A future sustainable energy system will be based on renewable energy sources (RES), mainly wind and solar [1]. Due to the volatile nature of these resources, energy storage and flexible demand will become critical to meeting energy needs. In addition, sector coupling, i.e., linking electricity, heat, gas, or transport, can be a way to use renewable energy sources for previously non-electrified processes such as heat supply via natural gas boilers. In this context, electricity from renewable energy sources becomes the primary energy instead of fossil fuels. Therefore, sector coupling is another important step towards defossilising all energy use [2]. At the same time, a sustainable energy system also includes the efficient use of energy to limit resource consumption (land, metals, water, etc.) as much as possible [3].
In terms of energy needs, a high amount of energy is used to provide heat for room heating, domestic hot water, and process heating. For example, in Germany, more than 60% of the final energy demand in the industry is caused by process heating [4], whereby the term process heat here includes different requirements concerning the temperature or the type of provision. In recent studies, the defossilisation of industrial process heat has become of more interest [5]. In this context, Wei et al. show the potential of direct electrification [6], while Neuwirth et al. focus on indirect electrification via hydrogen [7]. Bühler et al. analyse the impact of such a defossilised industry sector in Denmark [8]. Thus, the choice of a heating system impacts the design of the energy supply system. Selleneit et al. [9] introduced an approach for assessing industrial utilities in terms of their suitability for integrating variable renewable energies regarding fourteen property characteristics in the four categories energy efficiency, reaction ability, performance ability and demand adaptability.
Electrified processes can increase system efficiency with the ongoing energy transition and the increased expansion of renewable energies. Firstly, by reducing energy demand through greater efficiency and, secondly, by responding flexibly to energy peaks and troughs. However, both goals can conflict with each other. Heat pumps are a great lever to defossilise the process heat supply because they use environmental or industrial waste heat and can use renewable electricity. Heat pumps available on the market can reach sink temperatures of up to 160 °C [10]. Selleneit et al. [11] conclude that a heat pump scored slightly better than an electrode boiler concerning the approach presented in [9]. In terms of energy efficiency, the heat pump is more convincing. As the target temperature rises [12] and the variability of the heat sink and heat source increases [13], the flexible properties of the electric boiler may outweigh those of the heat pump. Walden et al. [14] compared the cost-optimised use of a high-temperature heat pump to an electric boiler (EB), both in combination with thermal energy storage (TES), for the consumption of fluctuating wind power. Since heat pumps can only exploit their efficiency advantage compared to electrode boilers through longer periods of full operation, they are predominantly used as an efficiency measure [12].
Pinch Analysis as a process integration method offers a graphical tool in the form of the Grand Composite Curve (GCC), which can be used to read out target values for the minimum heating and cooling demands of a process at the corresponding temperature level. Townsend and Linnhoff [15] were the first to discuss the correct integration of heat pumps using the GCC, according to which the heat pump is to be integrated only by heat absorption below the pinch temperature and heat release above it. Failure to follow this integration rule even leads to an increase in cooling demand in the worst case. Schlosser et al. [16] summarised process-specific GCC of industrial case studies from meat, dairy and metal processing as well as electroplating, paper production and sterilisation. Suppose the real process conditions differ from the idealised assumptions of the Pinch Analysis because the heat recovery potential cannot be fully exploited. Heat pumps can also be integrated into the existing heat exchanger network using the Heat Pump Bridge Analysis based on the Modified Energy Transfer Diagram [17]. Storages can be used in batch processes where heat and cooling demand are separated in time. The Indirect Sink and Source Profile method enables the correct dimensioning of storage to unlock the heat-pumping potential of these non-continuous processes [18].
In contrast to heat pumps, electric boilers have lower energy efficiency ratios but offer a higher potential for flexible operation. In the context of sustainable energy systems, this flexibility potential can be used for demand shifting to meet the power supply of wind turbines and PV plants. Demand shifting is widely discussed in scientific literature. Concerning industrial applications [19], demand shifting within a process is discussed for the aluminium, cement, chemistry, and pulp and paper industry [20]. In addition, demand shifting potential of further cross-sectoral industrial processes is discussed, like heating [21], ventilation, and air conditioning systems [22], cooling systems [23], manufacturing lines [13], power to heat for steam supply in the industry [24] or touristic facilities [25]. The potential of flexible demand of electric boilers for process heat in Germany is evaluated in [26]. All studies show the advantage of demand shifting to increase the degree of utilisation of RES.
The review underlines that both components, the heat pump and electric boiler, have different characteristics, which lead to different impacts on an energy system. Industrial heat pumps are mainly considered energy efficiency measures, while electric boilers offer greater potential for a more flexible demand. Regarding the described challenges to reach a sustainable energy system, it is still not well analysed which impact hybrid process heat supply systems based on both technologies will have on industrial utilities' economic and ecological performance.
Thus, this study aims to examine different direct electrification measures economically based on a case study under the different superordinate system issues of energy efficiency and flexibility. These measures are compared to a natural gas-fired boiler as the conventional reference system. In addition, a variant that can combine both types is discussed and compared. The paper is structured as follows: The case study is described before the underlying data, assumptions, and scenarios are explained in the Materials and Methods section. Furthermore, the optimisation methods used are described with the corresponding mathematical formulations. Finally, the results are summarised, discussed, and a conclusion is drawn.
This chapter explains the case study and all databases, scenarios, and assumptions.
For the production of canned foods, retort pouches, aluminium trays and bowls, thermal processing is one of the main food conservation methods. Providing long-term preservation and commercial sterility via the inactivation of pathogenic and food-spoiling microorganisms is the basic function of the sterilisation process in a batch retort. Heat processing temperature is well above 100 °C, and pressurised steam retorts, called autoclaves, are used to achieve commercial sterility [27]. In the investigated batch retort sterilisation process for pet food pouches [28], the sterilisation temperature is 120 °C and requires steam injection at 130 °C. Figure 1 illustrates that the maximum energy demand occurs only during the first few minutes of the process cycle to reach the sterilisation temperature ("Come-up Time"), while very little is needed after that to maintain process temperature ("Holding"). The pouches are then cooled down to 40 °C with cooling water. Ultimately, condensate and cooling water mix and leave the process at approximately 80 °C. Time and temperature differences between cooling water and steam inhibit direct heat recovery and only allow heat pumping based on TES.
