the process flow diagram during the experiments.
The experimental device for LDPE plastic pyrolizer (a); process flow diagram (b)
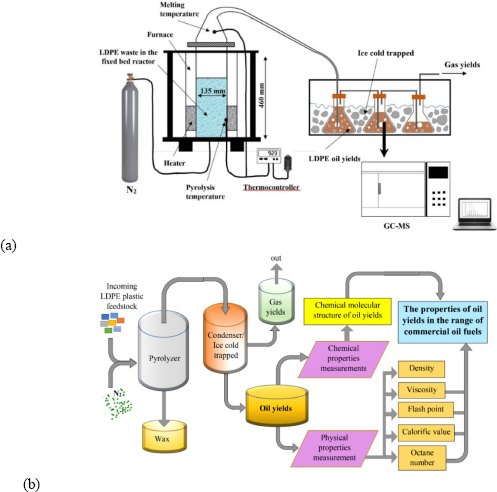
The plastic materials used as the pyrolysis feedstock were LDPE samples from an Indonesian petrochemical industry that do not have any pigmentation (i.e., transparent in colour). The feedstock has the physicochemical properties listed in Table 1 and Table 2. From the tables, it was found that the molecular formula is C38H38O6, while the predicted molecular structure of LDPE was shown in Figure 2.
LDPE molecular structure
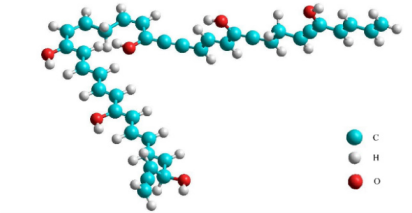
Firstly, for the preparation of the representative LDPE plastic samples, fine cuttings of food wrapper roughly the size of 0.25 cm2 with an initial mass of 250 g were cut using scissors for this experiment. After the pyrolizer (of fixed-bed type) and feedstock of LDPE were ready, the feedstock was put into the pyrolizer reactor, and then the reactor was closed tightly so that no leakage occurred. The pyrolysis process was conducted with temperature setting variations of 200 °C, 250 °C, 300 °C, 350 °C, and 400 °C for two hours with a heating rate of 10 °C/min. The temperature was observed with the help of a thermocouple and controlled by a thermo-controller where the changes in pyrolysis temperature were recorded in a computer through a data logger. Afterwards, N2 was flowed into the furnace/reactor to suppress O2 in the reactor to prevent combustion. After the pyrolysis process has been completed, besides obtaining temperature distribution measurements along the process, experimental data measured in the form of mass, volume, and density of the solid yields (wax) and the oil from pyrolysis were also obtained. Te wax was left in the furnace, and the oil yields were trapped in the beaker glasses inside an ice-cold bath. Moreover, another thermocouple was attached inside the furnace to observe the melting temperature of the condensed gas before turning it into oil yields, thus observing the relationships among the heat energy inside the furnace, the time to condense oil, and the melting point of condensed gas yields.
Physical properties of LDPE [21]
Property |
Unit |
Value |
---|---|---|
Molecular mass |
kg/mol |
≤600 |
Density |
g/ml |
0.91–0.93 |
Melting point |
°C |
100–110 |
Glass transition temperature |
°C |
–110 |
HDT at 0.46 MPa |
°C |
40–50 |
HDT at 1.8 MPa |
°C |
30–40 |
Tensile strength |
MPa |
8–15 |
Elongation |
% |
90–800 |
Flexural modulus |
GPa |
0.25 |
Impact strength |
J/m |
No break |
Surface hardness |
SD48 |
|
% Crystallinity |
% |
40–50 |
Afterwards, the oil yields were investigated for their physical properties, such as density, viscosity, flashpoint, calorific value, and octane number (RON), by using devices for measuring the physical properties as the measurement standardization. The density was calculated from the ratio of oil mass to its volume using the ACIS BC 500 electrical balance and a volume scale's beaker glass at STP condition. Then, the oil viscosity was measured at a standard temperature of 40 °C by means of viscometer type SYD-216D, and the flashpoint was measured using LEYBOLD, type: ABR NL 90212. For measuring oil calorific value, a bomb calorimeter method was used through the Parr 6050 Calorimeter. Subsequently, RON was tested using the CFR F1 engine BLS SX-100K at a standard temperature measurement of 23.4 °C. Apart from being tested in terms of their physical properties, the oil yields' chemical properties were also investigated using Gas Chromatography-Mass Spectrometry (GC-MS). This enabled identification of the chemical compositions of LDPE liquid yields after pyrolysis and categorization of the physicochemical properties of pyrolysis oil that are comparable to the substituted oil. As a result, the relationship between the two groups of properties will be better understood to find out whether or not the oil can substitute commercial oil fuels used now.
Elemental analysis of LDPE [22]
C |
H |
O |
|
---|---|---|---|
LDPE elemental composition (wt. %) |
77.13 |
6.07 |
16.8 |
It was found that pyrolysis produced three kinds of yields: solid (wax), liquid (oil), and gas (syngas) yields. However, this study will only analyse the oil yields just for the sake of changing the fuels. The results show that the product capacity of the oil yields was influenced by the different pyrolysis temperatures. In addition to affecting the resulting product, it turns out that this temperature also affects the properties of the oil yields. This study carried out two kinds of properties measurements; chemical and physical properties tests, which will be analysed in the following section. From the results, it was found that changes in chemical properties will affect physical properties.
