It is a common understanding that hydrogen (H2) is a very important energy carrier for energy transition. To be widely accepted and used, it has to be produced sustainably, without carbon dioxide (CO2) emissions being released into the atmosphere. Today, hydrogen is almost exclusively produced from fossil fuels. Such processes would need to be replaced by alternatives to produce "green H2". A vast amount of hydrogen is needed to substitute natural gas and other fossil fuels for mobility, energy storage, peak power generation, industry and households. Such an enormous generation will not be possible only through domestic facilities, but at least 50% of the total will be imported to Germany and other EU countries [1]. Electrolysis with renewable electricity can produce green H2, but the quantities are insufficient.
In addition to hydrogen generation from natural gas (with carbon capture and storage (CCS) and/or pyrolysis), the usage of waste biomass is worth investigating. The authors consider gasification the most promising approach regarding biomass and bio-waste with less than 50−70% water content. However, biomass itself does not have a very high mass content of hydrogen. That was shown especially in the previous developments for the so-called Biomass to Liquid technologies (BtL, second generation).
In BtL technologies, a hydrogen to carbon monoxide (H2/CO) ratio of above 2 was required for the Fischer-Tropsch synthesis. This was experienced with facilities like Choren [2], BioLiq [3], and the Güssing facility [4]. The gas with sufficiently high hydrogen content had to be produced externally and added to the synthesis gas. To increase the H2 yield, the approach adopted in the present research uses highly superheated steam at 1,200 °C, described as a general application in [5] or in more detail, especially in combination with biomass and BtL generation, in [6]. Some papers focus on the effects of temperature and Steam to Biomass Ratio (S/B) on the gas composition. In [7], it is shown that higher temperatures influence the reaction rates and favour endothermic reactions. High temperatures, in combination with an S/B ratio of over 1.0, result in high H2 content in the synthesis gas. It is also confirmed by an Aspen Plus simulation for wood residues [8]: increased S/B ratio and temperatures let the hydrogen yield grow in the synthesis gas. We have implemented the usage of superheated steam at 1200 °C with an S/B ratio of over 1.3 to provide sufficient energy and reactants for the endothermic reactions. The superheated steam increases the reaction rate and reduces tar fractions due to reforming. As shown in [9], if both parameters are increased, the tar content decreases, and H2 concentration rises in the synthesis gas.
As this process is conducted without air or oxygen, it has the features of allothermal gasification, or, more accurately, allothermal steam reforming with energy from biomass. Highly superheated steam is simultaneously the energy carrier, gasification agent and oxidising agent used to react with biomass carbon (C). The result is syngas with very high H2 concentration. That process and corresponding development are described in this article.
Another advantage of highly superheated steam is a high concentration of steam excess in the synthesis gas. It facilitates the treatment of tars, which are always present and prevents bigger problems, such as hard depositions generated in tubes and valves. Consequently, it is possible to use an updraft reactor, which is very tolerable regarding the quality of used biomass and wastes. Furthermore, the development of some devices for removing and breaking tars is also being addressed. These components include a device for the thermal cracking of gases, particularly tars, using a heat regenerator and an injection of oxygen to deliver the necessary energy for the cracking reactions. See the two patents [10] and [11], describing a process with different process management and components.
Furthermore, a regenerator system based on the patent [12] condenses tars and cools the tar-contaminated gas. The tars and water are condensed, and the cold is stored in the regenerator. Steam generation, superheating, thermal cracking, and cryo cooling are based on the principle of a special regenerator [13], which has an annular cylindrical bed of bulk material [14]. This regenerator is a so-called pebble heater. The special feature is the radial flow through the bulk material; a quick and efficient heat transfer is enabled due to its high specific surface area. Based on this structure and operation, the pebble heater can achieve a heat recuperation efficiency of up to 98% [15].
Allothermal gasification generally means that the required energy is generated outside the reactor, usually requiring an intensive heat transfer through the reactor walls. It can be achieved using electrical heaters or hot combustion gases, as in the case of heat pipe reformers [16] or the methane steam reforming process. In both cases, the energy transfer and especially the temperatures are limited by the material properties of related components, sometimes resulting in the damage of high-quality metallic tubes for heat pipe [17] or high chrome / high nickel-based tubes for steam reformers [18]. The tests were performed with ceramic tubes for heat pipes, but the temperature in the reaction zone was lower than 900 °C [19]. Generally, it was concluded that using phase change materials in heat pipes considerably limits the operating temperature range [20]. Such problems are avoided when the energy may be added directly to the reactor "in situ", like in Güssing [4], with hot solid particles. Those particles are heated outside the reactor by combusting carbon residues from gasification. That carbon is not available for the process, especially for the reaction with steam to increase H2 yield. The reactor temperature was not higher than 900 °C.
The approach based on an allothermal process with steam adding was used to avoid such problems and achieve the highest possible H2 yield, coupled with high process efficiency. In general, state-of-the-art allothermal steam gasification relies on processes that use catalysts like potassium, sodium, calcium, magnesium or heavy metals [21]. However, catalysts represent another economic reference that must be tailored to the biomass used [22]. It only makes the process unnecessarily more expensive and limits the variety of suitable biomasses.
Superheated steam allows the advantage of the updraft gasifier to be retained and counteract the high tar loads. The use of superheated steam at over 1000 °C has been comparatively less investigated, especially in practical applications. In addition to the tests at the pilot plant, there was only one other test plant in Japan [23]. A study about allothermal steam gasification [24] also addresses increasing steam temperatures and steam/biomass ratios. It shows its effectiveness in reducing tars and increasing the hydrogen content in the synthesis gas.
The added steam must have enough sensible heat to supply the energy for endothermal reactions. That was made possible by extremely high steam superheating. With such an approach, the entire biomass can be converted into syngas. While biomass has a low hydrogen content, hydrogen liberated from biomass and hydrogen from the superheated steam result in a very high hydrogen concentration in the syngas. After separating the hydrogen from the syngas, the waste gases that cannot be used further (e.g., tail gas from the pressure swing adsorption (PSA)) may provide the energy for the steam generation and its overheating. Accordingly, all the waste energy will be returned to the gasification process.
In the presented process, the energy needed for gasification in an allothermal reactor is produced outside by overheating steam at 1,200 °C and transferring it directly ("in situ") into the reactor. The advantage of this technology is that syngas with high H2 content can be produced without using pure oxygen or diluting the syngas with nitrogen. At that temperature, the kinetics of the gasification reactions are considerably improved (the well-known rule of thumb is: 50 K higher temperature = doubled reaction speed). Furthermore, using an updraft gasifier is possible, enabling the usage of low-quality feedstock. Table 1 shows different biomasses and their ultimate analysis. The most important aspect that stands out is the consistently low hydrogen content of around 6% in combination with the high carbon content of over 45%. It shows the effectiveness of pure steam gasification; the water is reduced to hydrogen, thereby significantly increasing the hydrogen content in the synthesis gas by up to 61 vol%.