Batch sterilisation process with corresponding sink and source profile for heat pump integration
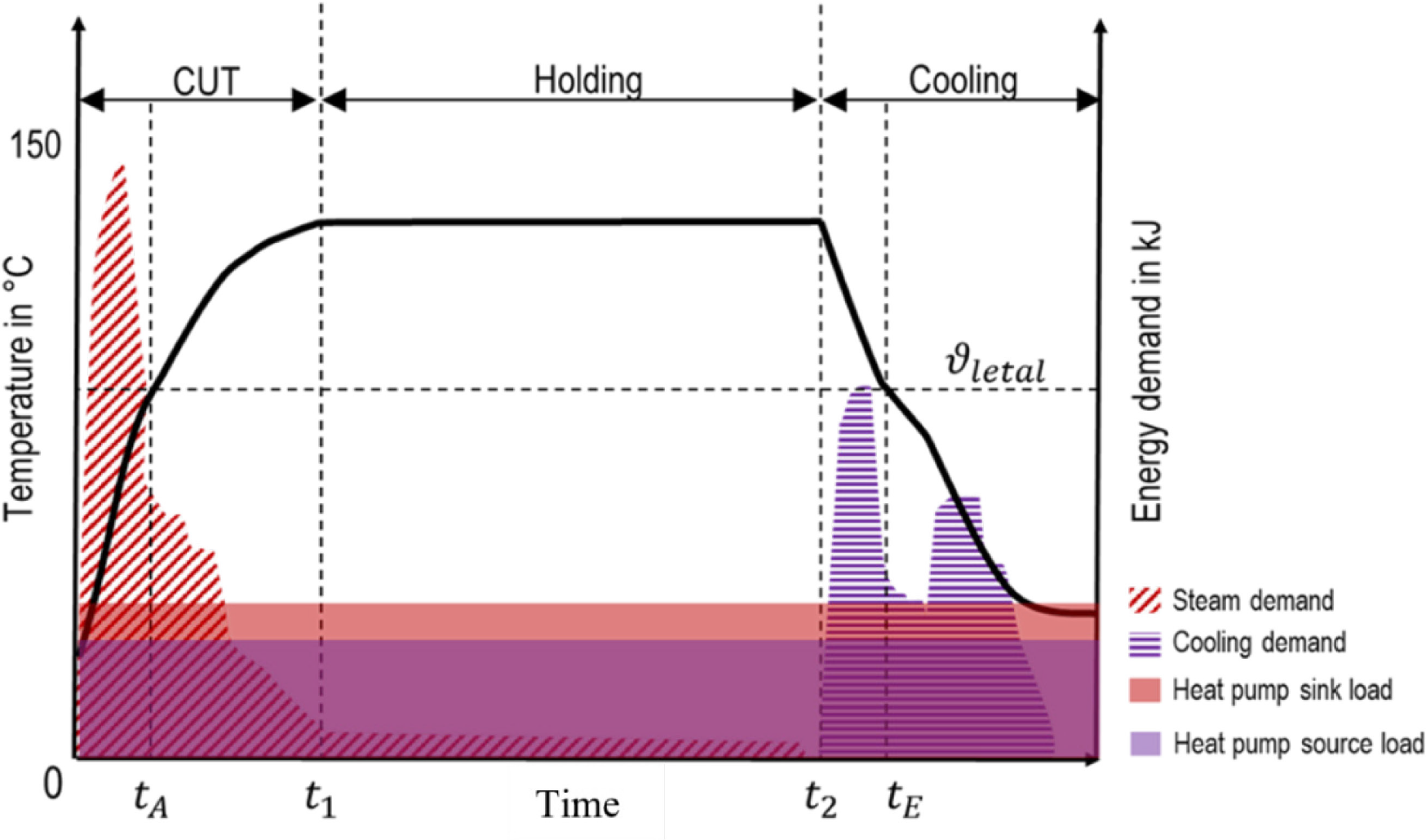
To compare both ways of sustainable heat supply for the presented process, one reference scenario and three scenarios using a heat pump and/or electric boiler are considered. All three electrified scenarios also include TES. The chosen scenarios are as follows:
Scenario Gas Boiler: A gas-fired boiler is used as a reference scenario. The boiler supplies the heat on demand and is dimensioned according to the maximum heat demand.
Scenario Heat Pump: In this scenario, the focus is on maximising energy efficiency. Therefore, an optimal design of a heat pump system is done by pinch analysis and mathematical optimisation of storage size.
Scenario Electric Boiler: In this scenario, an electric boiler is chosen instead of a heat pump; thus, the focus is on maximal flexibility. A linear program (LP) determines the boiler's operation schedule.
Scenario Hybrid: This scenario is chosen to analyse the interaction of both technologies. Hence, both technologies are used and sized according to the objective to minimise annual costs via a mixed-integer linear program (MILP).
Annual system costs are considered to quantify the economic aspects of all configurations. In addition to annual operation costs caused by electricity or natural gas demand, annual investment costs Ia is determined according to eq. (1) considering the lifetime L, the interest rate i, and the specific investment costs I:
(1)
Table 1 shows the cost components for the annual investment costs. According to Walden et al. [14], the specific investment costs for heat pumps range from 150 to 1000 /kWth and depend strongly on the system integration costs. In the following, 600 /kWth was assumed. Due to the higher risk factor in the financing of Very High-Temperature Heat Pumps (VHTHP), an interest rate of 0.12 is assumed for them, according to Schlosser [29]. In comparison, an interest rate of 0.07 is assumed for long-established systems such as the gas boiler [30]. A lifetime of 20 years is assumed for steam accumulators.
Parameters for investment cost accounting
VHTHP | EB | GB | Storage | |
---|---|---|---|---|
Invest I [/kWth] | 600 [31] | 135 [32] | 250 [30] | 32.61 [/kWh] [33] |
Lifetime L [a] | 20 [29] | 20 [32] | 25 [30] | 20 |
Efficiency η | > 1 | 0.99 [32] | 0.90 [30] | - |
Interest rate i | 0.12 [29] | 0.07 | 0.07 [30] | 0.07 |
The data on the quarter-hourly steam demand for the case study come from Hechelmann et al. [34]. For the steam accumulator, an efficiency of 100% is assumed for charging and discharging, and 99.78% is assumed for the efficiency of the accumulator over a time step [35]. In the reference case, the gas boiler without a storage tank is designed for the maximum demand (5860 kW). The average natural gas price png for non-household customers in the EU in the second semester of 2021 was 4.16 ct/kWh, according to Eurostat [36].