A comparison of the snapshot of oil products between LDPE oil yields (a) and gasoline (b)
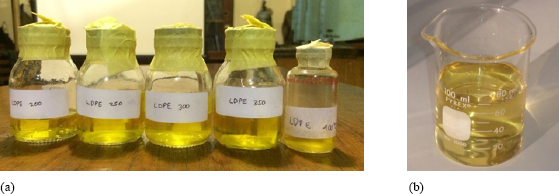
Figure 3 depicts a photograph of LDPE oil yields for each pyrolysis temperature. From the picture, it can be seen that the oil yields have a light-yellow colour similar to that of gasoline or those of commercial fuel oil on the market. Further analyses are needed by comparing the physical properties of the oil yields with the physical properties of other commercial fuels to find out whether the oil yields are suitable for use as an alternative oil fuel to substitute other commercial oil fuels,
Because this study investigates the effect of pyrolysis temperature, the temperature distribution during pyrolysis was observed.
Pyrolysis temperature, melting temperature, and condensation time & temperature in elapsed time
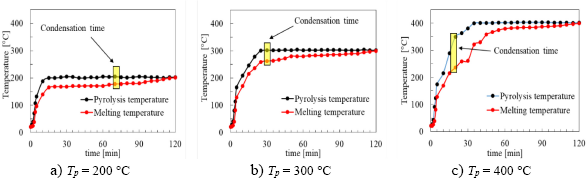
Figure 4 shows the pyrolysis temperature distribution of the LDPE plastic at various pyrolysis temperatures (Tp). The yellow square sign represents the condensation temperature and the time in which the pyrolytic gas of LDPE yield was condensed to oil yields into the beaker glass. From the figure, it can be seen that the condensation time of oil yields into the beaker glass shows the relationship among the pyrolysis temperature, the heating time, and the time to achieve condensation of oil yields. At the pyrolysis temperature of 200 °C, oil starts dripping into the glass beaker at 70 minutes. Meanwhile, at 300 °C, oil starts dripping at 30 minutes. At the highest pyrolysis temperature of 400 °C and after 20 minutes of processing, the oil starts to drip. At pyrolysis temperature (Tp) 300 °C, the condensation started at t = 30 min and T = 262 °C. Meanwhile, at Tp = 400 °C, it began at t = 25 min and T = 259 °C. There is a 3-degree smaller difference in Tp = 400 °C than in Tp = 300 °C, but it was faster by 5 minutes in Tp = 400 °C than in Tp = 300 °C. This occurred because, at Tp = 400 °C, the thermal energy given in the furnace is higher, so the heating force among LDPE molecules is greater. It accelerates the achievement of condensation at the beginning of the reaction with a faster time. The high pyrolysis temperature forces LDPE molecules to absorb more heat, and the condensation time required by LDPE is achieved faster. Conversely, at lower pyrolysis temperature Tp = 300 °C, the force of attraction among the LDPE molecules affecting the intermolecular force is stronger at low temperatures. So, the stronger intermolecular interactions result in higher melting points, as shown in the relatively higher and slower condensation start.
When LDPE plastic is heated, the LDPE temperature increases, affected by the endothermic reaction. Afterwards, the LDPE began to decompose, and its phase changes from solid to liquid. With increasing pyrolysis temperature, the phase will change from liquid to gas. Then, this yield will exit into the ice-cold trap to be condensed. At higher pyrolysis temperatures, the formation of gaseous products due to biomass decomposition occurs faster, so the change from gas to liquid also occurs more quickly. As a result, the oil yields entering the ice-cold trap also happens faster (dripping faster). However, in this condition, the mass and volume of oil yield are smaller because the oil yields cannot condense completely due to the lack of residence time of condensation in this ice-cold trap. As a result, both non-condensable and condensable gas come out together, implying the mass and volume of the gas yields will be greater than the oil yields. It can be correlated to Figure 5 and Figure 6, in which the mass and volume of the oil yields at Tp = 400 °C are smaller than at Tp = 300 °C, even though Tp = 400 °C has a faster condensation start.
From Figure 2, it can be inferred that the higher the temperature is, the condensation will start sooner. This condition also indicates that the higher the pyrolysis temperature, the shorter residence time is required to start for condensation of gases to become liquid yield. In fact, it takes the same amount of thermal energy to convert LDPE pyrolysis products to a liquid form at all different pyrolysis temperatures. However, the heating temperature is inversely proportional to the condensation time of oil yields, and a higher heating temperature yields a faster product than a lower heating temperature. Therefore, for the process of converting LDPE into oil, a high temperature is not needed [23] because it will cause wasteful heating energy in the reactor.