Ultimate analysis from different biomasses on a dry basis − results in wt% [25]; the last two biomasses (green wastes 1 and 2) are the results of an analysis commissioned by HiTES Holding
Ultimate analysis | Rice husk | Wood chips | Wood residue | Coffee bean | Green wastes 1 | Green wastes 2 | |
---|---|---|---|---|---|---|---|
Carbon | C | 45.80 | 51.19 | 50.08 | 49.40 | 46.30 | 47.60 |
Hydrogen | H | 6.00 | 6.08 | 6.70 | 6.10 | 6.00 | 6.00 |
Oxygen | O | 47.90 | 41.30 | 42.51 | 41.20 | 38.50 | 39.60 |
Nitrogen | N | 0.30 | 0.20 | 0.16 | 0.70 | 1.87 | 1.13 |
Sulphur | S | - | 0.02 | 0.20 | 0.07 | 0.20 | 0.09 |
Chlorine | Cl | - | - | - | - | 0.31 | 0.13 |
- | Ash | 0.80 | 1.16 | 0.36 | 2.50 | 7.20 | 5.60 |
- | Moisture | 12.30 | 20.00 | 5.01 | 10.10 | 30.60 | 70.40 |
Lower calorific value, dry [kJ/kg] | - | - | - | - | 17,300 | 17,800 |
It is well known that different biomasses are very similar in their ultimate analysis, as presented in Table 1. What makes the difference is the amount of ash in the dry biomass. Usually below 10%, it does not greatly influence the calorific value. If different qualities of biomass are used, it is very important to analyze the composition of the ash. It varies significantly; even the same kind of biomass from different locations can have different ash compositions influenced by the variation in the soil makeup. Therefore, the ash composition and ash melting point have to be analyzed in each case. A higher content of alkali elements can significantly reduce the melting point.
The flow direction of the biomass feedstock and the gasification agent steam are counter-current. As typical for such gasifiers, three different process zones are formed. Different temperature zones within the reactor can describe each zone's boundaries, although they are not sharp but 'transitional'. The drying zone is the first zone the feedstock reaches at the top of the reactor, and the last zone is where the syngas must pass before flowing out. In the drying zone, the water from the wet biomass evaporates and mixes with the upcoming stream of syngas. After the dried biomass reaches a temperature of about 250 °C, it enters the pyrolysis zone, which spreads up to the temperature of about 700 °C. In this zone, the large hydrocarbon molecules in the biomass break down into smaller and simpler molecules of gas, liquid and char, as shown in eq. (1):
(1)
The composition and amount of the different pyrolysis products depend on different factors, such as the biomass's heating rate and the residence times of the syngas and biomass. These factors also influence the amount of tars in the syngas. The devolatilization of the biomass ends at about 700 °C, which is also the boundary of the pyrolysis zone. After the devolatilization of the biomass, only solid carbon remains and moves from the pyrolysis zone to the gasification zone. The end of this zone depends on the input temperature of the steam, in this case 1,200 °C. Because of the 'transitional' boundaries between the gasification and pyrolysis zones, homogeneous reactions can also occur in the hotter parts of the pyrolysis zone. Three heterogeneous and two homogeneous reactions can be identified as the main reactions in the gasification zone. The heterogeneous reactions are the Boudouard Reaction, eq. (2), the Water Gas Reaction, eq. (3), and the Methanation Reaction, eq. (4).
(2)
(3)
(4)
The two homogeneous reactions are the Water Gas Shift Reaction, eq. (5), and the Steam Reforming Reaction, eq. (6).
(5)
(6)
All of these are equilibrium reactions, which means that the concentration of every single reactant and the temperature at which the reaction takes place are influenced by the side of the equation of the thermodynamic equilibrium. These reactions can occur in any of the three zones within the gasifier. Still, the activation energy and kinetic aspects prevent them from taking place in the colder zones of the gasifier in any significant amount. Due to the high excess of steam (i.e., the gasification agent) and its high temperature, the reaction equilibrium in eq. (3) is located on the side of the products, and the char could fully react. Only the ash leaves the gasification zone through the bottom of the gasifier, whereas the syngas flows to the pyrolysis zone.
The influence of superheated steam on tars because of biomass gasification has significant advantages due to tar reforming, eq. (7).
(7)
The tars react with steam, producing hydrogen and carbon monoxide, thus lowering the amount of tar that leaves an updraft reactor. Steam also acts as a solvent for water-soluble tar components, preventing clogging of different facility parts. Steam is the gasification agent and energy carrier, producing a high steam-to-biomass ratio. Other authors have shown that increasing this ratio decreases the tar yield [26]. It was shown by Li et al. [27] that a high steam content in the syngas can help eliminate the heavy tars and increase the hydrogen yield and the carbon conversion.
A pilot facility for allothermal biomass gasification with extremely high steam superheating has been erected for the first time in technical application. The construction started in early 2008. Even the first tests demonstrated the outstanding advantages of the proposed technology, using the Pebble-Heaters (regenerators with spherical bulk material) for generating steam at such extremely high temperatures. It was the first worldwide gasification test with very high steam superheating at a 100−200 kg/h biomass capacity pilot facility. Later, there was a similar test facility in Japan [23], with lower temperatures (mostly 900−1,000 °C) and a resulting H2 concentration in the synthesis gas of about 40 %. The temperature was limited by the regenerator technology used for steam preheating. The results were considerably worse, and the facility size was significantly larger, although the capacity was smaller, thus clearly demonstrating the importance of higher temperatures. The same group of authors performed a numerical performance analysis [28] using parametric steam temperature between 1,200 K and 1,500 K. It was proved that higher temperature leads to considerably higher mass loss rate of the char at the outlet (i.e. inlet of the steam), higher H2 fraction and lower CO fraction in the synthesis gas.