Various approaches have been considered to create flexible prices to incentivise system-serving operations. One possibility would be to adopt time-resolved prices based on the wholesale prices of the European Power Exchange with additional costs for grid services and taxes. However, these prices do not fully correlate with the emission intensity of the electricity mix [37]. To represent both flexible prices and to reduce the emission intensity, a synthetic time series for electricity prices in ct/kWh according to equation (2) is used in the following:
(2)
The values for the quarter-hourly resolved carbon dioxide (CO2) emission factor of the German electricity mix in gCO2/kWh are taken from Blizniukova et al. [38] for the years 2017 (17) and 2019 ('19). The average price for electricity is 14.45 ct/kWh according to [39] and describes the average price for non-households in the EU in the second semester of 2021.
Figure 2a shows the distribution of prices in two time series for 2019 and 2017. The distribution is flatter in 2019 compared to 2017, and the spread from maximum (17: 21.35 ct/kWh, 19: 24.24 ct/kWh) to minimum values (17: 5.27 ct/kWh, 19: 4.80 ct/kWh) is larger. Figure 2b shows the course of the synthetic prices over the time steps. Also, greater deviations from the mean in 2019 can be seen, and the peaks and troughs occur at different times than in 2017. Negative prices on the electricity balancing market due to short-term energy consumption or other financial incentives for offering flexibility, such as participation in the reserve market, are neglected.
Quantitative representation of the synthetic time series for quarter-hourly resolved electricity prices 17 & 19
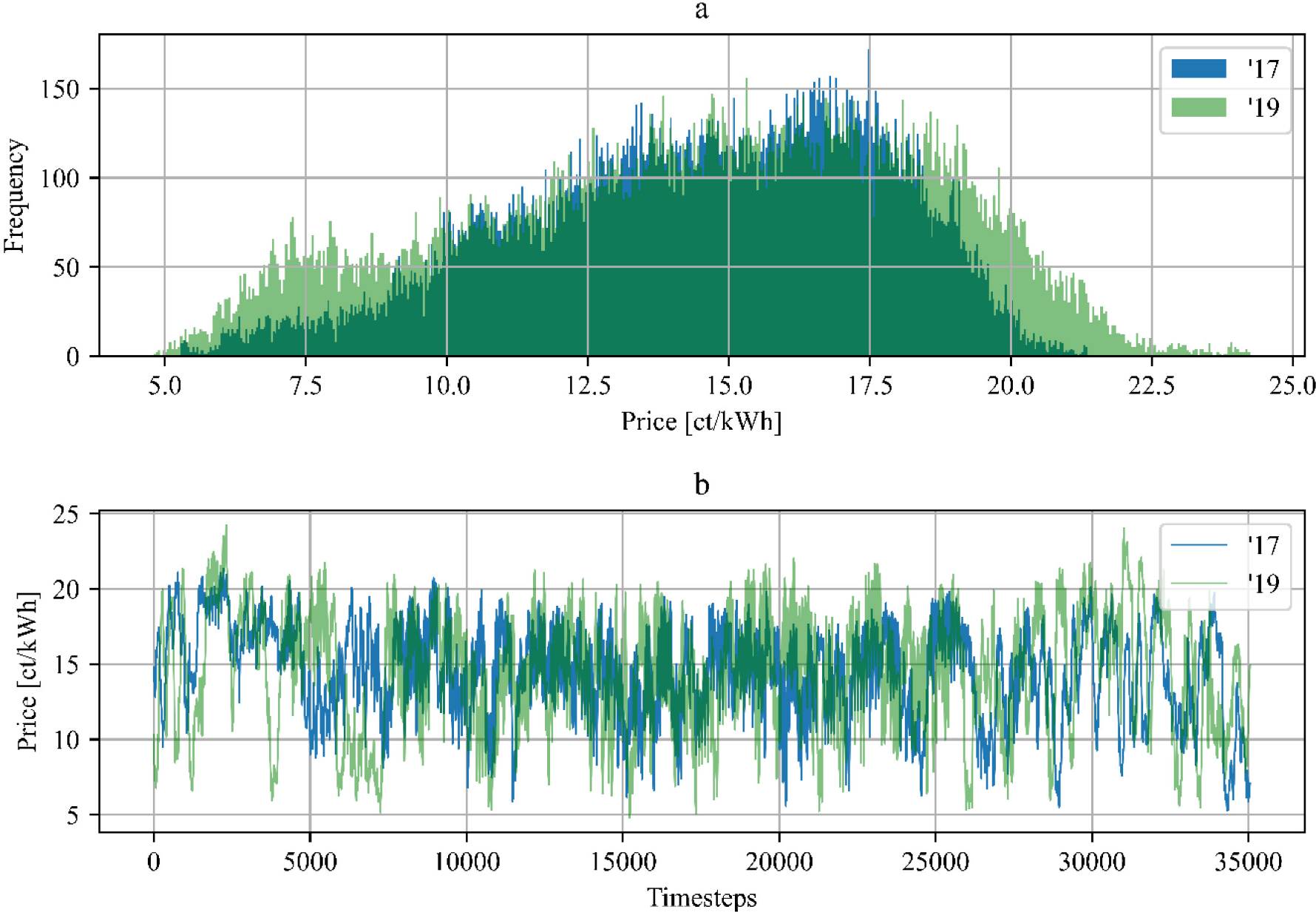
All three scenarios need different methods for dimensioning the plant and storage size and enabling an optimised operation of the utilities. The methods used for all three scenarios are explained in detail in the following subsections.
The core of this scenario is a heat pump dimensioned according to Process Integration principles. Therefore, firstly, the stream data of the process are to be defined as input data for the Pinch Analysis. For batch processes, the average load is modelled for this purpose. According to the Time-Average-Method, this concept is based on storing the heat taken from the leaving cooling process stream in warm storage to be used again for heating later.