The mass of oil yield
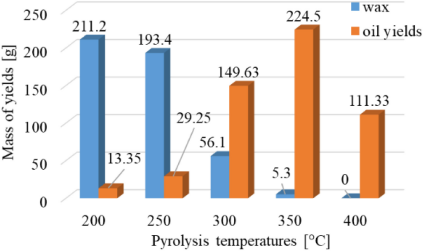
The volume of oil yield
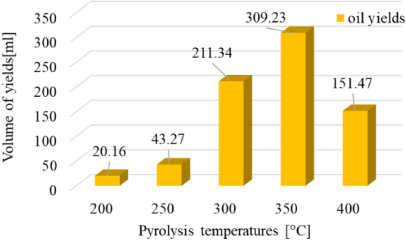
After identifying the temperature profiles during the pyrolysis process, the effect of temperature on the oil products was also observed.
Based on Figure 5, it can be observed that an increase in pyrolysis temperature will have an impact on the increase in the amount of mass oil yield produced around 120 minutes during the process. The graph shows the production of solid yields (wax) and liquid yields (oil). If it is related to wax production, the increase in oil yields is due to the decrease in wax products. It can be determined by the mass and energy balance equation:
(1)
(2)
where mfeedstock as mLDPE explains the mass of LDPE plastic in the initial process. Meanwhile, myields (mass of yields produced after pyrolysis) consist of mwax (mass of wax), moil yields (mass of oil yields), and mgas yields (mass of gas yields). In the study, mLDPE, mwax, and moil yields were measured; however, mgas yields was predicted as determined in Table 3. The values of all mfeedstock and myields are stated in gram.
The feedstock and yields produced by pyrolysis in the mass-energy balance
Tp [°C] |
Initial mass [g] |
Product yields [g] |
||
---|---|---|---|---|
Wax |
Oil |
Gas |
||
250 |
211.2 |
13.35 |
25.45 |
|
250 |
250 |
193.4 |
29.25 |
27.35 |
300 |
250 |
56.1 |
149.63 |
44.27 |
350 |
250 |
5.3 |
224.5 |
20.2 |
400 |
250 |
0 |
111.33 |
138.67 |
At a temperature of 200 °C, the amount of wax produced is greater than at other temperatures, automatically resulting in a smaller oil yield production. As the temperature increases, the production of wax decreases, and most of the LDPE breaks down into gas, which is condensed into oil yields affecting the increase in the oil produced. However, after 350 °C – to be precise, at 400 °C – the amount of oil yield decreased, even though the amount of wax was almost non-existent.
Wax is a solid-yield product, which then melts into a liquid and evaporates into a gas yield. However, because the pressure of the gas that comes out is not large enough due to the small heating temperature, the gas will return to the solid phase again. When it enters the liquid phase, the wax cannot evaporate because the temperature in the reactor has not yet reached the decomposition temperature of these heavier molecules. In addition, the higher the heating temperature in the pyrolysis process, the more gas is produced, either condensed or not. This is because the higher the heating temperature, the plastic will undergo thermal cracking, decomposing the plastic into gas [24]. The condensable gas will change phase into a liquid phase and accommodate in the beaker glass. The more gas yields that can be condensed, the more oil yields will be produced. In other words, the mass of oil yields resulting from pyrolysis will also increase.
However, the decrease in oil yields at 400 °C is caused by the high pyrolysis temperature because – besides producing wax and oil yields – the pyrolysis of LDPE also produces gas yields. In addition, at 400 °C, a secondary reaction occurs where the oil yield in the furnace is converted into more non-condensable gas than in pyrolysis at 350 °C. At 400 °C, more gases are resulting from LDPE decomposition, including flammable gas compounds such as CH4 and H2, therefore decreasing the oil yield production [25].
The same problem also occurs in the volume of oil yields, as shown in Figure 6. It describes the amount of volume of oil yield obtained around 120 minutes pyrolysis process. The increase in oil yield volume also takes place as the temperature increases to 350 °C and then decreases at the pyrolysis temperature of 400 °C. This happens because, at a temperature of 400 °C, more non-condensable gas is produced than at 350 °C.
After analysing the temperature distribution and the quantity of oil yields, this study observed the chemical compounds of oil yields produced at 200 °C, 300 °C, and 400 °C to distinguish the chemical properties of each pyrolysis temperature. Table 4 represents the constituent chemical compounds of oil yields at pyrolysis processes at 200 °C, 300 °C, and 400 °C according to the sequence of carbon chain lengths formed. Aside from being shown by the chemical structure, it is also indicated by their isomer and percentage. From the GC-MS results, the longest chain at 200 °C is C20, at 300 °C is C24, and at 400 °C, the longest chain is C28. The changes in chemical compounds are directly proportional to the increase in pyrolysis temperature. These changes are caused by the reforming of the initial molecule structure into its isomers and an increased number of cyclic and alkyl molecular groups in the constituent chemical compounds. In addition, the number of polycyclic aromatic hydrocarbons (PAH) has also increased.