At that time, the objective of the pilot facility was to generate synthetic fuels through the Fischer-Tropsch synthesis, the so-called second-generation BtL (Biomass to Liquid). Therefore, it was necessary to produce a synthesis gas rich in hydrogen to get an H2/CO ratio of about 2 or somewhat higher. The proposed process achieved the goal of using superheated steam without adding external hydrogen. In fact, in some cases, that ratio was 5 or even more, so the steam temperature has been reduced mostly to 1,100 °C, or some oxygen has been added to the steam to increase the amount of CO. The test results obtained are per the mentioned numerical analysis [28]. After the reactor, a cyclone was installed to remove heavy tar from the synthesis gas. Usually, there is no need for a dust filter combined with an updraft gasifier, but it was installed later to enable tests with higher outlet temperatures. A newly developed thermal cracker works at operating temperatures between 1,000 °C and 1,400 °C The thermal cracker is based on the two patents [10] and [11]; they describe the advantages of a radial flow through a bed material with simultaneous injection of oxygen to supply energy for the cracking reactions. Its role was to break down lighter tars, which were not separated in the cyclone, and to crack the methane molecules to increase the hydrogen yield. Although some tests with natural minerals as catalysts were performed, the best results were achieved with alumina pebbles, enabling very high temperatures. After preheating synthesis gas from the reactor outlet temperature to the operation temperature, some small amount of oxygen has been added. In that way, the energy required for cracking was generated. For that application, the experience with the Pebble-Heater technology was used again. Due to very high heat recuperation, the energy requirement for the entire system remained low.
After the cracker, the gas was cooled down, and, in a condenser, the remaining water content was removed at 25−30 °C. A cryocooler was designed and installed to facilitate further removal of the condensate and extremely volatile tars [12]. The synthesis gas was again cooled down to 0 °C or even −5 °C in a packed-bed column. After condensing water and volatile tars (like naphthalene), the gas was heated in a second column, almost to the same inlet temperature of about 20 °C to 25 °C. An external cooler was required to cover energy lost through the condensation and wall losses. Even here, an intermittent operation of those columns was required. Again, energy consumption was very low due to the high recovery. An active carbon filter was installed to remove any remaining tar residues or water condensate. At the end, a filter filled with zinc oxide (ZnO) pellets was used to remove the last traces of hydrogen sulphide. In that way, a completely clean synthesis gas was obtained, as presented in Table 3. After the compression to the required pressure, it was suitable for the Fischer-Tropsch reactor filled with the required catalyst.
The pilot facility (Figure 1) was in operation with 50−200 kg/h of different kinds of biomass, such as low-quality wood chips, straw, waste grains from beer breweries, residues from biogas digestion, wild nuts and others. The first tests started in late 2008, and the facility was subsequently enlarged and improved. The first BtL fuels were generated already in 2009.
Photo of the pilot facility; from left to right: cracker, reactor, biomass bin
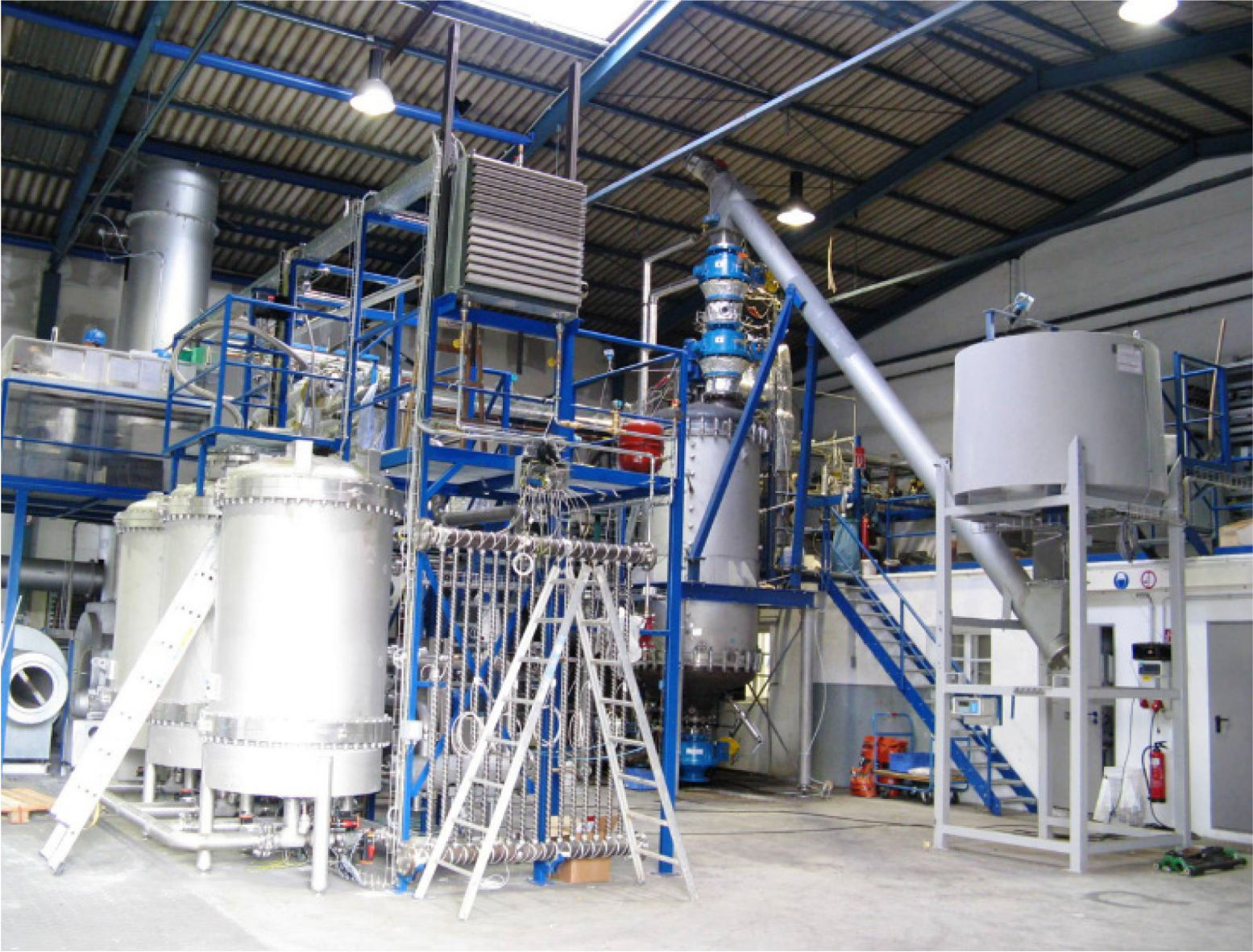
The test results from the experiments at the pilot plant were very promising. Figure 2 illustrates a measurement over 24 hours; the uppermost measurement line shows the hydrogen content in the gas. On average, it was 51.3 vol%, with peaks at almost 60 vol%. The second line, in the range of 30 vol%, shows the CO2 content in the syngas. The third line is the CO content, which indicates that the required ratio of H2/CO is well above 2. The last measurement line represents the methane (CH4) content.