According to the optimisation variant Process Integration, the heat pump is integrated with the help of the GCC using the COP curve [16]. If the evaporator capacity is calculated for the shifted temperatures from the pinch temperature to the lowest source temperature based on the following equation (3), these value pairs form the COP curve (black line in Figure 3a). The intersection of the GCC and COP curves defines the required evaporator capacity (square mark Figure 3a) at the corresponding temperature level:
(3)
Integration of a heat pump into the GCC by COP-curves (a) and schematic illustration of heat pump parameters (b)
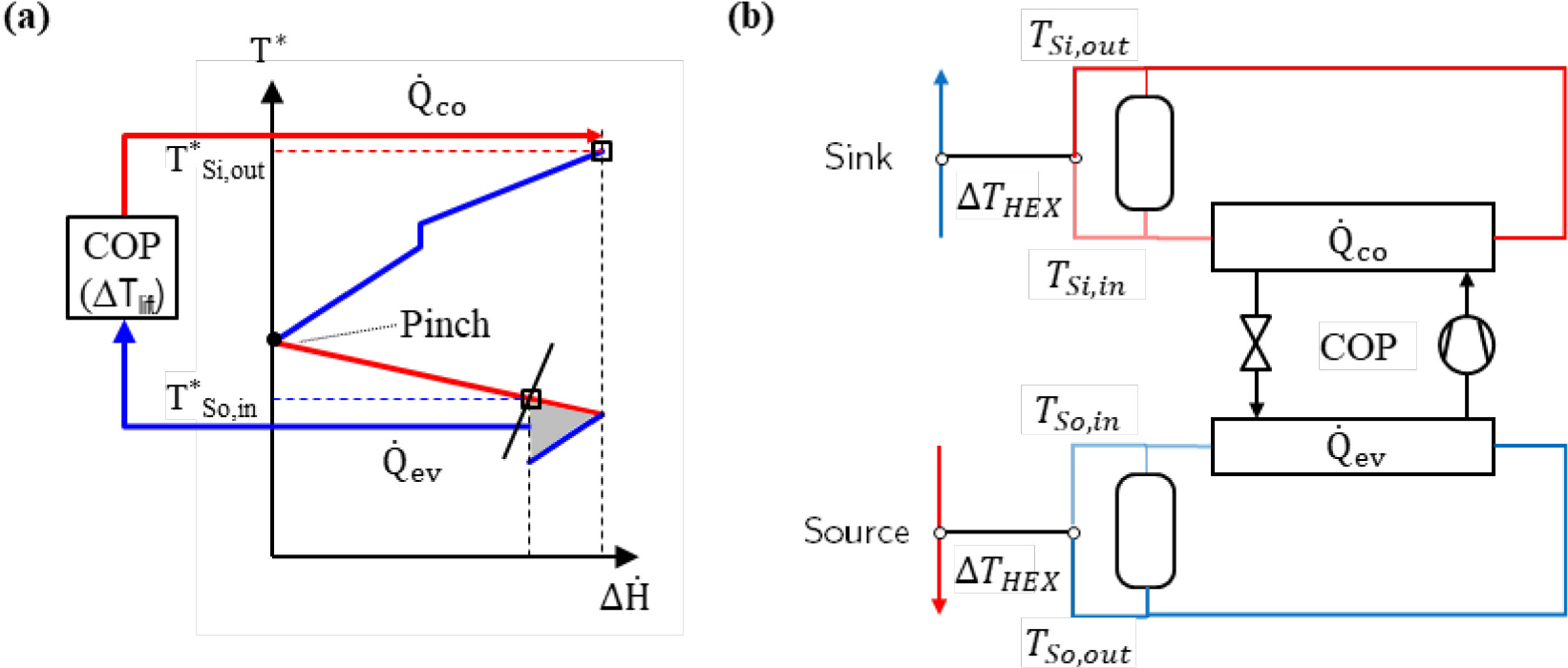
The COP of a VHTHP is determined by a regression model of market-available performance data based on equation (4) depending on the target sink temperature T(Si,out) and the temperature lift ΔTlift between heat sink (Si) and source (So) [12]. Market-available VHTHPs for steam generation achieve sink temperatures T(Si,out) of up to 165 °C with temperature lifts ΔTlift of up to 115 K [31]:
(4)
(5)
Since the heat transfer between a heat sink and source is already represented in the COP regression models, the COP is determined based on the temperature of the heat sink leaving the condenser TSi,out and the temperature of the heat source entering the evaporator TSo,in (see Figure 3b). For the heat recovery loop shown in Figure 3b, the input variables for the COP calculation are determined considering a source-side temperature spread of ΔTSo = 3 K due to the nominal temperatures of the test conditions according to DIN EN 1511-2 [40] as follows:
(6)
(7)
(8)
The heat pump is designed using the GCC. For this purpose, the average steam demand is determined according to equation (9), and the associated COP is calculated via equation (4) using the parameters from Table 2.
Regression parameters of the COP for VHTHPs [12]
VHTHP | Fitting parameter | |||
---|---|---|---|---|
Steam-based VHTHP | a = 8.898 | b = 0.042214 | c = -0.52137 | d = 0.16395 |
Due to the higher average steam demand at the beginning of the data set, the heat pump is designed to be 10% larger. This results in a thermal output of the heat pump of 2259 kW and a COP of 2.22:
(9)
The VHTHP is operated constantly, and a fixed electricity price is assumed. When calculating the annual operating costs, it is also considered that the VHTHP reduces the cooling demand. It is assumed that electrical costs would otherwise be incurred for the cooling tower (COPCT: 10 [41]); these are deducted from the VHTHP.
In addition, the steam accumulator is optimised using Linear Programming (LP) formulation as follows:
(10)
A variable is introduced for the maximum storage size which must be constant at each time step. It is defined as the upper bound for the variable of the storage content :
(11)
(12)
Furthermore, energy (14) and storage (15) balances are necessary, as well as another condition to ensure that the heat pump is operated constantly (13):
(13)
(14)
(15)
This results in the following variable (16) and cost vector (17):
(16)
(17)
An LP is used for the mathematical formulation of the problem of operation optimisation and sizing of the Boiler. It is based on the considerations of Wolf et al. [35]. Due to the temporal resolution of 15 minutes, the ramp-up times of 1-2.5 minutes [42] are neglected in the formulation. Constraint (18) states that the size of the electric boiler can only take one value and constraint (19) sets the size of the electric boiler as the upper bound for the maximum steam production :
(18)
(19)
In the energy balance, the constant value of the VHTHP is replaced by the continuous variable of the electric boiler :
(20)
This results in the cost and variable vector as follows:
(21)
(22)
A MILP is set up for optimisation with a VHTHP and an electric boiler. For this purpose, each binary variable serves as a decision variable on whether a heat pump with an associated thermal capacity (between 0 and 2260 kW in 10 kW steps) and the corresponding is installed. Constraint (23) ensures that only one heat pump can be built, and constraint (24) that it is the same for each time step:
(23)
(24)
The energy balance of (20) must be adjusted to include the thermal output of the installed heat pump:
(25)
Cost and variable vector, as shown in (16) and (17), must be extended, compared to the case without a heat pump:
(26)
(27)
The operating and investment costs result in the total annual costs of 0.9573 M for the reference case. The annual costs for the electrification measures considered are shown in Table 3. None of the electrification measures are economically viable under the assumed prices.