Chemical composition of tar yields at 200-400 °C by GC-MS
Chemical structures |
Chemical compound and the isomers |
Normalized peak area [%] |
||
---|---|---|---|---|
Tp = 200 °C |
Tp = 300 °C |
Tp = 400 °C |
||
C6H18 |
Cyclotrisiloxane, hexamethyl Cyclohexene, 3-methyl |
1.19 |
0 |
0 |
C7H12 |
2-Hexene, 2-methyl, 1,3-pentadiene, 2,3-dimethyl |
17.55 |
0.24 |
0.31 |
C8H16 |
Heptane, 4-methyl Cyclohexane, ethyl |
29.11 |
18.25 |
21.84 |
C9H18 |
Cyclohexane, 1,3,5-trimethyl, Dimethyl-3,5 heptene-3 |
13.15 |
8.45 |
11.16 |
C10H22 |
Decane Octane, 3,3-dimethyl |
5.73 |
26.7 |
10.3 |
C12H24 |
Heptane, 2,5,5-trimethyl, 1-methyl-3-propyl-cyclooctane, 2-decene, 2,4-dimethyl |
12.33 |
14.92 |
15.09 |
C11, C13-20 |
20.94 |
31.44 |
41.3 |
Related to the change in the carbon chain length, at 200 °C, the percentage of long-chain hydrocarbon content starting from C11 is 32.73%. The change occurred at 300 °C, with an increase in the carbon chain to 46.36%, and it continued to increase to 53.39% at 400 °C. This increase occurred because the solid yield (wax) produced at low pyrolysis temperatures decomposes, forming oil yields with a large molecular weight. In addition, at high pyrolysis temperatures, the production of gases that have a small molecular weight will increase, meaning that the oil yields only consist of those with large molecular weight, implying a longer carbon chain.
After observing the hydrocarbon compounds of oil yield constituents in Table 4, in general, the results show that increasing pyrolysis temperature will also increase the cyclic compounds and compounds containing alkyl groups. In addition, the higher the pyrolysis temperature, the longer the carbon chain of the oil yield compound that will be formed. This is the result of the thermal effect of pyrolysis temperature. The effect of heat will affect the abstraction of H atoms due to changes in entropy in LDPE oil. There is a possibility of internal rotation of methyl groups that occurs. The methyl groups have the same hindering potential as in the early LDPE hydrocarbon. The methyl bonds will break away from each other and will form bonds with other hydrocarbon molecular radicals. There is a possibility of internal rotation of methyl groups that occurs. The methyl groups have the same hindering potential as in the early LDPE hydrocarbon. The methyl bonds will break away from each other and will form bonds with other hydrocarbon molecular radicals. In addition, an increase in temperature will cause the abstraction of H atoms. The lack of H atoms in the parent compound will, in turn, force the C-C atoms to bond together to form cyclic bonds. It can be seen that the percentage of alkyl and cyclic compounds increase at high pyrolysis temperatures. In general, at all variations of pyrolysis temperature, most of the hydrocarbons of oil LDPE produced are C7H12, C8H16, C9H18, C10H22, and C12H24, along with their isomers.
These reaction mechanisms for the formation and release of hydrocarbon molecular structures have been simulated using the Spaya.ai software, showing the stages of the H release mechanism [26], the combination of hydrocarbon molecules with alkyl compounds, formation of cyclic compounds, and isomerase compounds. All of which can be seen in Figure 7.
The changes that occur in oil yields compounds based on the GC-MS at 200–400 °C will impact the other properties, i.e., the physical properties as described in the following section.
The reaction mechanism of the change in LDPE molecular structure
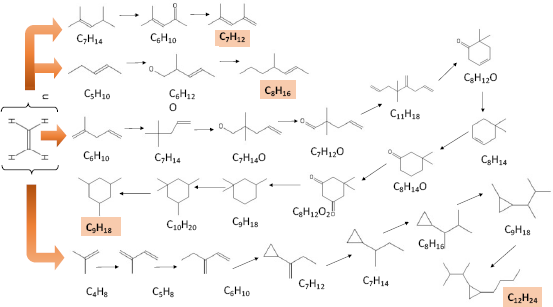
Density is one of the physical properties of fuel that greatly affects combustion performance. In this study, the effect of pyrolysis temperature on oil yield density will be verified. Figure 8 describes the change in the density of oil yields at various pyrolysis temperatures obtained from the mass and volume ratio, which has been illustrated in Figure 5 and Figure 6. From Figure 8, it can be seen that the increase in pyrolysis temperature will result in an increase in oil yield density. In low-temperature pyrolysis, thermal cracking occurs in the pyrolysis process because the generated vapor produced by the process in the reactor is condensed before going to the channel that leads to the ice-cold trap so that the oil yield will return to the reactor and be heated again.
As is known, density is the degree of compactness of a substance at a certain volume. The density of a substance depends on the atomic mass of the constituent compound of the substance. This means, the greater the atomic mass of the constituent compounds while the volume stays constant, the greater the density will be. In addition, in thermal cracking, further breakdown of the hydrocarbon chains occurs, which leads to the condensed gas having shorter hydrocarbon chain bonds [27]. Furthermore, the density change is closely related to the composition of the oil yields' constituent compounds, which can be seen in Table 4. From the GC-MS results, it can be seen that longer hydrocarbon bonds result in increased density because they have a heavier molecular weight. With the increasing number of long carbon chains (C11–C28) and the increasing number of double bonds (alkene) and alkyl groups, the density increases as the temperature increases. To apply oil yields to be appropriate as a substitute for oil fuels, the density of LDPE oil yields should have values that are almost the same as the density of commercial fuel oil.