Gas composition during a test over 24 hours; T = 360 °C, average composition data in vol%: H2 51.32; CO 7.75; CH4 2.73; CO2 30.11

The discontinuity of the biomass feeding caused gas composition variations through the dome valves on the top of the reactor. Based on the data, important findings in the field of high-temperature applications were recorded concerning the reactor material, geometry, flow control and the handling of tars. Table 2 shows the ultimate analysis of a tar sample extracted from the cyclone. The empirical formula determined from the mass proportions of carbon, hydrogen, and oxygen of the tar sample (C1H1,8O0,5) indicates a high proportion of long-chain, heavy hydrocarbons. Table 3 shows the concentration of hydrocarbons in the dry syngas before and after the activated carbon filter but before the zinc oxide (ZnO) filter. There are hardly any long-chain tars, only highly volatile hydrocarbons such as benzene and toluene. After the ZnO filter, the last traces of hydrogen sulphide were removed, and all pollutants were below the detection limits.
Ultimate analysis and lower calorific value of a tar sample extracted from the cyclone with the used testing methods
Test parameters | Testing methods | Test results | Units |
---|---|---|---|
Carbon | DIN 51 732 | 59.5 | wt% |
Hydrogen | DIN 51 732 | 6.95 | wt% |
Nitrogen | DIN 51 732 | < 0.5 | wt% |
Oxygen | DIN 51 732 mod. | 33.1 | wt% |
Phosphorus | DIN EN 14107 | 109 | mg/kg |
Chlorine | DIN 577-3 | 0.025 | wt% |
Lower calorific value | DIN 900-2 mod. | 24,363 | kJ/kg |
Sulphur | DIN EN ISO 20884 | 192 | mg/kg |
Laboratory tar analysis of the synthesis gas before and after the activated carbon filter at 200 kg/h and steam at 1,100 °C
Lab number | H11-239 9.4-VA | H11-240 9.4-NA |
---|---|---|
Sample designation | [mg/m3] | [mg/m3] |
Pyridine | <0.1 | <0.1 |
Hydrogen sulphide | 84.0 | 0.32 |
Carbonyl sulphide | <0.1 | <0.1 |
Carbon disulphide | <0.1 | <0.1 |
Furan | <1.0 | <1.0 |
Methylfuran | 5.0 | <1.0 |
Dimethylfuran | 13.0 | <1.0 |
Cyclopropane | <1.0 | <1.0 |
Cyclopropene | <1.0 | <1.0 |
Cyclobutene | <1.0 | <1.0 |
Methylcyclopentane | <1.0 | <1.0 |
Dimethylhexadiene | <1.0 | <1.0 |
Indene | <1.0 | <1.0 |
Naphthalene | <1.0 | <1.0 |
Phenol | <1.0 | <1.0 |
Benzene | 7,100.0 | 22.8 |
Toluene | 89.8 | <0.1 |
Ethylbenzene | <0.1 | <0.1 |
m+p-Xylene | <0.1 | <0.1 |
o-Xylene | <0.1 | <0.1 |
Styrene | <0.1 | <0.1 |
i-Propylbenzene | <0.1 | <0.1 |
n-Propylbenzene | <0.1 | <0.1 |
1.3.5-Trimethylbenzene | <0.1 | <0.1 |
1.2.4-Trimethylbenzene | <0.1 | <0.1 |
1.2.3-Trimethylbenzene | <0.1 | <0.1 |
2-Ethyltoluene | <0.1 | <0.1 |
3.4-Ethyltoluenes | <0.1 | <0.1 |
i-Propyltoluene | <0.1 | <0.1 |
Those values are considerably better than tar concentrations in the order of g/m3, reported in [16] and related publications. Such clean syngas was introduced into the Fischer-Tropsch reactor without danger of catalyst inactivation.
The results were also important for gas cleaning without catalysts, only combining a pure thermal cracker and cryocooler. Catalysts represent a further economic factor and should be adapted to the respective feedstock. This aspect would limit the range of input materials used for the updraft gasifier, being its most valuable advantage. It can be concluded that an allothermal operation with energy input directly from the gasification agent steam offers significant advantages in terms of tar handling and removal. Therefore, the disadvantage of the reactor's high tar formation rate is eliminated. It is, therefore, possible to produce a synthesis gas with high hydrogen concentration with such state-of-the-art components and an innovative, purely thermal process. The value of the presented pilot facility was further proven by its continuous (24/7) and reliable three-month operation.
The development and tests on the pilot plant were performed from 2008 onward and successfully completed in 2014 with Technology Readiness Level (TRL) 5. The current hydrogen ramp-up has made this technology attractive again. The results from the pilot plant have shown that the cleaned and dried syngas contained a high concentration of hydrogen, even >60 vol%. Therefore, it was evident that the next step – TRL 7 – was to replace the Fischer-Tropsch reactor with a Pressure Swing Adsorption (PSA) facility and separate the hydrogen in its pure form.
Figure 3 illustrates the process flow diagram in a simplified manner. After the dryer, the biomass is transported into the reactor via a conveyor belt. The gasification of the biomass produces synthesis gas in the reactor, and its cleaning begins immediately afterwards. In the cyclone, fractions of tars and particles are removed and transported back into the high-temperature zone of the reactor by a tar pump. The particle filter removes particles to further purify the synthesis gas from pollutants. Afterwards, the synthesis gas flows towards the high-temperature cracker, where the remaining tars are removed from the synthesis gas by adding a small amount of oxygen to sustain a high cracking temperature.