Results
Case | Cost [M€/a] | VHTHP size [kW] | EB size [kW] | Storage size [kWh] |
---|---|---|---|---|
Heat Pump | 1.3629 | 2259 | - | 59,436 |
Electric Boiler (‘17) | 2.6393 | - | 5240 | 19,955 |
Hybrid System (‘17) | 1.2142 | 1950 | 543.1 | 24,454 |
Electric Boiler (‘19) | 2.5776 | - | 6642 | 27,810 |
Hybrid System (‘19) | 1.2097 | 1950 | 651.8 | 24,454 |
Using an electric boiler with a flexible price tariff is almost twice as expensive as using a heat pump with a fixed price tariff for both scenarios considered. The integration of an electric boiler together with the heat pump at the flexible price tariff has a cost advantage over the heat pump alone in both scenarios considered.
In the hybrid case, the heat pump covers 94.95% of the steam demand. Depending on the scenario, the annual cost advantage amounts to 10.9% and 11.2% compared to the process integration of only a heat pump. Whereby between 10% and 12% can be attributed to the savings in investment costs of the heat pump, the rest is achieved through the flexible operation of the boiler.
Integrating a heat pump into the process means 23.7% (17) to 36.3% (19) of CO2 emissions can be saved during operation compared to the reference case due to the higher efficiency, as seen in Figure 4. Even 27.6% (17) to 39.86% (19) can be saved in the hybrid system. In contrast, the emissions would increase by 17.7% (19) and 47.1% (17) if an electric boiler was used.
Changes in CO2 emissions compared to the reference case for the years 17 and '19
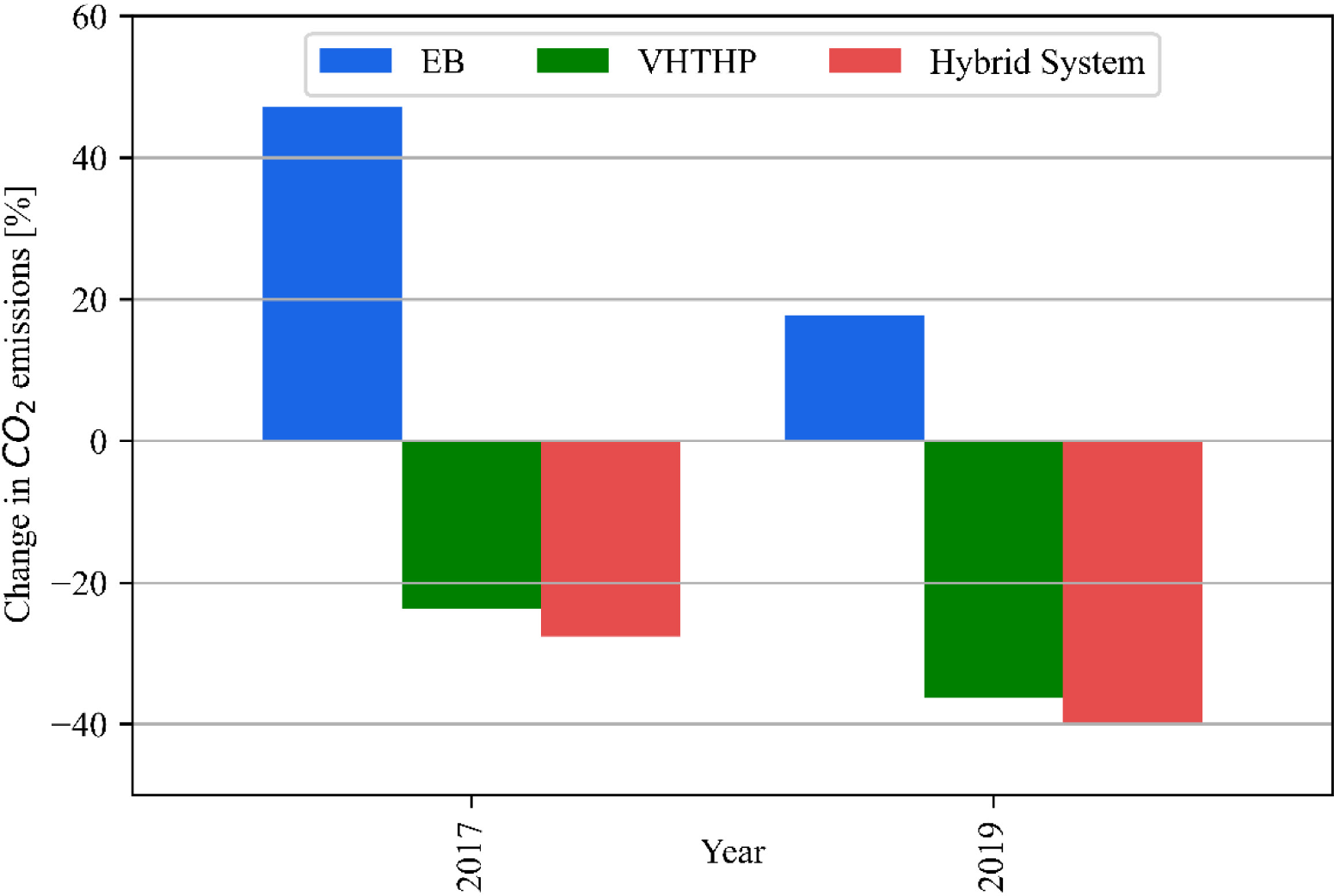
Since energy prices, such as gas and electricity, and investment costs vary greatly depending on the production system, a sensitivity analysis is carried out in the following. Here, the average electricity prices are assumed to be ± 20% (17.34. ct/kWh to 11.56 ct/kWh) for the hybrid system with the fluctuations of the year 2017. For the same case, the investment costs are varied by ± 20% (720 /kW to 480 /kW). For comparison, the gas price (4.99 ct/kWh to 3.33 ct/kWh) and the investment costs for the gas boiler (300 /kW to 200 /kW) are varied similarly. Figure 5 shows the results of this sensitivity analysis. The investment costs for both cases have a significantly smaller impact than a change in energy prices. It shows that a 20% reduction in electricity prices would not be enough for the hybrid system to achieve cost parity with the reference case. It would require a reduction in electricity prices of about 15% with a simultaneous increase in gas prices of about 10%, which means an electricity-to-gas price ratio of approximately 2.67.