The density of LDPE oil yields at various pyrolysis temperatures compared to other commercial fuels
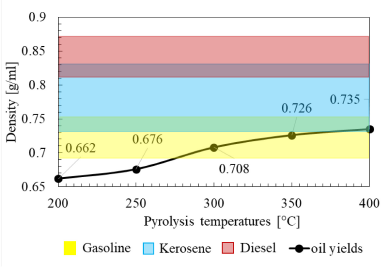
Figure 8 also shows a comparison of the density values of pyrolysis oil with commercial oils. It can be seen that the density of pyrolyzed oil at temperatures of 300 °C and 350 °C is in the density range of gasoline, while at 400 °C, it is almost in the density range of gasoline and kerosene.
The value of the physical properties of viscosity cannot be separated from the density. The viscosity increases as the density increases.
The viscosity of LDPE oil yields at various pyrolysis temperatures compared to other commercial fuels
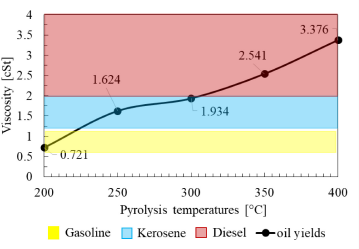
In Figure 9, it can be seen that as the pyrolysis temperature increases, the viscosity of the oil yields also increases because viscosity is influenced by the chemical structure of the constituent molecules. The longer the chemical structure bonds are, the greater the viscosity values will be. As the temperature becomes higher, the oil yields will have a longer carbon chain structure, thus increasing the viscosity value of oil yield.
If the increase in viscosity is correlated with the results of the GC-MS test, the rise in temperature will increase the number of double-bond hydrocarbons in the oil yields, resulting in the increase in viscosity values. Viscosity will increase if the oil yield molecules contain more double-bond molecular chains. Viscosity is the value of a fluid's resistance to flow. Therefore, the greater the viscosity value, the slower the fluid flow. The main factor affecting this matter is the intermolecular force. The force among molecules in double-bond compounds is greater than that of a single bond compound. For example, C10H20O contains double bonds, and with a large inter-molecular force, it has a large viscosity.
The oil yields from the LDPE pyrolysis have viscosity values within the range of commercial fuel viscosity values at each temperature. However, the viscosity of pyrolysis oil at 200 °C has the lowest value and is lower than the viscosity of gasoline, which is 0.721 cSt. The viscosity values of pyrolysis oil at 250 °C and 300 °C fall within the viscosity range of kerosene, and those of oil yields at 350 °C and 400 °C fall within the viscosity range of diesel oil.
Another physical property that is no less important for substitute oil fuel is the flashpoint, which concerns the lowest temperature in which the fuel can be ignited. In Figure 10, it can be seen that at a higher temperature, the oil yield has a higher flashpoint value. If this is associated with the chemical compositions of oil yields, the oil yield at low temperatures has a simpler carbon chain and vice versa. In other words, if the pyrolysis temperature is increased, the flashpoint value of oil yields will also increase.
The flashpoint corresponds to the carbon chain contained in the oil yields. Oil yields having a longer carbon chain will have a higher flashpoint value because it is harder for oil to evaporate when the long carbon chains impact the oil yields to have a larger density and higher viscosity. Oil yields that have a large density and are more viscous are more difficult to burn due to the strong molecule bonds among the constituent atoms. Automatically, it will cause a high flashpoint value.
The flashpoint of LDPE liquid yields at various pyrolysis temperatures compared to other commercial fuels
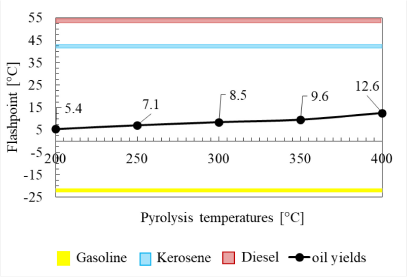
Unfortunately, there is no flashpoint value of oils from the pyrolysis that is precisely the same as the flashpoint value of commercial fuels. However, Figure 10 shows that the flashpoint value of pyrolysis oil is much lower than kerosene and diesel but higher than gasoline.
Similar to the other properties, the calorific value of oil yields also increases as the pyrolysis temperature increases, as shown in Figure 11. The chemical compositions of oil yield compounds will change due to the thermal cracking, which affects the carbon chain structures – from short carbon chains to longer carbon chains as the pyrolysis temperature increases. This is because the calorific value indicates the amount of energy contained in the oil yields, and the calorific value is strongly influenced by the kind of constituent compounds that have the potential for high calorific values.
The calorific value of LDPE liquid yields at various pyrolysis temperatures
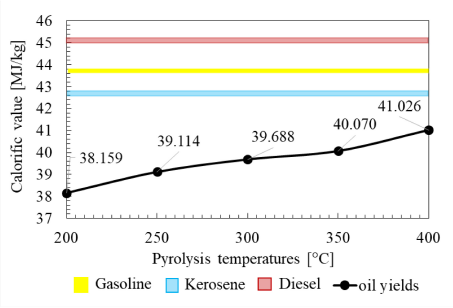
The GC-MS results showed a change in the molecular structure of the oil yields, which led to an increase in calorific values [28]. In addition, the results also determined an increase of polycyclic aromatic hydrocarbons (PAH) compounds. The increase in the formation of PAH compounds will cause an increase in oil yields' calorific value [29]. Besides, the increase in calorific value influenced by the hydrocarbons' chemical structure also shows that there are many flammable compounds. The number of flammable compounds depends on changes in molecular structure due to the formation of alkyl groups in the compounds on the paraffin group, or compounds with the same carbon number, where paraffin has the highest calorific value compared to aromatics and naphthene based on a weight basis.