Flow sheet of the demo plant process
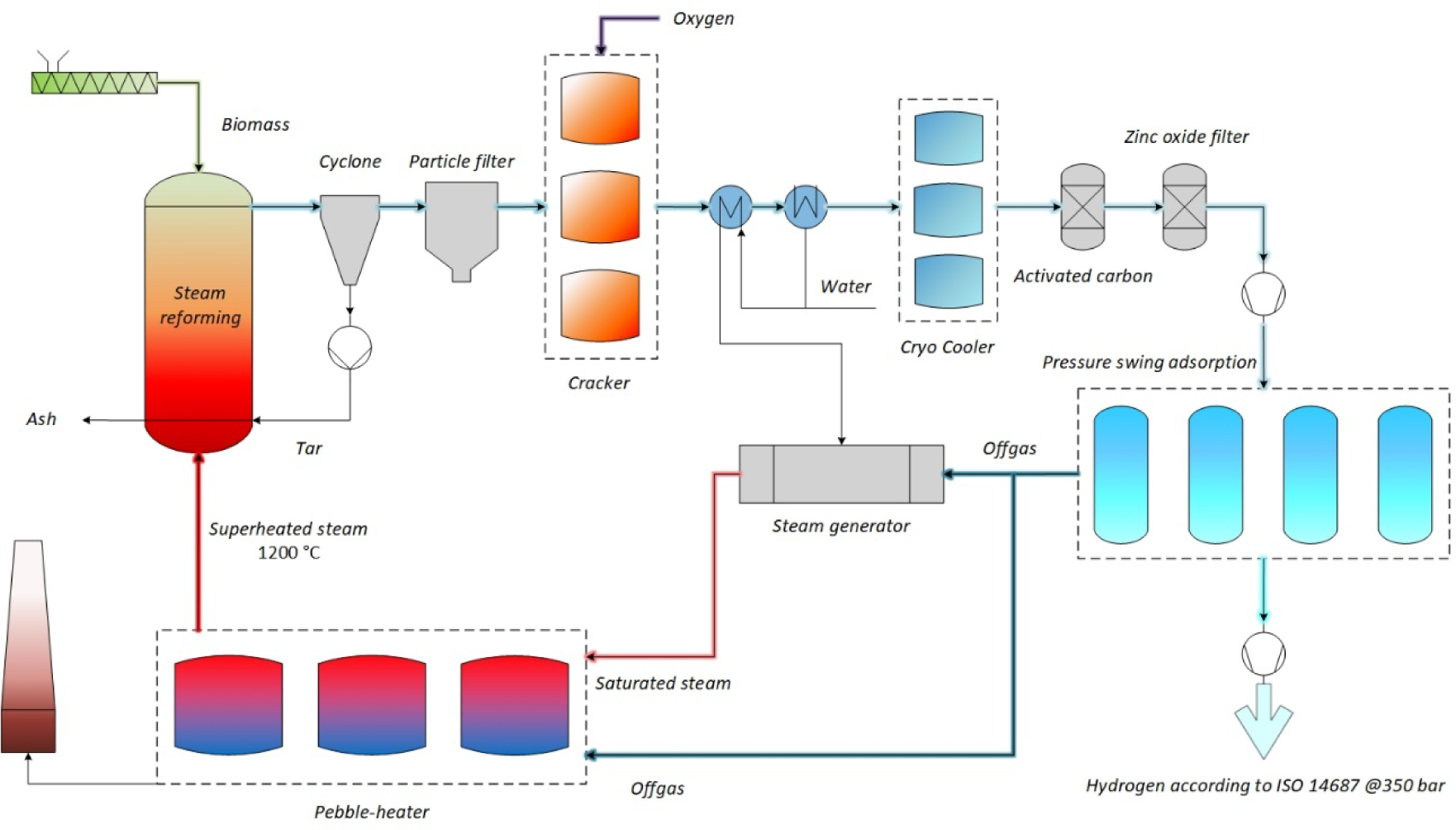
In the next step, the synthesis gas is cooled down in a heat exchanger and dried in a condenser. The cooling circuit is created by mixing fresh water and condensate. The preheated feed water is then supplied to the steam boiler to generate saturated steam. After cooling, the gas is dried in a cryocooler to remove the remaining condensate and extremely volatile tars. The synthesis gas must be purified of all potential pollutants to prevent undesired constituents, so the activated carbon filters out any remaining hydrocarbons and the zinc oxide filter will remove the last hydrogen sulphide traces.
To achieve TRL 7, a demo plant was designed with an input of 2,000 kg/h dry biomass. Due to the high hydrogen content, the demo plant can convert the biomass at a ratio of 10:1, achieving a hydrogen output of 200 kg/h. The biggest changes related to the pilot plant took place after the ZnO filter. A gas compressor follows the filter to achieve the required inlet pressure for the PSA. The PSA is designed based on the maximum allowable concentrations of other gases (e.g. CO) to operate a polymer electrolyte membrane (PEM) fuel cell. The remaining gas (tail gas from PSA) contains mainly CO2, CO, CH4 and a small amount of unseparated H2. As mentioned, it is used primarily to generate steam and to superheat it to 1,200 °C. If there is still some surplus of tail gas, it will be used for additional biomass drying. This facility will be trimmed to further maximise H2 yield and not achieve the optimal H2/CO ratio as in the pilot facility. Therefore, the steam temperature will be at least 1,200 °C. Still, higher temperatures will also be operated to use the recorded temperature effect on the H2 concentration (as reported in [28]). Like in the pilot facility, some lime addition to the feed will be used to suppress the ash melting in case of biomass with higher alkali content. In this case, the extracted hydrogen will be compressed to the application pressure − at 350 bar. Due to this process configuration and the integrated, intensive recuperation of energy with the Pebble-Heater technology, it is possible to achieve a process efficiency of up to 70%.
The exhaust gases from the tail gas combustion contain only CO2, H2O, N2 and O2. If pure oxygen would be used for combustion in an oxyfuel process, ideally at stoichiometric combustion conditions (air-to-fuel ratio equal to 1), only CO2 and H2O would be generated. It also opens up new synergies: first, oxygen from the electrolysis process can be used directly, and CO2 can be easily separated. Since CO2 is biogenic, Bio-Energy Carbon Capture Utilization and Storage (BECCUS) makes the whole process CO2-negative and significantly reduces greenhouse gas pollution. Consequently, three new and independent patents for producing hydrogen from biomass through allothermal steam reforming have been filed.