Sensitivity analysis on electricity and gas prices, as well as the investment costs of the VHTHP of the hybrid system '17 and the gas boiler
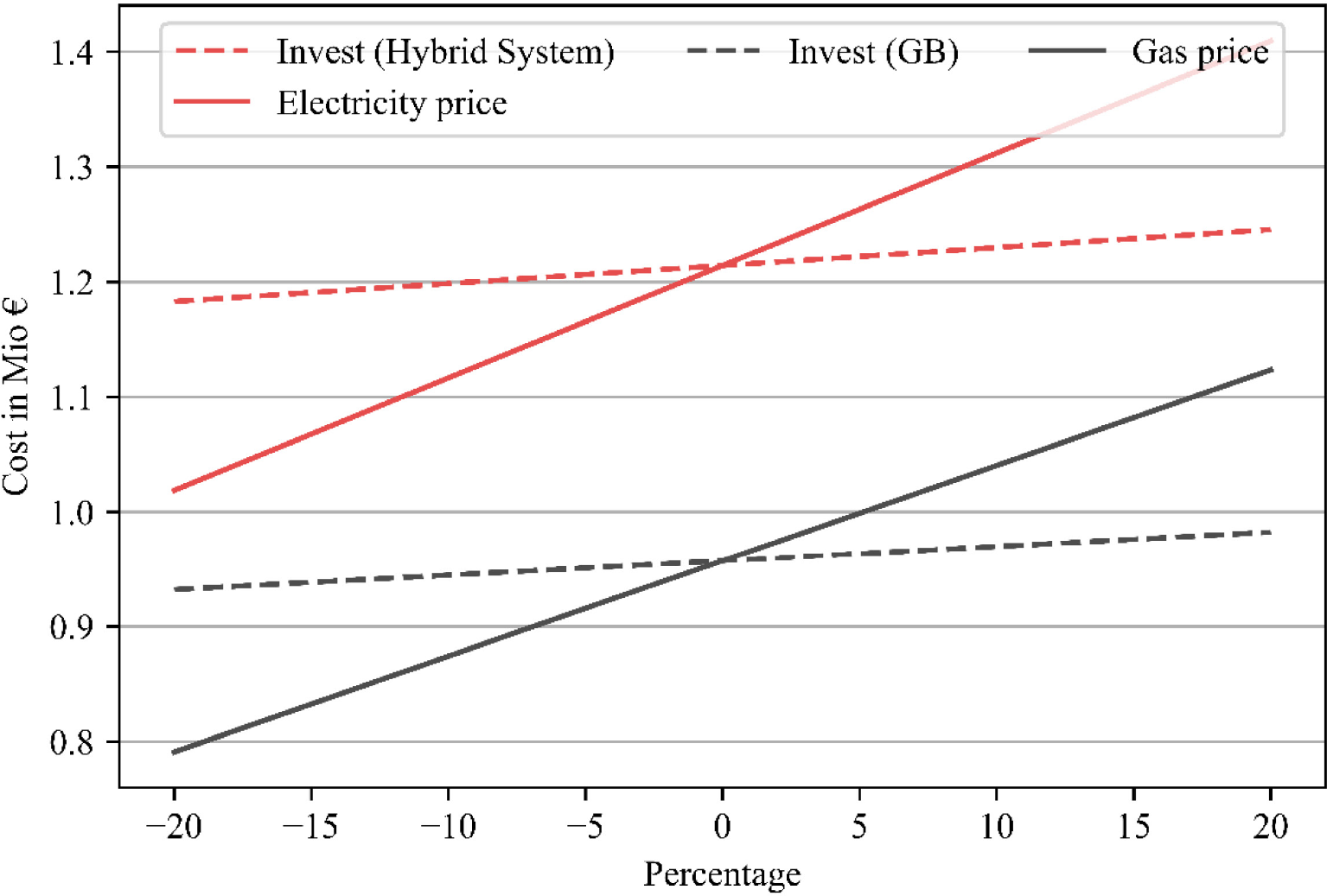
The electrification of process heat generation using renewable energies has clear efficiency advantages over the combustion of fossil fuels and is also potentially climate neutral. Furthermore, these alternatives are almost economically competitive under the natural gas price for 2021. For a climate-neutral economy and industry, however, direct or indirect electrification is unavoidable, as the emission factor in the electricity mix will decrease, but that of natural gas will remain constant.
However, economic competitiveness depends heavily on the electricity-to-gas price ratio [12]. Recent developments show that energy prices are rising, among other things, due to increasing CO2 prices. While these remain the same for fossil fuels, electricity prices will be less affected as the expansion of renewable energies continues. The hybrid system would break even at a natural gas price of 5.42 ct/kWh, representing an electricity-to-gas price ratio of 2.67, with the assumed electricity price of 14.45 ct/kWh. While the electricity-to-gas price ratio for the prices considered in 2021 was 3.47, it was 2.81 for the average prices in the first semester of 2022 [43], [44]. Although, according to the merit order principle, the electricity price rises with the gas price, the ratio became better in favour of the electricity price. It suggests that the systems with heat pumps would perform even better.
Nevertheless, the assumed prices from 2021 are more representative due to the probably temporary energy crisis in Europe. In addition to the economic impact of the geopolitical events in 2022, they have clarified that European industry needs to become independent of fossil fuels. To achieve this, it will be necessary to reduce energy consumption by increasing efficiency and strengthening the use of local renewable energy sources. In the latter context, the ability to react flexibly to power peaks will become more important. Hybrid systems such as the one discussed can contribute to both aspects, i.e., efficiency and flexibility.
In addition, it must be discussed to what extent a larger spread between high and low-price phases would impact the economic viability of a flexible system. This widening is likely with a larger share of volatile RES in the grid. Within the literature, several designs of future energy price models are discussed. In this context, Dunkelberg et al. [24] highlight the different shapes of residual loads for different regions and their influences on the need for flexible electricity demand. Heidrich et al. [22] underline how the spread between high and low prices can be modified and how this may influence the demand response potential. The effects of scenarios with a higher spread between high and low-price phases need further investigation.
The calculated costs for the flexible system with the electric boiler and the hybrid system using the synthetic time series of prices are purely theoretical, as there are currently only limited financial incentives for big scaled industrial companies to run their plants flexibly. In addition, the approach neglects negative prices that would be possible for the provision of load in the event of an oversupply of energy for grid stabilisation. Since the systems, such as boilers and storage tanks, were designed for optimal operation based on the price signals, they differ depending on the scenario. The plants would probably have to be designed somewhat larger, and the total annual costs should therefore be assumed to be higher. Furthermore, the specific investment costs can vary considerably. Especially for heat pumps, these are, as discussed, in a wide range and depend on the system in which they must be integrated. Also, the assumed interest rates can differ significantly depending on how companies assess the risks related to new technologies and an increasing need for energy saving and defossilisation. These and other uncertainties, like changing CO2, electricity, and gas prices, should be investigated in further work to estimate future annual operating costs to support investment decisions better.