Commercial oil fuels generally have calorific values ranging from 42.5379 MJ/kg to 46.0548 MJ/kg. In Figure 11, the lowest calorific value of 38.1586 MJ/kg is obtained at 200 °C, and the highest calorific value of 41.0262 MJ/kg is obtained at 400 °C. If a comparison is made with standard fuels, only one calorific value of LDPE oil yields is close to the calorific value of commercial fuel. Oil yields at 400 °C show a calorific value of 41.0262 MJ/kg, close to the kerosene calorific value of 42.8 MJ/kg. Based on this experiment, the oil yields do not fully have the same physical properties as commercial fuels. Therefore, the oil yield should be mixed with other additional additives or introduced to further refinery processes to achieve a physical property value the same as the corresponding property value of commercial fuels.
Another important physical property for oil yields in engine performance applications is the octane number used to assess the fuel's ability to withstand knocking inside the combustion engine. Moreover, this is a reference for measuring gasoline quality, and this shows how much pressure can be exerted before the gasoline ignites spontaneously.
The octane number of LDPE oil yields at various pyrolysis temperatures compared to other commercial fuels
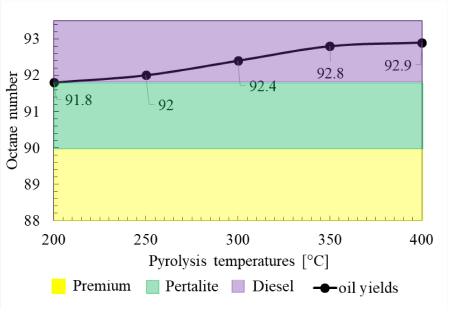
In Figure 12, it can be seen that the octane number increases as the pyrolysis temperature increases. This determines that the increase in temperature will result in a higher-octane number. In the GC-MS results shown in Table 4, the oil yields that are dominated by cyclic compounds and alkyl groups will cause an increase in the octane number. The change in the increase in octane number is more dominated by the number of alkyl groups, which increased from 34.4% to 50.32%, and finally to 78.6% at 200 °C, 300 °C, and 400 °C, respectively. Meanwhile, the change in cyclic compounds increased from 30.85% to 41.02%, and finally to 17.32%. This decrease in cyclic structure is also due to the formation of alkyl and cyclic bonds altogether. The increase in octane number is caused by the cyclic compounds having molecular bonds that are more stable than straight bonds [30]. Meanwhile, the increase in octane number due to the alkyl group is caused by more H atoms joining the oil yield compounds, so the molecules are more stable and do not burn easily.
This elucidates the change in the composition of oil LDPE pyrolysis molecules based on GC-MS results. After the observation, the changes in the percentage of straight-chain compounds, cyclic compounds, and alkyl compounds at different pyrolysis temperatures are formulated in Table 5.
The chemical groups of GC-MS results
Tp = 200 °C |
Tp = 300 °C |
Tp = 400 °C |
|
---|---|---|---|
Straight-chain aliphatic hydrocarbons |
34.75% |
8.66% |
4.08% |
Branched-chain with alkyl compounds |
34.4% |
50.32% |
78.8% |
Cyclic hydrocarbon compounds |
30.85% |
41.02% |
17.32% |
Table 5 illustrates that as the temperature increases, the percentage of the straight chain compounds will decrease. This is because temperature affects thermal cracking on these compounds. The straight compounds will decompose into other hydrocarbon group compounds, such as cyclic compounds and alkyl compounds groups. In the oil-yield compounds containing alkyl molecules, an increase in temperature will increase alkyl group formation because many alkyl compounds are formed due to the release of H atoms during the decomposition of LDPE in the pyrolysis process. The higher the temperature, the greater the thermal cracking for decomposing the LDPE compounds. As a result, the splitting of compounds also releases a lot of H atoms. Therefore, many alkyl compounds that have radical properties are formed. These alkyl compounds will induce other compounds, like straight-chain and other cyclic compounds, to fuse into a new molecular structure of hydrocarbon.
Cyclic compounds display a particularly unique trend. Initially, there was an increase in cyclic compounds from Tp = 200 °C to Tp = 300 °C. Above Tp = 400 °C, the percentage decreased significantly, from 41% to 17.32%, due to the following:
Figures 5 and 6 indicate a very significant gas formation. The change in cyclic compounds is closely related to the formation of gas compounds that have shorter carbon chains, such as CH4 and H2, which are decomposed from cyclic compounds;
On the other hand, the changes in compounds due to gas formation will also reduce the percentage of straight-chain aliphatic compounds. This is because the straight aliphatic compounds easily become gases;
The number of cyclic groups decreases with the increase in alkyl compounds because the cyclic compounds without double bonds are easily isomerized due to their dynamic electrons. A shortage of electrons is caused by a dynamic electron in this particular cyclic bond, so it is easily broken, and its structure changes. The bond dissociation energy of cyclic compounds is not as high as that of alkyl or aromatic compounds. Thus, it is easier to decompose than alkyl compounds.