Mass balance of the demo plant
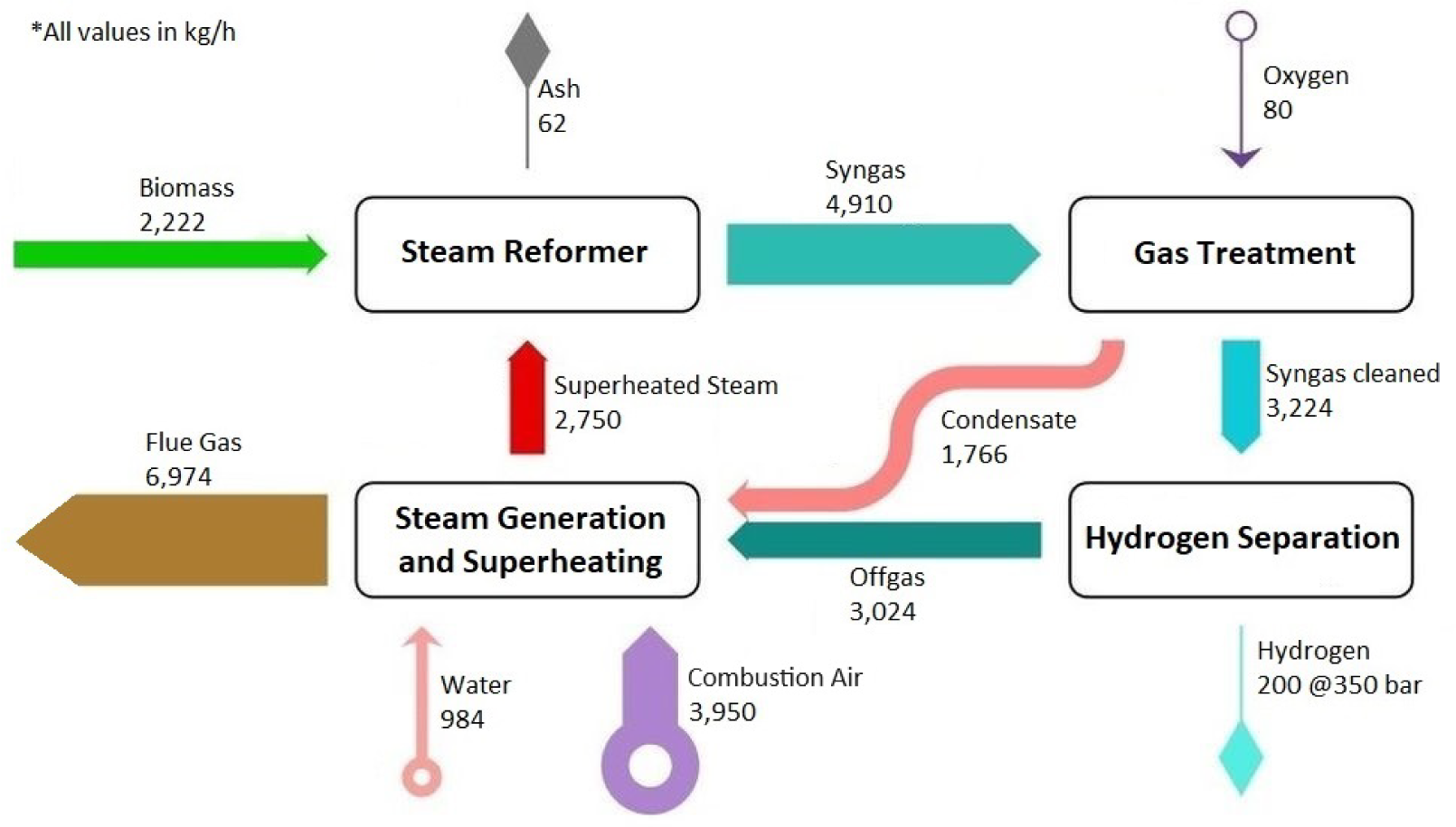
Energy balance of the demo plant
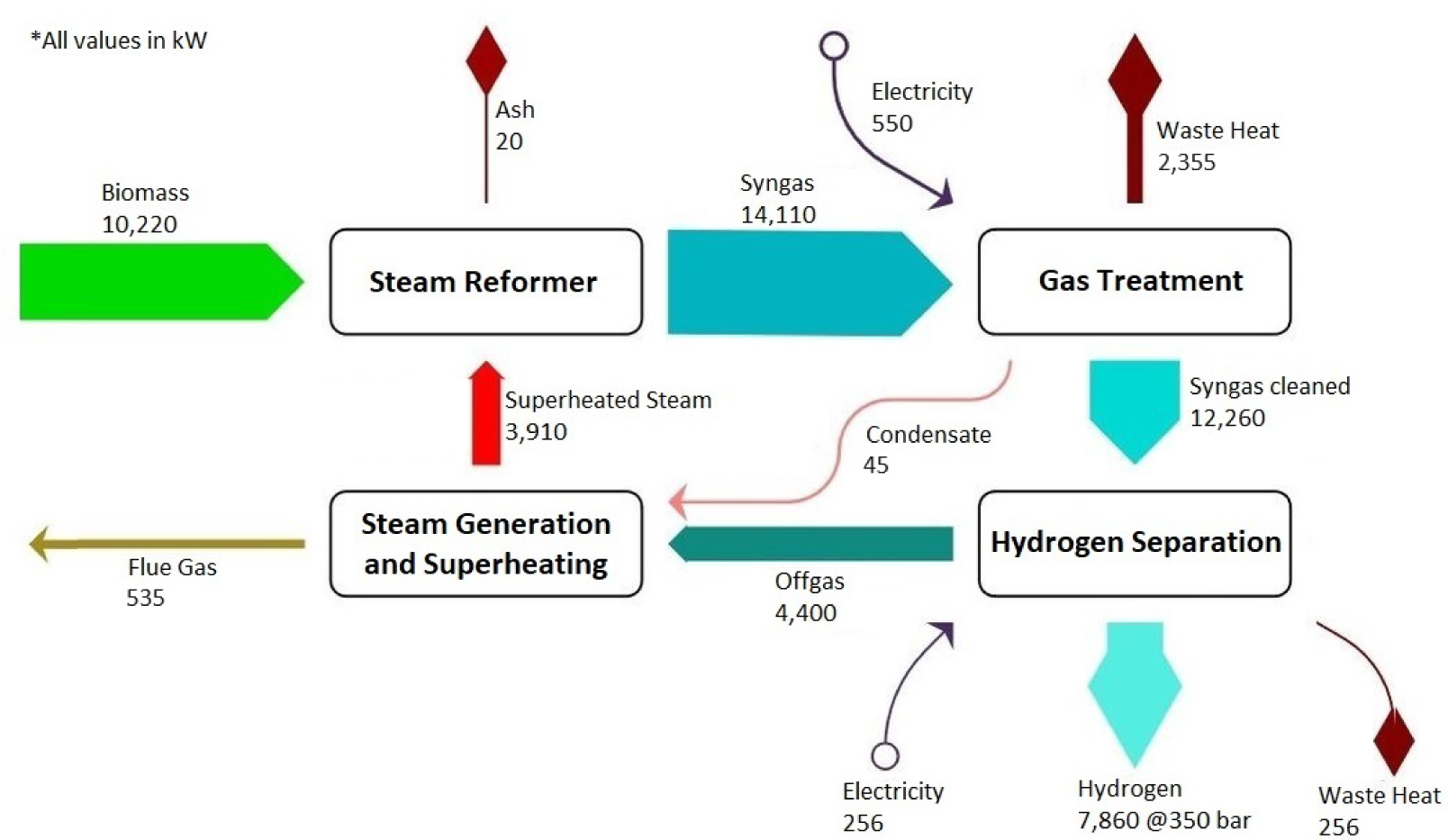
In Figure 4 and Figure 5, the mass and energy balances of the demo plant are presented. The biomass goes in the steam reformer (updraft reactor) with a remaining water content of 10% and is brought into contact with the superheated steam at 1,200 °C from below. The resulting syngas is then treated, tars are separated or eliminated, and the excess water in the gas is condensed out.
Figure 6 presents a three-dimensional view (Computer Aided Design Model) of the plant and illustrates how the components are connected.