The shown advantage and the hybrid system's design depend strongly on the observed process. However, batch sterilisation processes are common and can be found in many companies. Nevertheless, applying the presented methods and comparison to other case studies would highlight the potential of hybrid systems combining energy efficiency and flexible demand for a wide range of applications. It may be part of the future energy system and defossilised steam supply. Other processes for which a pinch analysis has already been carried out (e.g., see [29]) offer good points for further research and should be considered. The mathematical formulation may also need to be extended depending on the process. Partial load operation of the heat pump and downtimes would be possible.
Based on this, it should also be considered how the overarching comparison between energy efficiency and flexibility can be extended to dimensions above a single process and how this affects the grid and energy management. The focus here is on how much flexibility is needed in regional (but interconnected) energy systems to cope with the fluctuating integration of renewable energies into the distribution grids as much as necessary. In this context, the potential of flexible heat supply and other flexible loads, such as electric vehicles, power-to-gas, energy storage, etc., can be of great interest to investigate their potential and the interactions between these loads in future regional energy systems.
The findings of this study underline that electrification measures for process heat in the case study under consideration are almost economically viable at average European prices of 2021. However, the results also show that electrification can already have a high environmental benefit. Regarding the economic assumptions made, the reference system (natural gas) is the economically best alternative. Among the electrified solutions, a fully flexible system with an electric boiler has the highest annual costs, while an efficient system with a heat pump can halve the annual costs. The hybrid solution, which combines flexibility and efficiency, leads to the lowest costs of all electrified solutions and is competitive with the natural gas system at an electricity-gas price ratio of 2.67. It shows that the joint use of an efficient heat pump and a flexible boiler results in advantages, as the boiler can use flexible prices and simultaneously reduce the investment costs of the heat pump through smaller dimensioning. Considering also the GHG emissions of all systems, the case study underlines the advantage of electrified solutions. Increasing efficiency using a heat pump reduces emissions by 24.7% to 36.3% compared to the reference case using the emission factor of the German electricity mix in 2017 and 2019. The hybrid solution leads to further benefits resulting in a reduction potential of 39.9% compared to using natural gas if the prices are sufficiently correlated with the emission factor of the electricity mix. Thus, the case study results highlight how both characteristics, i.e., flexibility and efficiency, may be required to establish the solution with the lowest GHG emissions. Gas prices are increasing, not least because of carbon pricing. Combined with the political will to reduce the dependence on fossil fuels and the aim to realise carbon-neutral energy systems, it will further increase the already high potential of electrified solutions for economic and ecologically sustainable steam supply in industries.
COP | Coefficient of performance | [-] |
c | Cost vector | [-] |
E | Energy | [kWh] |
e | Emission coefficient | [gCO2/kWh] |
i | Interest rate | [%] |
L | Lifetime | [a] |
N | Number of timesteps | [-] |
p | Price | [ct/kWh] |
Power | [kW] | |
T | Temperature | [K] |
x | Variable vector | [-] |
Greek letters | ||
η | Efficiency coefficient | [-] |
τ | Timestep width | [h] |
Subscripts | |
a | Year |
avg | Average |
co | Condenser |
CO2 | Carbon dioxide |
CT | Cooling Tower |
EB | Electric boiler |
el | Electric |
ev | Evaporator |
D | Demand |
HP | Heat Pump |
max | Maximal |
ng | Natural gas |
S | Storage |
Si | Heat Sink |
So | Heat Source |
th | thermal |
t | Timestep |
Abbreviations | |
EB | Electric Boiler |
GCC | Grand Composite Curve |
GHG | Greenhouse Gas |
LP | Linear Programming |
M, Mio | Million |
MILP | Mixed Integer Linear Programming |
RES | Renewable Energy Sources |
TES | Thermal Energy Storage |
VHTHP | Very High-Temperature Heat Pump |
Radical transformation pathway towards sustainable electricity via evolutionary steps, ,Nature communications , Vol. 10 (1),pp 1077 , 2019, https://doi.org/https://doi.org/10.1038/s41467-019-08855-1
, The potential of sector coupling in future European energy systems: Soft linking between the Dispa-SET and JRC-EU-TIMES models ,Applied Energy , Vol. 267 ,pp 115100 , 2020, https://doi.org/https://doi.org/10.1016/j.apenergy.2020.115100
, Environmental Impact of Solar and Wind energy- A Review ,J. sustain. dev. energy water environ. syst. , Vol. 10 (2),pp 123 , 2022, https://doi.org/https://doi.org/10.13044/j.sdewes.d9.0387
, - https://www.umweltbundesamt.de/daten/energie/energieverbrauch-fuer-fossile-erneuerbare-waerme#warmeverbrauch-und-erzeugung-nach-sektoren ,
Electrification of industrial process heat: long-term applications, potentials and impacts ,ECEEE Industrial Summer Study Proceedings , 2018
, Electrification of Industry: Potential, Challenges and Outlook ,Curr Sustainable Renewable Energy Rep , Vol. 6 (4),pp 140148 , 2019, https://doi.org/https://doi.org/10.1007/s40518-019-00136-1
, The future potential hydrogen demand in energy-intensive industries - a site-specific approach applied to Germany ,Energy Conversion and Management , Vol. 252 ,pp 115052 , 2022, https://doi.org/https://doi.org/10.1016/j.enconman.2021.115052
, - , Potentials for the electrification of industrial processes in Denmark, Proceedings of ECOS 2019: 32nd International Conference on Efficiency, Cost, Optimization, 2019
System Efficiency Rating of Industrial Utilities in Electricity Grids with a high share of Variable Renewable Energies ,Chemical Engineering Transactions , (76),pp 973978 , 2019, https://doi.org/https://doi.org/10.3303/CET1976163
, Large-scale heat pumps: Uptake and performance modelling of market-available devices ,Renewable and Sustainable Energy Reviews , Vol. 137 ,pp 110646 , 2021, https://doi.org/https://doi.org/10.1016/j.rser.2020.110646
, System efficiency Methodology for rating of industrial utilities in electricity grids with a high share of variable renewable energies A first approach ,Renewable and Sustainable Energy Reviews , Vol. 130 ,pp 109969 , 2020, https://doi.org/https://doi.org/10.1016/j.rser.2020.109969