Besides, the increase in branched chains in the oil yield compounds at a higher pyrolysis temperature also affects the increase in the octane number because the branched-chain paraffin has a much higher rating of octane number than straight-chain paraffin. In addition, the increase in octane number is caused by the rise in the percentage of long-chain hydrocarbon content with increasing temperature. This affects the decrease in shorter and more medium-chain hydrocarbon content from 200 °C to 400 °C because the increase in temperature influences the increase in oil yield production, resulting in more compounds consisting of large molecules. Compounds having large molecular weight tend to have long carbon chains. The high molecular weight increases LDPE molecules' resistance to decomposition, and as the carbon chain gets longer, the total binding forces among molecules are greater, making the LDPE chain stronger. Therefore, the increase in molecular weight and longer carbon chains make it difficult for fuels to burn at low temperatures. Hence, the oil yield will be able to withstand high pressures and temperatures. When applied to the engine, this can delay the occurrence of knocking.
The octane number measurements were carried out on oil yields at pyrolysis temperatures of 200 °C, 250 °C, 300 °C, 350 °C, and 400 °C with results showing the values of 91.8, 92, 92.4, 92.8, and 92.9, respectively. These results indicate that LDPE pyrolysis oil fuels have a higher octane number compared to the fuels in the Indonesian market, which are in accordance with government regulations, i.e., Premium (around 88–90), Pertalite (around 90–92), and Pertamax (around 92–95), which are considered safe for use in any engines. The test results show that the oil yields are within the range of Pertalite (90) and Pertamax (92), which are the most recommended fuels for usage.
This study carries out exploration on LDPE pyrolysis. The results of this study indicate that the conversion process of LDPE plastic waste into oil fuel is very promising. The results showed that the pyrolysis process converted almost 90% of LDPE plastic into oil fuel at a temperature of 350 °C. This pyrolysis process of converting this plastic waste also does not require a large heating temperature, thus saving energy. In addition, the chemical properties of GC-MS results showed that the pyrolysis process had changed the chemical compounds that make up the oil yields. This process can improve the physical properties of oil yields. The increase in pyrolysis temperatures will increase oil yield densities, viscosities, flashpoints, calorific values, and octane numbers affected by the change in atomic mass, chemical structure, carbon-chain, amount of PAH formed, and alkyl groups of constituent compounds. The oil yields produced are also comparable to other commercial oil fuels as a substitute oil. The LDPE oil yields confirm that their physical properties are within the range of commercial fuels, while the physical properties of calorific value are below the value of commercial fuels. Even so, any treatments to increase the calorific value can be provided by adding certain additives or further treatment through the oil refinery process. This study recommends that 350 °C is the appropriate pyrolysis temperature because it has the highest production capacity of oil yields, while their properties are within the range of the standard oil fuels properties.
- Indonesia Hasilkan 67 Juta Ton Sampah pada 2019, 2019, https://www.aa.com.tr/id/headline-hari/indonesia-hasilkan-67-juta-ton-sampah-pada-2019/1373712
Poultry Manure Derived Biochars - The Impact of Pyrolysis Temperature on Selected Properties and Potentials for Further Modifications ,J. Sustain. Dev. Energy, Water Environ. Syst. , Vol. 9 (1), 2021, https://doi.org/http://dx.doi.org/10.13044/j.sdewes.d8.0337
, Multicomponent Modelling Kinetics and Simultaneous Thermal Analysis of Apricot Kernel Shell Pyrolysis ,J. Sustain. Dev. Energy, Water Environ. Syst. , Vol. 8 (4),pp 766–787 , 2020, https://doi.org/http://dx.doi.org/10.13044/j.sdewes.d7.0307
, Stabilization of Empty Fruit Bunch derived Bio-oil using Solvents ,J. Sustain. Dev. Energy, Water Environ. Syst. , Vol. 4 (1),pp 38–47 , 2016, https://doi.org/http://dx.doi.org/10.13044/j.sdewes.2016.04.0004
, Development of a green procedure of citrus fruits waste processing to recover carotenoids ,Resour. Technol. , Vol. 3 (3),pp 252–262 , 2017, https://doi.org/https://doi.org/10.1016/j.reffit.2017.08.007
, A Mass Balance Method for Assessing Emergy Benefit of Waste Mining for Refuse Derived Fuel Production ,International Journal of Environmental Science and Development , Vol. 8 (6),pp 448–453 , 2017, https://doi.org/https://doi.org/10.18178/ijesd.2017.8.6.995
, The bibliometric analysis and review of dioxin in waste incineration and steel sintering ,Environ. Sci. Pollut. Res. , Vol. 26 (35),pp 35687–35703 , 2019, https://doi.org/https://doi.org/10.1007/s11356-019-06744-0