3D-model of the demo facility
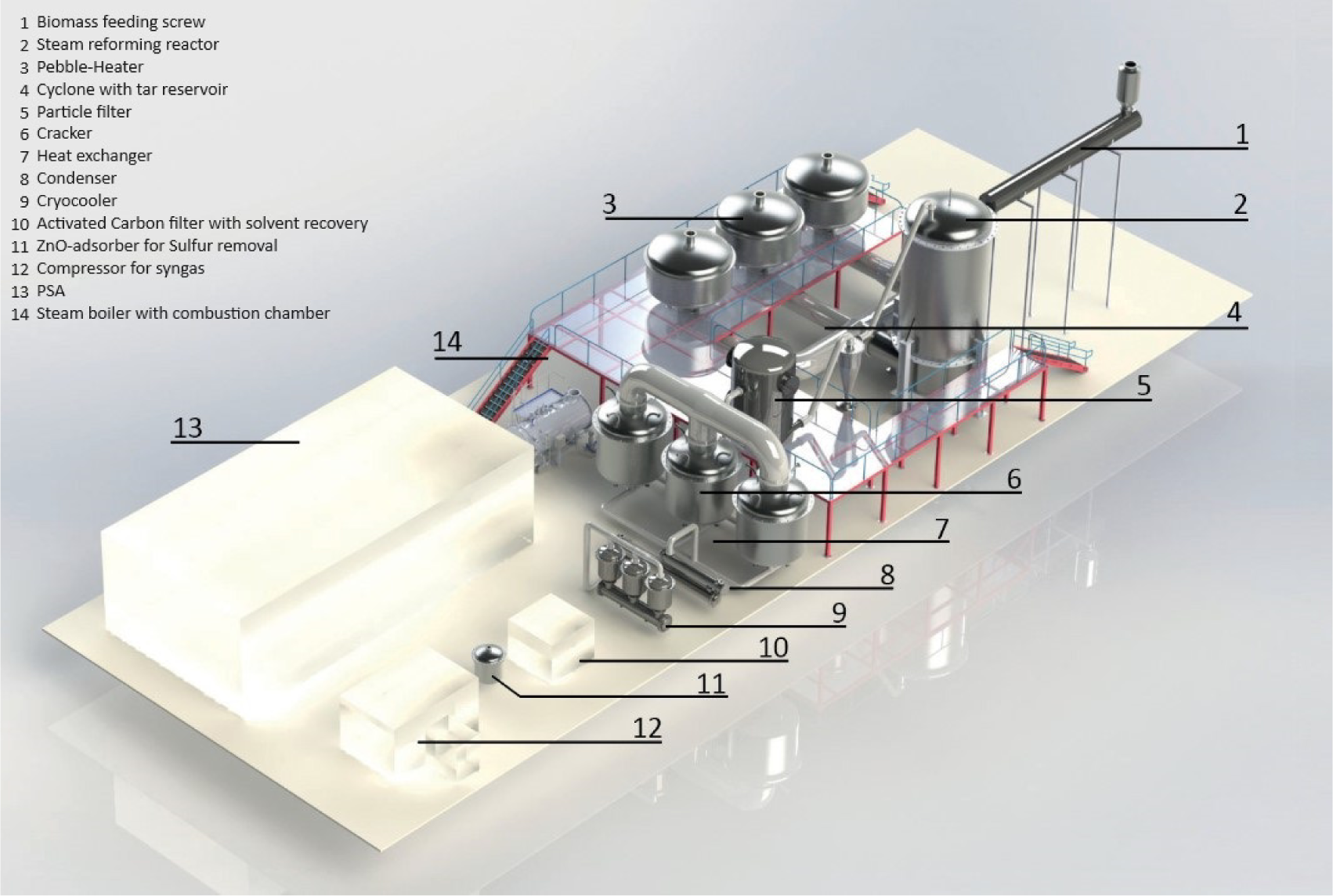
Optimal process control and switching between the regenerators are required for an efficient process. It should be noted that all three vessels for Pebble-Heaters, crackers, and cryocoolers are necessary for continuous operation. With the position of the relevant valves changed, it is possible to always have at least one of the three vessels in the required operation phase. The feeding of the input material is controlled depending on the synthesis gas temperature at the reactor exit. In that way, the capacity of the plant and the required amount of steam are controlled in case the feedstock's water content varies.
The system's economic efficiency is considerably improved compared to other hydrogen production paths. The required technology is simple; few inexpensive input materials are used, and due to the high energy recovery through the pebble heater, there is reduced energy loss. This situation is also reflected in the production price of hydrogen (already compressed to 350 bar), which can have an average value of around 3.10 €/kg, depending on the scenario. Such an average price is considerably lower than hydrogen imported from North Africa. In these scenarios, the input biomass is paid for, but there are also residues with negative prices that would significantly reduce production costs. In economic terms, comparatively low sales prices of 6−9 €/kg can be offered to the market, but a very high internal rate of return (IRR) can be attained. In the case of a sales price of 7 €/kg, the IRR is already 17%, calculated with a high biomass price of 120 €/t. There is also income generated from the GHG quota (if applied in the transport sector), which can be counted twice in Germany as of January 30, 2024. Other sources of income can be biogenic benzene and biogenic CO2. In Table 3, a relatively high proportion of benzene in front of the activated carbon filter can be seen; this can be marketed with suitable solvent recovery. The biogenic CO2 can easily be captured with high purity using an oxyfuel process. The oxygen required for this can be supplied by an electrolyzer nearby or generated directly on-site using an O2 PSA.
The main advantage of preheating steam to 1,200 °C is that it enables allotherm steam reforming, using the energy from biomass. In that way, there is no need to introduce oxygen (pure or with air) into the reactor, which reduces the amount of molecular hydrogen. Only the waste gas (tail gas from PSA) is used for the external combustion for steam generation and superheating. Excess steam in the syngas enables much easier handling of tars and their removal. Therefore, it is possible to use an updraft reactor, the simplest gasification technology. It can accept different kinds of waste biomass, which positively influences the economy of the process. The heavier tar fraction is separated in a cyclone and introduced back in the hottest zone of the reactor. Newly developed components for treating the syngas, pure thermal cracker and cryocooler based on regenerative principles, enable the production of a very clean gas suitable for the equipment with very sensitive catalysts (like the Fischer-Tropsch reactor). The results obtained from the pilot facility have demonstrated the importance of high-temperature steam for high hydrogen yield, high hydrogen concentration, and easier handling and removal of tars.
At the same time, the components used are mainly based on temperature-resistant ceramics, which were used in previous technology development. Material problems are thus avoided at a very reasonable cost. The experience from the pilot facility and observed advantages will be used in a demonstration facility for pure hydrogen generation, resulting in:
high process efficiency, up to 70%;
high hydrogen yield (from 1 t of input biomass, it is possible to get 100 kg of hydrogen, i.e. 10 wt%);
very high quality of the produced hydrogen (5.0, i.e. 99.999%), suitable for the most demanding applications;
CO2-emission less than 1 kgCO2/kgH2, or even negative with BECCUS;
power consumption less than 5 kWh/kgH2, mostly for compression;
considerably lower production costs than electrolysis based on renewable electricity, at least at current prices in Germany.