, Large-scale heat pumps: Applications, performance, economic feasibility and industrial integration ,Renewable and Sustainable Energy Reviews , Vol. 133 ,pp 110219 , 2020, https://doi.org/https://doi.org/10.1016/j.rser.2020.110219
, System efficient integration of standby control and heat pump storage systems in manufacturing processes ,Energy , Vol. 181 ,pp 395406 , 2019, https://doi.org/https://doi.org/10.1016/j.energy.2019.05.113
, Optimal operation of a conceptional industrial energy system including a high temperature heat pump, thermal energy storage and wind power. ,Book of Presentations from 3rd HTHP Conference ,pp 323345. , 2022
, Heat and power networks in process design. Part I: Criteria for placement of heat engines and heat pumps in process networks ,AIChE J. , Vol. 29 (5),pp 742748 , 1983, https://doi.org/https://doi.org/10.1002/aic.690290508
, Heat Pump Integration by Pinch Analysis for Industrial Applications: A Review ,Chemical Engineering Transactions , (76),pp 712 , 2019, https://doi.org/https://doi.org/10.3303/CET1976002
, Heat Pump Bridge Analysis Using the Modified Energy Transfer Diagram ,Energies , Vol. 14 (1),pp 137 , 2021, https://doi.org/https://doi.org/10.3390/en14010137
, Thermal Energy Storage Integration Based on Pinch Analysis - Methodology and Application , Vol. 89 (5),pp 598606 , 2017, https://doi.org/https://doi.org/10.1002/cite.201600103
, An Integrated Optimization Model for Industrial Energy System Retrofit with Process Scheduling, Heat Recovery, and Energy Supply System Synthesis ,Processes , Vol. 10 (3),pp 572 , 2022, https://doi.org/https://doi.org/10.3390/pr10030572
, Assessment of the regionalised demand response potential in Germany using an open source tool and dataset ,Advances in Applied Energy , Vol. 1 ,pp 100001 , 2021, https://doi.org/https://doi.org/10.1016/j.adapen.2020.100001
, Hybrid-heating-systems for optimized integration of low-temperature-heat and renewable energy, Chemical Engineering Transactions , Vol. 52 ,pp 10871092 , 2016, https://doi.org/https://doi.org/10.3303/CET1652182
, Economic Multiple Model Predictive Control for HVAC SystemsA Case Study for a Food Manufacturer in Germany ,Energies , Vol. 11 (12),pp 3461 , 2018, https://doi.org/https://doi.org/10.3390/en11123461
, Optimization of Cooling Utility System with Continuous Self-Learning Performance Models ,Energies , Vol. 12 (10),pp 1926 , 2019, https://doi.org/https://doi.org/10.3390/en12101926
, Assessment of Flexibilisation Potential by Changing Energy Sources Using Monte Carlo Simulation ,EnergiesEnergies , Vol. 12 (4),pp 711 , 2019, https://doi.org/https://doi.org/10.3390/en12040711
, Analysis on the demand response potential in hotels with varying probabilistic influencing time-series for the Canary Islands ,Renewable Energy , Vol. 160 ,pp 14801491 , 2020, https://doi.org/https://doi.org/10.1016/j.renene.2020.06.024
, - , Zeitlich und regional aufgelöstes industrielles Lastflexibilisierungspotenzial als Beitrag zur Integration Erneuerbarer Energien (in German, Spatially and temporally highly resolved potential of industrial load flexibility as a contribution to the integration of renewable energies), Dissertation, 2017
Energy consumption in batch thermal processing: model development and validation ,Journal of Food Engineering , Vol. 73 (3),pp 217224 , 2006, https://doi.org/https://doi.org/10.1016/j.jfoodeng.2005.01.040
, Energy Efficiency Measures for Batch Retort Sterilization in the Food Processing Industry ,Chemical Engineering Transactions , (52),pp 163168 , 2016, https://doi.org/https://doi.org/10.3303/CET1652028
, - , Integration von Wärmepumpen zur Dekarbonisierung der industriellen Wärmeversorgung (in German, Integration of heat pumps for decarbonisation of industrial heat supply), Dissertation, 2021
Technical and economic feasibility of sustainable heating and cooling supply options in southern European municipalities-A case study for Matosinhos, Portugal ,Energy , Vol. 153 ,pp 311323 , 2018, https://doi.org/https://doi.org/10.1016/j.energy.2018.04.036
, - , IEA HPT Annex 58 about HTHPs State of the art review, demonstration cases and development perspectives., Book of Presentations from 3rd HTHP Conference 2022, 2022
Potential for Power-to-Heat in the Netherlands ,Report, Delft , 2015
, Kostenoptimierte Speicherintegration für eine dekarbonisierte Industrie (in German: Cost-optimised storage integration for a decarbonised industry) ,DKV Tagung 2019 , 2019
, Renewable Energy Integration for Steam Supply of Industrial ProcessesA Food Processing Case Study ,Energies , Vol. 13 (10),pp 2532 , 2020, https://doi.org/https://doi.org/10.3390/en13102532
, On the potential of temporally resolved GHG emission factors for load shifting: A case study on electrified steam generation ,Applied Energy , Vol. 348 ,pp 121433 , , https://doi.org/https://doi.org/10.1016/j.apenergy.2023.121433
, - https://ec.europa.eu/eurostat/statistics-explained/index.php?title=Natural_gas_price_statistics#Natural_gas_prices_for_non-household_consumers ,
The effect of price-based demand response on carbon emissions in European electricity markets: The importance of adequate carbon prices ,Applied Energy , Vol. 295 ,pp 117040 , 2021, https://doi.org/https://doi.org/10.1016/j.apenergy.2021.117040
, - Short-term greenhouse gas emission factors for electricity consumption within the LCA framework - a case study of Germany and its TSO control zones, 2022,
- https://ec.europa.eu/eurostat/statistics-explained/index.php?title=Electricity_price_statistics#Electricity_prices_for_non-household_consumers ,
Air conditioners, liquid chilling packages and heat pumps for space heating and cooling and process chillers, with electrically driven compressors: Part 2: Test conditions , 2018
, Free cooling of data centers: A review ,Renewable and Sustainable Energy Reviews , Vol. 35 ,pp 171182 , 2014, https://doi.org/https://doi.org/10.1016/j.rser.2014.04.017
, - , Potenziale der Sektorkopplung und Nutzung von Strom aus Erneuerbaren Energien im Wärmebereich in Sachsen-Anhalt, (in German, Potentials of sector coupling and use of electricity from renewable energies in the heating sector in Saxony-Anhalt), 2017
- https://ec.europa.eu/eurostat/statistics- explained/index.php?title=Electricity_price_statistics#Electricity_prices_for_non-household_consumers ,
- https://ec.europa.eu/eurostat/statistics- explained/index.php?title=Natural_gas_price_statistics&oldid=582365#Natural_gas_prices_for_non-household_consumers ,