, Thermogravimetry as a research method in the transformationprocesses of waste rubber and plastic products for energy carriers (WtE and WtL processes) ,J. Sustain. Dev. Energy, Water Environ. Syst. , Vol. 1 (2),pp 163–171 , 2013, https://doi.org/https://doi.org/10.13044/j.sdewes.2013.01.0012
, A review on alternative fuels in future energy system ,Renew. Sustain. Energy Rev. , Vol. 128 (May), 2020, https://doi.org/https://doi.org/10.1016/j.rser.2020.109927
, Experimental investigation to identify the type of waste plastic pyrolysis oil suitable for conversion to diesel engine fuel ,J. Clean. Prod. , Vol. 246 ,pp 119066 , 2020, https://doi.org/https://doi.org/10.1016/j.jclepro.2019.119066
, Biofuels production through biomass pyrolysis- A technological review ,Energies , Vol. 5 (12),pp 4952–5001 , 2012, https://doi.org/https://doi.org/10.3390/en5124952
, Activated Carbon by Co-pyrolysis and Steam Activation from Particle Board and Melamine Formaldehyde Resin: Production, Adsorption Properties and Techno Economic Evaluation ,J. Sustain. Dev. Energy, Water Environ. Syst. , Vol. 1 (1),pp 41–57 , 2013, https://doi.org/http://doi.org/10.13044/j.sdewes.2013.01.0004
, An overview of chemical additives present in plastics: Migration, release, fate and environmental impact during their use, disposal and recycling ,Journal of Hazardous Materials , Vol. 344 ,pp 179–199 , 2018, https://doi.org/https://doi.org/10.1016/j.jhazmat.2017.10.014
, Co-pyrolysis of biomass and waste plastics as a thermochemical conversion technology for high-grade biofuel production: Recent progress and future directions elsewhere worldwide ,Energy Conversion and Management , Vol. 163 ,pp 468–492 , 2018, https://doi.org/https://doi.org/10.1016/j.enconman.2018.02.004
, Production and characterization of pyrolysis oil using waste polyethylene in a semi batch reactor ,Indian J. Chem. Technol. , Vol. 25 (4),pp 336–344 , 2018
, Pyrolysis of plastic waste for liquid fuel production as prospective energy resource ,IOP Conf. Ser. Mater. Sci. Eng. , Vol. 334 (1), 2018, https://doi.org/https://doi.org/10.1088/1757-899X/334/1/012001
, Effect of pyrolysis temperature on chemical and physical properties of sewage sludge biochar ,Waste Manag. Res. , Vol. 33 (3),pp 275–283 , 2015, https://doi.org/https://doi.org/10.1177/0734242X14565210
, Effects of different conditions on co-pyrolysis behavior of corn stover and polypropylene ,Polymers (Basel). , Vol. 12 (4), 2020, https://doi.org/https://doi.org/10.3390/POLYM12040973
, A review on pyrolysis of plastic wastes ,Energy Convers. Manag. , Vol. 115 ,pp 308–326 , 2016, https://doi.org/https://doi.org/10.1016/j.enconman.2016.02.037
, Quantitative correlation of physical and chemical properties with chemical structure: Utility for prediction ,Chem. Rev. , Vol. 110 (10),pp 5714–5789 , 2010, https://doi.org/https://doi.org/10.1021/cr900238d
, - Commodity Thermoplastics: Polyvinyl Chloride, Polyolefins, and Polystyrene, 2010, https://www.sciencedirect.com/science/article/pii/B9780815520276100066
The synergistic effect of co-pyrolysis of oil shale and low density polyethylene mixtures and characterization of pyrolysis liquid ,J. Energy Inst. , Vol. 90 (3),pp 355–362 , 2017, https://doi.org/https://doi.org/10.1016/j.joei.2016.04.007
, Recycling of waste plastics into fuels. LDPE conversion in FCC ,Applied Catalysis B: Environmental , Vol. 125 ,pp 499–506 , 2012, https://doi.org/https://doi.org/10.1016/j.apcatb.2012.06.020
, Yield and Composition of Gases and Oils/Waxes from the Feedstock Recycling of Waste Plastic ,Feed. Recycl. Pyrolysis Waste Plast. Convert. Waste Plast. into Diesel Other Fuels ,pp 285–313 , 2006, https://doi.org/https://doi.org/10.1002/0470021543.ch11
, Char formation and gas products of woody biomass pyrolysis ,Energy Procedia , Vol. 32 ,pp 145–152 , 2013, https://doi.org/https://doi.org/10.1016/j.egypro.2013.05.019
, Route Design in the 21st Century: The ICSYNTH Software Tool as an Idea Generator for Synthesis Prediction ,Organic Process Research & Development , 2015, https://doi.org/https://doi.org/10.1021/op500373e
, Pyrolysis of Waste Plastics into Fuels ,PhD Thesis ,pp 216 , 2010
, Pyrolysis oil composition and catalytic activity estimated by cumulative mass analysis using Py-GC/MS EGA-MS ,Energy , Vol. 219 ,pp 119428 , 2021, https://doi.org/https://doi.org/10.1016/j.energy.2020.119428
, A review on polycyclic aromatic hydrocarbons: Source, environmental impact, effect on human health and remediation ,Egypt. J. Pet. , Vol. 25 (1),pp 107–123 , 2016, https://doi.org/https://doi.org/10.1016/j.ejpe.2015.03.011
, Impact of fuel molecular structure on auto-ignition behavior - Design rules for future high performance gasolines ,Prog. Energy Combust. Sci. , Vol. 60 ,pp 1–25 , 2017, https://doi.org/https://doi.org/10.1016/j.pecs.2016.12.001
,