Abbreviations | |
BECCUS | Bio-Energy Carbon Capture Utilization and Storage |
BtL | Biomass to Liquid |
IRR | Internal Rate of Return |
PSA | Pressure Swing Adsorption |
S/B | Steam to Biomass |
TRL | Technology Readiness Level |
- , , Options for the Import of Green Hydrogen to Germany by 2030: Transport Routes – Country Assessments – Implementation Requirements (German). in Future Energy Systems. acatech - Deutsche Akademie der Technikwissenschaften, 2022
- , Industrial Scale Hydrogen Production from Biomass via CHOREN’sUniqueCarbo-V-process, in 18th World Hydrogen Energy Conference 2010 - WHEC 2010: proceedings. 3 part 2: Hydrogen production technologies Parallel sessions book, vol. 3, D. Stolten and T. Grube, Eds., in Schriften des Forschungszentrums Jülich Reihe Energie & Umwelt, no. 78, vol. 3., Jülich: Forschungszentrum, IEF-3, 2010
The bioliq® Entrained‐Flow Gasifier – A Model for the German Energiewende ,ChemBioEng Reviews , Vol. 7 (4),pp 106–118 , 2020, https://doi.org/https://doi.org/10.1002/cben.202000006
, - Biomass CHP Plant Güssing – Using Gasification for Power Generation, 2003, https://api.semanticscholar.org/CorpusID:168167823
- Carbonic raw material e.g. coal, gasifying method, involves using superheated water vapor as gasification agent and energy carrier for gasification reaction at temperature above specified degree Celsius, http://depatisnet.dpma.de/DepatisNet/depatisnet?action=bibdat&docid=DE102007050566A1, [Accessed: Jan. 25, 2024]
- Method and device for converting carbonaceous raw materials, 2011, https://patents.google.com/patent/US20110035990/en, [Accessed: Jan. 25, 2024]
Simulation and Techno-Economic Assessment of Hydrogen Production from Biomass Gasification-Based Processes: A Review ,Energies , Vol. 15 (22),pp 8455 , 2022, https://doi.org/https://doi.org/10.3390/en15228455
, - , Aspen Plus simulation of biomass gasification for different types of biomass, presented at the The 60th SIMS Conference on Simulation and Modelling SIMS 2019, August 12-16, Västerås, Sweden, 2020
Influence of pressure, temperature and steam on tar and gas in allothermal fluidized bed gasification ,Fuel , Vol. 99 ,pp 204–209 , 2012, https://doi.org/https://doi.org/10.1016/j.fuel.2012.04.022
, - Process and device for cracking gases (German), http://depatisnet.dpma.de/DepatisNet/depatisnet?action=bibdat&docid=DE102012111894A1, [Accessed: Jan. 31, 2024]
Method and Apparatus for the Conversion of Long-Chain Hydrocarbons (German) ,German Patent 102012111900A1 , 2012
, - Device and method for removing condensable gases from gas streams (German), 2014, https://register.dpma.de/DPMAregister/pat/register?AKZ=1020141124014&CURSOR=0, [Accessed: Feb. 11, 2024]
- Regenerator, http://depatisnet.dpma.de/DepatisNet/depatisnet?action=bibdat&docid=EP000000620909B1, [Accessed: Jan. 31, 2024]
- Process for the operation of a regenerator and regenerator, 2002, http://depatisnet.dpma.de/DepatisNet/depatisnet?action=bibdat&docid=US000006334265B1, [Accessed: Jan. 31, 2024]
- , Regenerative thermal oxydizers based on the pebble-heater technology, presented at the INFUB 2000 - Industrial Furnaces and Boilers, Portugal, 2000
Biomass heat pipe reformer—design and performance of an indirectly heated steam gasifier ,Biomass Conv. Bioref. , Vol. 4 (1),pp 1–14 , 2014, https://doi.org/https://doi.org/10.1007/s13399-013-0102-6
, Gasification of woody biomass in a novel indirectly heated bubbling fluidized bed steam reformer ,Fuel Processing Technology , Vol. 224 ,pp 107003 , 2021, https://doi.org/https://doi.org/10.1016/j.fuproc.2021.107003
, Creep Failure of Reformer Tubes in a Petrochemical Plant ,Metals , Vol. 9 (10),pp 1026 , 2019, https://doi.org/https://doi.org/10.3390/met9101026
, Ceramic Heat Pipes for High Temperature Application ,Energy Procedia , Vol. 120 ,pp 140–148 , 2017, https://doi.org/https://doi.org/10.1016/j.egypro.2017.07.147
, Allothermal Fluidized Bed Reactor for Steam Gasification of Biomass ,Instrumentation Science & Technology , Vol. 43 (4),pp 390–428 , 2015, https://doi.org/https://doi.org/10.1080/10739149.2015.1010090
, Catalysts for gasification: a review ,Sustainable Energy Fuels , Vol. 3 (3),pp 656–672 , 2019, https://doi.org/https://doi.org/10.1039/C8SE00614H
, Bio-hydrogen production from steam reforming of liquid biomass wastes and biomass-derived oxygenates: A review ,Fuel , Vol. 311 ,pp 1–23 , 2022, https://doi.org/https://doi.org/10.1016/j.fuel.2021.122623
, High temperature steam-only gasification of woody biomass ,Applied Energy , Vol. 87 (3),pp 791–798 , 2010, https://doi.org/https://doi.org/10.1016/j.apenergy.2009.09.035
, Experimental Analysis of Brewers’ Spent Grains Steam Gasification in an Allothermal Batch Reactor ,Energies , Vol. 12 (5),pp 912 , 2019, https://doi.org/https://doi.org/10.3390/en12050912
, Numerical investigation of different biomass feedstock on syngas production using steam gasification and thermodynamic analysis ,Chemical Product and Process Modeling , Vol. 0 (0), 2023, https://doi.org/https://doi.org/10.1515/cppm-2023-0056
, Biomass gasification with pure steam in fluidised bed: 12 variables that affect the effectiveness of the biomass gasifier ,IJOGCT , Vol. 1 (1/2),pp 194 , 2008, https://doi.org/https://doi.org/10.1504/IJOGCT.2008.016739
, Experimental study and modeling of heavy tar steam reforming ,Fuel Processing Technology , Vol. 178 ,pp 180–188 , 2018, https://doi.org/https://doi.org/10.1016/j.fuproc.2018.05.020
, Analysis of an updraft biomass gasifier with high temperature steam using a numerical model ,Applied Energy , Vol. 90 (1),pp 38–45 , 2012, https://doi.org/https://doi.org/10.1016/j.apenergy.2010.12.058
,